Monitoring of the Machine Tools for Semiconductor Manufacturing
In ensuring the reach of productivity levels, it is crucial to maintain the availability of production equipment through maintenance activities. Using Machine Monitoring products, the status condition of machine elements, based on the positions of installed sensors, gives the possibility to track the ongoing health status. Maintenance activities should begin only when there is a warning caused by a machine element failing.
During collision events, the damage is not caused by the immediate collision since Machine Protection products detect this initial point and stop the progression of movement, saving breakages and unplanned downtime.
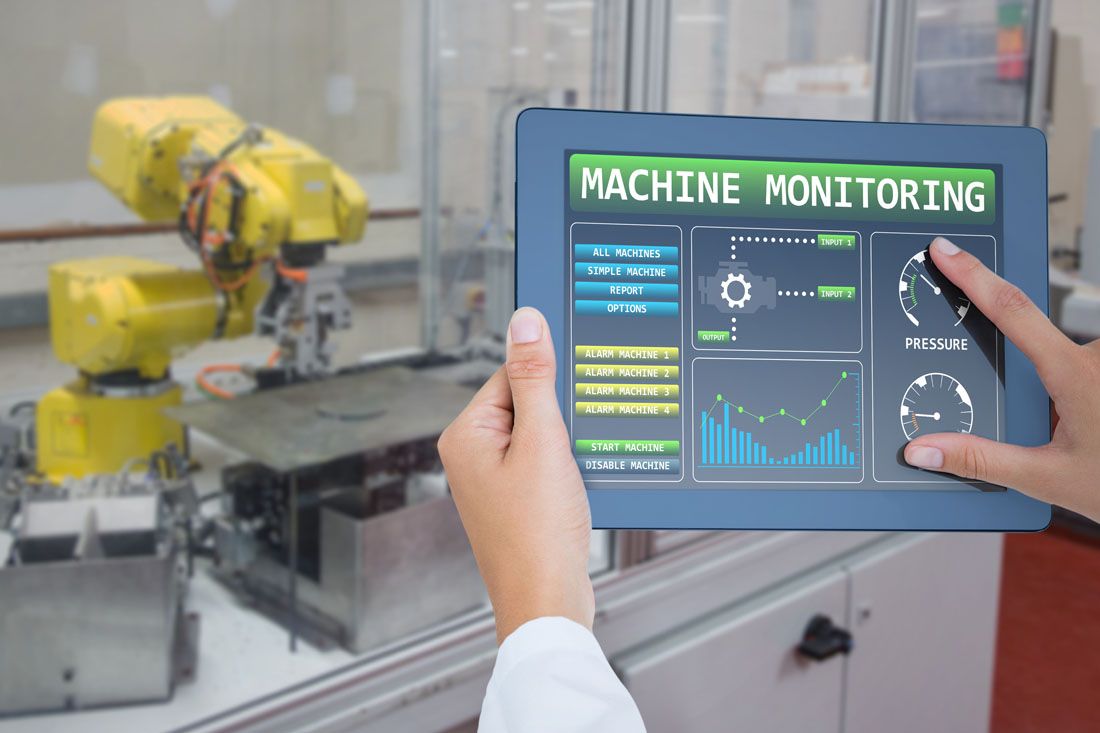
Marposs sensors can detect diamond wire breakage on ingot slicing machines, monitor wheel dressing on grinding machines, or check vibrations during lapping operations. Marposs systems take the task of analyzing, safeguarding, and optimizing production processes.
In addition, the early detection of bearing damage is essential to keep machine and spindle vibrations under control, reduce consequential costs and improve quality. This can be achieved through the precise evaluation of sensor signals (vibration, temperature, and optional gravity). Alarm limits can be set individually, and if exceedor dropbelow these limits, a defined reaction can be taken promptly.
- Artis machine monitoring systems reliably detect vibration anomalies
- Vibration sensors measure bearing conditions of spindle and axis
- Easy integration into new or existing machine tools, equipment, or robots, regardless of the typre of machine control
- The system can run permanently in the background. Operator intervention is only required in the event of an alarm
- The event recorder (black box) reliably records the alarm events (date, time, and values) and the stored information can be used for further evaluation and analysis
- sensor data and event data can be exported as CSV file
- Reduction of unplanned outage times and costs because worn components can be replaced at an early stage (predictive maintenance)