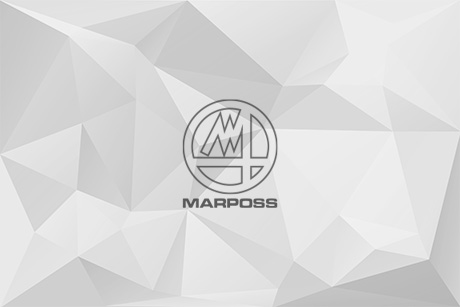
The basic characteristic of the modern universal grinding machines is their flexibility in performing combined external, face and internal grinding operations by means of various spindle wheelhead concepts and machining methods enable precise matching to the required application.
A complete offer for today's market trends towards production systems that allow to execute various grinding operations on the same machine and that can be reconfigured along the time: the machines can be used for plunge grinding, traverse grinding, shoulder grinding, continuos path controlled taper grinding, non-round grinding and contour grinding in one set-up, obtaining an enormous flexibility in changing machine configuration.
This main feature is obtained with different wheelhead executions which enable the use of more grinding tools in various combinations.
Two, three or even four wheels (conventional or high speed CBN type on suitable spindles with integrated motors) can be mounted at the same time and used in sequence for the required machining.
With over 50 years of experiences together with grinding machines makers, Marposs is able to offer an effective constant checking and monitoring of the working process to reach high demand for dimensional and geometric precision. The range of applications includes gap, dressing wheel supervision, collision check, automatic survey of vibrations for wheel balancing and finally the real dimensional inspection before, during and after the working process, with automatic correction of part measure.
All these applications are available in a unique multifunction electronic system: Marposs P7 that, by means of modular hardware and software architectures, is capable to cover all the necessary functions to manage the grinder's control and monitoring cycles.
Marposs P7 capability has been today improved adding new functions able to satisfy the actual market trend for enormous flexibility in changing machine configuration.
More sophisticated software functions are now available for automatic wheel balancing, when the grinding machine is equipped with two wheels on a single spindle shaft (Dual Plane Balancing), and for CBN wheels dressing monitoring to detect a chip or other discontinuity in a wheel's surface using acoustic emission sensors technology (AE Monitoring with Dynamic Thresholds).