Tracer Gas Leak Test
Within Marposs Group, Helium Technology S.r.l. designs and manufactures helium leak testing machines dedicated to meet the different needs of our customers, from a simple manual station to automatic systems integrated into production lines.
WHY?
To answer to the growing requests of leak testing using helium as tracing gas in strategic industrial sectors where the quality requirements are getting more and more strict.
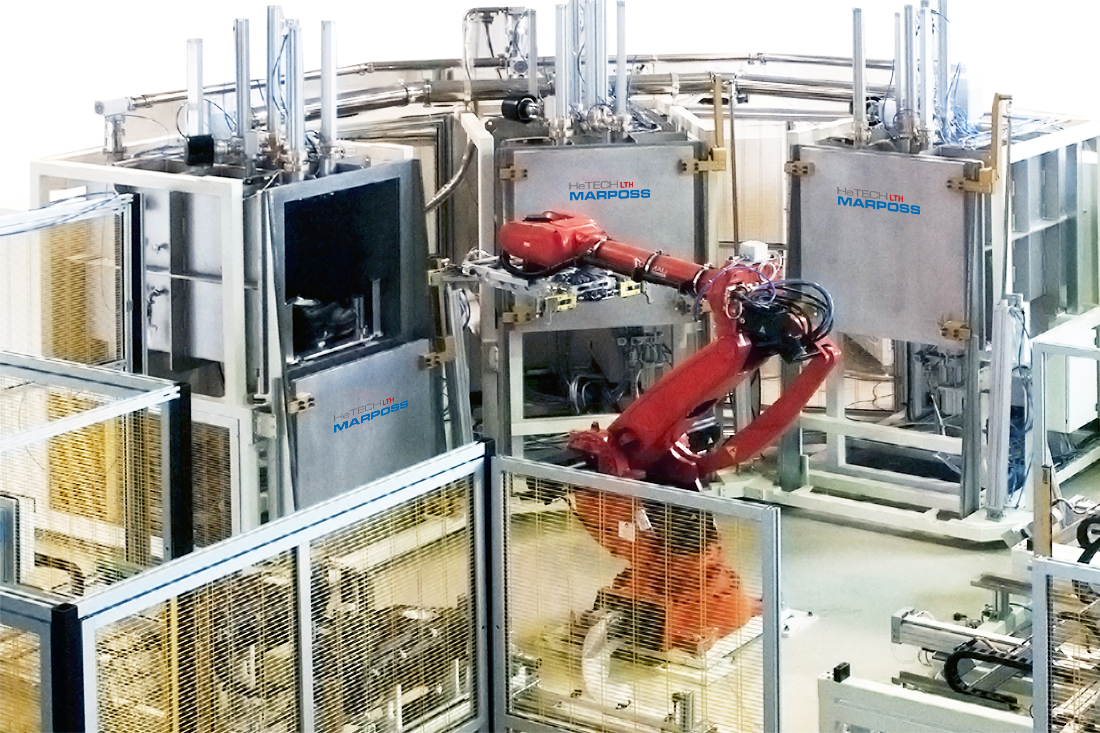
- Totally customizable benches
- Different sectors of application (Automotive, Aerospace, Refrigeration, Food Industry, Medical, White goods and others)
- Accuracy and reliability of the test compared to other tracer gases methods
- Interchangeable tooling for different products to be tested on the same machine
- Global presence and financial soundness guaranteed by Marposs network worldwide
- Strong expertise and Tailor-made approach for each project
- Relevant reference in the market worldwide, mainly working with multinational customers
- Collateral services related to our commercial proposal:
- On site leak testing
- After-sales and technical support assistance
- Periodical assistance and maintenance programs
- Revamping systems
- Manufacturing of Helium Recovery Systems of different capacity depending on customer request
There are different methods for conducting a helium leak test:
Global test on vacuum chamber
This represents the best and most effective choice:
- Highest sensitivity, accuracy and reliability
- It’s a global test: the leak will be detected anyway, everywhere it is
- It’s an automatic and objective test: results are not affected by human error
- It’s completely accepted by any norm
- Result does not depend on factors as the temperature of the test object (if it’s warm, it’s better), the volume within reasonable limits, the shape and the material of the test object (also flexible objects can be tested).
- The only condition for applying this test is that the component to be tested doesn’t suffer to stay in vacuum conditions and the material is not permeable to the helium.
Sniffer test
It’s the most simple and cheap helium test, widely used everywhere. Main differences respect to the test under vacuum chamber are:
- Worse sensitivity (also because, typically, the sniffer probe cannot catch the entireleakrate,butonlyafraction).
- It can be used to test only few specific points of the test object as it’s not a global test.
- Might be a good option for testing huge components (volume higher than 3m3), too big to be placed in a vacuum chamber.
- Accuracy greatly depends on the attention the operator pays to the job
- The sensitivity is lower as Sniffertestisdoneinambientconditions. Hencethebackgroundisaffectedby thepresenceoftheheliumnaturallypresentintheair(5ppm). Inside the chamber, given the air it’s been evacuated, the background is much lower.
Spray test
In this case the mass-‐spectrometer is connected to the test object, and helium sprayed from the outside. It’s used very rarely, mainly to localize the leaks only. There’s not much to say about this method.
Global test helium outside / vacuum inside
In this case the component is tested within a close chamber in which there is an atmosphere enriched with helium. Mass-‐spectrometer is connected to the component, eventually joined to a vacuum pump if the component’s volume is too large.
Sometimes is requested by the customers because of the cheaper price, but it’s not likely to be used for one main reason: the differential pressure between outside and inside can be only one bar, and it’s applied in the opposite direction than the in the normal working conditions of the test object.
So, it is correct to apply this technique only in one case: when the test object will work in vacuum conditions under atmospheric pressure.
- Dedicated pumping system for the analysis - Total flow
- Pumping system placed on a cart for easy maintenance
- Dedicated Electric and Pneumatic cabinet
- Ventilation and Sound proofing of the pumping system
- Removable & Exchangeable tooling with manual or automatic loading/unloading
- Totally customizable HMI interface