Part Inspection and Setup on Lathes and Turning Centers
One of the main issues in the production area using lathes or turning centers is caused by scrap parts due to wrong machining. One of the way’s to avoid scrap is to know how the workpiece is fixed on the spindle (the real position with respect to machine axes) and also to measure / inspect the work piece after the machining process. To perform this kind of check, it is necessary for the machine to be equipped with part probing systems: Touch probes.
Part probing identifies measurement operations that are carried out entirely inside the lathe or turning center, in the very same conditions in which the cutting takes place. In this way, the operator gets the same data provided by CMMs, but in a faster and more meaningful way. In fact, it is true that CMMs provide very precise measures, but the information is not relied to how the part is positioned inside the machine; furthermore, the different environmental conditions could also affect the result of machining too.
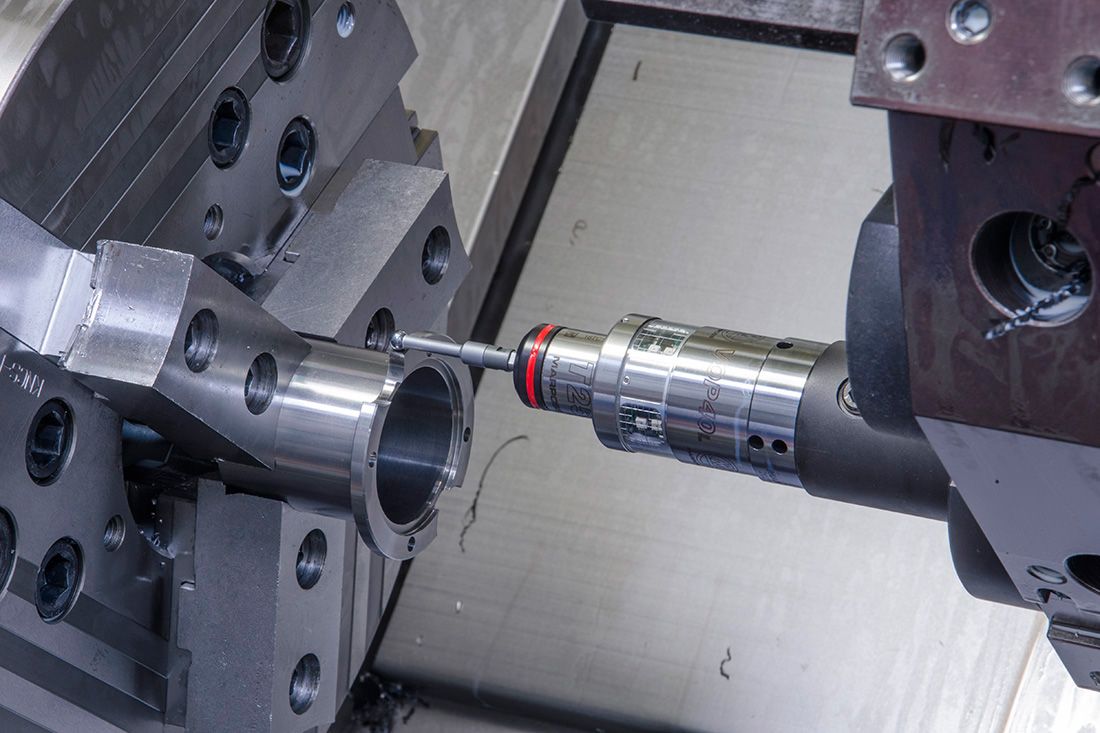
Part probing applications perform two checks: work-piece set up and part inspection.
Before starting a cutting process, it is important to know exactly the position of the rough work piece, its origins and orientation. The lack of such information or its inaccuracy implies the risk of machining the part out of the required tolerances, due to part misalignment. In other words, knowing the work-piece set up leads to significant scrap reduction.
The part inspection allows the dimensional check just after the machining. In this way, the user knows if:
- The part is in tolerance and can proceed to the next process
- The part has dimensions lower than the requested part print, so it requires further machining
- The part was badly machined and out of tolerance. The immediate removal of a bad part prevents further process on it
- Tool wear adjustments are possible to get the next machined part into the tolerance specifications
- Reduction of working and check times
- Increase of production efficiency
- Real-time determination of part position
- Scrap reduction
- Measurement of workpieces fixed on the machine
Marposs provides a complete offer of part probing applications to equip every lathe and turning center and measure parts of different shape.
- Optical transmission touch probes: probes ideal for machines of small and medium dimensions
- Radio transmission touch probes: probes for large lathes and turning centers, working on big parts
- Scanning probe: probe which allows to verify the accuracy of profile just machined and identify surface defects directly on the machine
In addition, Marposs develops dedicated measurement software for every part probing application.