Monitoring Solutions for Gear Cutting Machines
When cutting gears, optimizing tool life offers a significant potential for productivity improvements and tool costs. Early replacement wastes usable tool life; if the wear width is too wide, reconditioning requires excessive sharpening. This reduces the number of possible regrinds. Only monitoring of the actual wear ensures replacement at the correct time. Productivity gains using ARTIS process monitoring systems.
The solution is proven to be extremely useful in tool life optimization and control or optimizing cycle times and tool life from a total cost perspective.
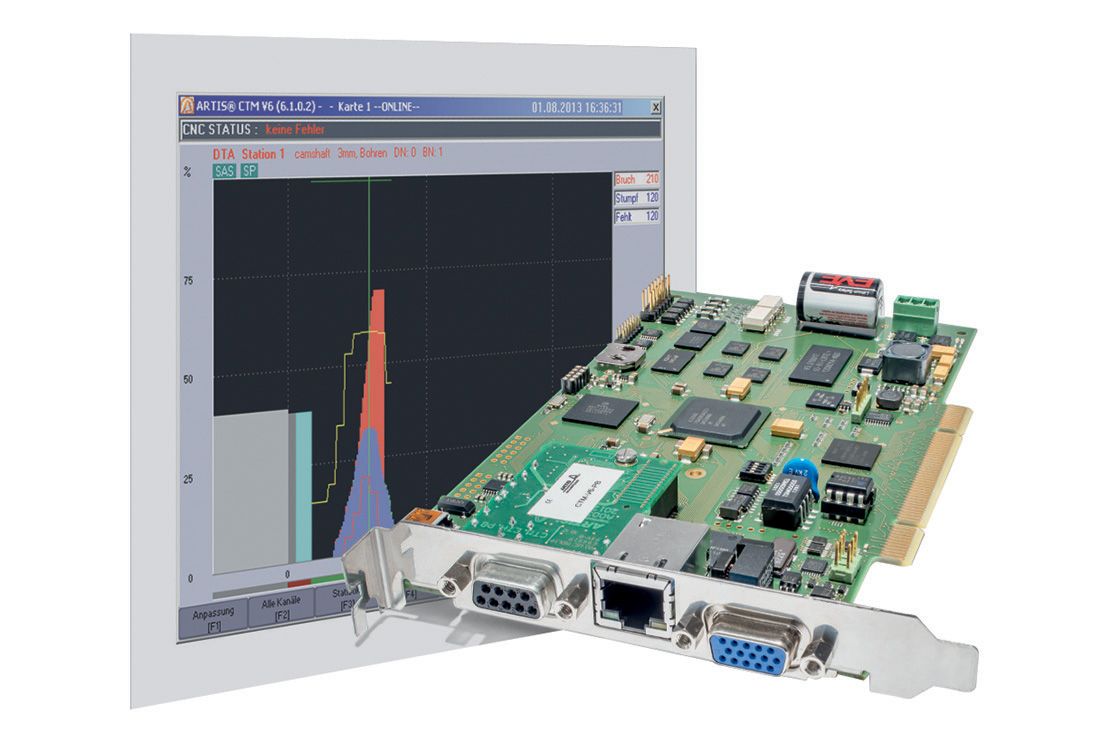
The electronic and integrated monitoring system detects intermittent tool damage associated with special cause or overrunning and could stop machine and or identify reject to protect machine, part and tool. The system indirectly detects wear, breakage and cratering in the hob cutter teeth, part misload, part slippage, and concentricity problems by a clear visualization of the process.
Process data is collected either digitally using the spindle torque data or by additional sensors, to be processed in the Tool and Process Monitoring System and visualized on a monitor of a Windows-based operating panel. Alarm limits allow identification of tool breakage or wear. By using an additional vibration sensor, cutting process vibrations can be monitored and evaluated.
Optimization using statistics:
The optional statistic function offered by the CTM process monitoring system shows tool tending and tool change frequency. The option helps to identify the right limits and to optimize the cutting parameters. The statistical data can be used to compare cycles and tools. The data recorder allows a tracking of past cycles. valuable information based on long-term data acquisition. In addition to wear control, the data can also be used for optimization, e. g. adapting the cutting parameters.
- Wear-dependent tool change or need-driven replacement of inserts
- Maximum tool life
- Maximum number of tool regrinds
- No wasting of valuable service life
- Dependable recognition of tool breakage
- Consistent product quality
- Machine protection
- TMU (True Power sensors)
- Genior Modular and CTM (DTA and/or sensors)
- License code for a Gear Hobbing strategy (option for CTM)