Tool Breakage on Lathes and Turning Centers
The missed tool breakage detection during a machining process can potentially produce devastating effects on the production.
First of all, every part that the damaged tool will cut from the moment of breakage will turn into scrap. This issue is amplified in case of unmanned production, where several hours may pass before an operator recognizes such problem.
Secondly, in processes like boring, tools used on a part after the broken one are likely to be damaged because they should remove more material than expected and more material than what is suitable for their features.
To avoid that kind of waste and costs, it is compulsory to equip the machine with effective tool integrity check systems, able to recognize a possible breakage right after a machining process.
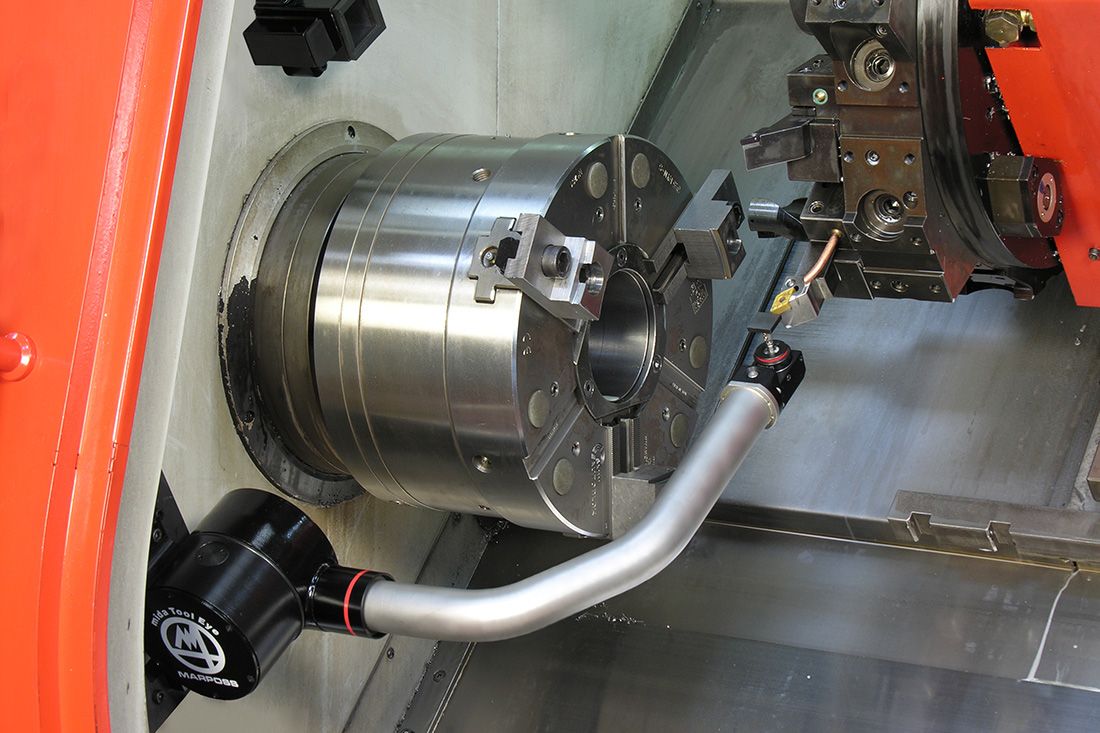
Marposs provides different solutions for tool breakage detection and integrity check on lathe and turning centers.
Marposs products for tool breakage take as initial reference the dimensions in tool table and require the definition of the maximum acceptable breakage tolerance by the operator. After machining, the check is performed: if a breakage greater than the tolerance is detected, an alarm signal is generated in order to replace the damaged tool, avoiding production issues.
- Increase of production quality
- Increase of machine productivity
- Scrap reduction, especially in unmanned operations
- Automatic tool integrity check
- Quick check
- Facilitation of operator’s activities
Different systems for tool breakage are available for lathes and turning centers:
- Mida Arms, high positional repeatability measurement arms used for tool setting and checking on lathes. They consist of a fixed base and a mobile arm and a touch probe is mounted on the mobile arm
- TBD, Tool Breakage Detector, a product dedicated to axial integrity check, mainly for solid body tools (e.g. drills and tapping tools). It is able to recognize very small tools, down to 0.15 mm, in less than a second
- Mida Laser, non-contact system which, besides integrity check, allows to perform different measurements and cutter profile scanning
- Vision Tool Setting, ideal for micro-tools and applications requiring extraordinary metrological performances (measurement accuracy less than 2 microns). Dedicated software cycles are available for integrity check of turning applications