Software for Dimensional Control, Process Monitoring and Grinding Wheel Balancing
SOFTWARE FOR APPLICATIONS ON GRINDERS
MARPOSS, with over 60 years of experience in the production of equipment used to control grinding processes, has always designed equipment with the most suitable technology available for the industrial market at the time. Over the years the production has shifted from solutions that were initially based on a limited amount of electrical and electronic components, to integrated circuits and finally to systems where the software has played an increasingly important role. Since the end of the nineties the equipment produced guarantees greater flexibility and applicative modularity, thanks to the software, by using configurations that are very similar to each other in terms of hardware with a just a few specific parts dedicated to the management of the different sensors and transducers required to control the process.
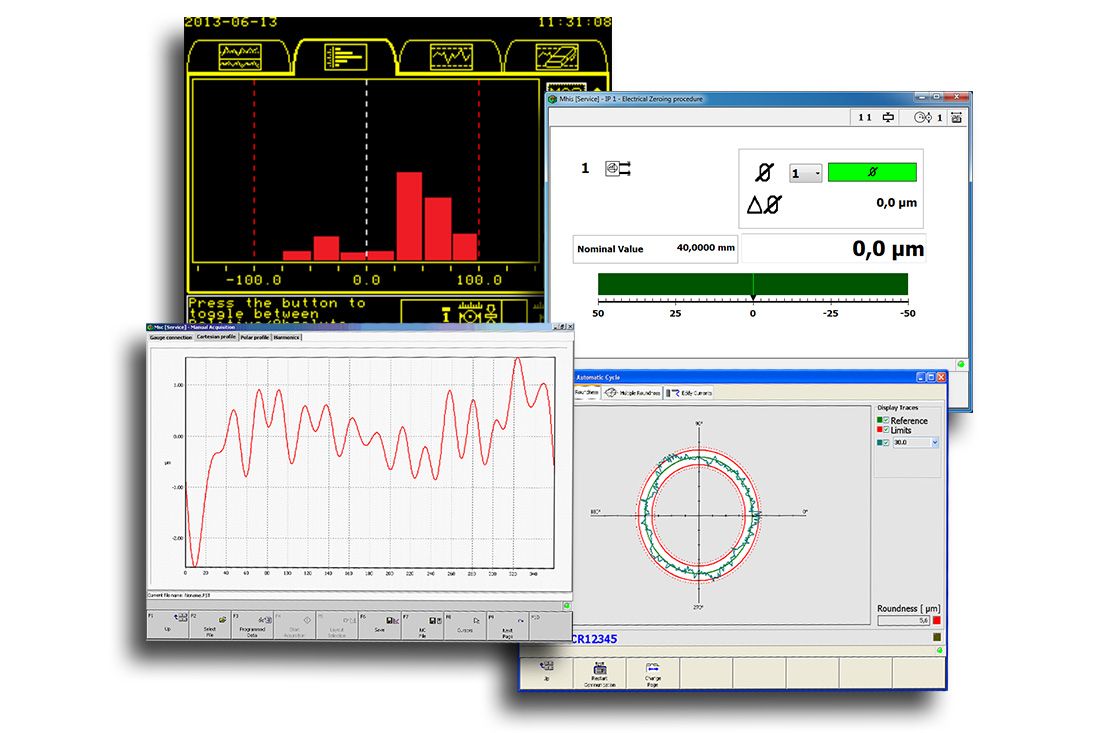
Software application packages have been developed for all types of process controls and various types of cycles, for the specific applications of in-process / post-process measurements, grinding wheel balancing cycles and acoustic sensors.
Today we can design, and this will be increasingly possible in the future, control systems that can be configured very quickly based on the specifications of the individual machine, that can be updated and monitored remotely and that allow an increasingly broad and speedy sharing of data with other systems in the automation and control of production processes.
Marposs is able to achieve products based on compact hardware configurations in compliance with the demands of the main global manufacturers of grinders.
All the control cycles are the result of experiences garnered over the years and they provide operators with increasingly simple and optimised interfaces.
They are accessed through interactive menus that describe the variables to parametrise in simple workshop terms.
All the information necessary to comply with the specifications of Industria 4.0 is exchanged through the latest interfaces.
The main control cycles of the various software libraries are:
- For the measurement: In-process and post-process cycles to check the diameter and length of parts with continuous or interrupted surfaces, part positioning cycles, cycles for specific parts such as camshafts, crank shafts, eccentric shafts and cycles for different types of grinding operations: centerless, double disk, for planes, for pads.
Cycles are available for the production of coupling parts (match grinding), combined cycles to check the conicity or that monitor the shape of the part, processing the ovality or eccentricity.
There are cycles to continuously monitor the quantity of material removed by the grinding wheel and that provide the adequate feedback information to the machine. - For balancing the grinding wheel: cycles for pre-balancing grinding wheels, automatic balancing cycles with one or two balancing heads and machine vibrational mapping cycles
- For acoustic sensors: gap and crash cycles for the optimisation of the cycles times and for the machine safety, monitoring cycles of the noise threshold to keep under control the dressing of the grinding wheel, grinding wheel / dresser touch check cycles, broad band analysis cycles to check the noise levels of the various machine parts (preventive maintenance).
The user interface designed by Marposs is based on state of the art representation methods that, in fact, use the same development environments used to create interfaces for the consumer marker. This ensures that users interacting with the equipment find the same performance of other devices available on the market (touch screens, organisation of the various software levels, similar graphic objects, etc.).
All the software packages can be configured based on the structure of the equipment used, the customer's requests and the necessary communication methods.
Marposs produces equipment that can be divided based on the hardware/software configurations: there is "single function equipment" that manages a single type of control and allows a minimum level of customisation and external interface; and systems with maximum expansion possibilities "multi-function/multi-task equipment", that can execute various types of controls, with more complex cycles and a greater exchange of information externally. The graphic options have various levels, from simple state or numerical or bar indications to time diagrams, histograms and drawings.
BROCHURES AND MANUALS
User Manual | |
---|---|
English |
Common Parts: (3.86MB)
Wheel Balancing: (4.14MB) ACOUSTIC EMISSION: (2.61MB) In Process: (7.61MB) Post Process: (5.63MB) PROTOMAR: (4.47MB) |
Italian |
ACOUSTIC EMISSION: (2.72MB)
Common Parts: (3.84MB) Wheel Balancing: (3.99MB) PROTOMAR: (4.45MB) In Process: (7.78MB) Post Process: (5.50MB) |
German |
Common Parts: (3.55MB)
Wheel Balancing: (4.02MB) ACOUSTIC EMISSION: (2.76MB) In Process: (7.71MB) Post Process: (5.71MB) PROTOMAR: (4.54MB) |
French |
Common Parts: (3.86MB)
Wheel Balancing: (4.12MB) ACOUSTIC EMISSION: (2.75MB) In Process: (7.65MB) Post Process: (5.55MB) PROTOMAR: (4.45MB) |
Spanish |
Common Parts: (3.92MB)
Wheel Balancing: (4.02MB) ACOUSTIC EMISSION: (2.80MB) In Process: (7.61MB) Post Process: (5.52MB) PROTOMAR: (4.49MB) |