Acoustic Emission Sensors for Grinders
ACOUSTIC SENSORS
The acoustic sensors are one of the components of the monitoring system on grinding machines. They check the noise issued at the point where the part or dresser touch the grinding wheel.
The wide range of acoustic sensors can be applied to grinding machines for internal or external grinding, grinding without centres, grinding for planes, grinding for gears or tools, resolving the most disparate application problems.
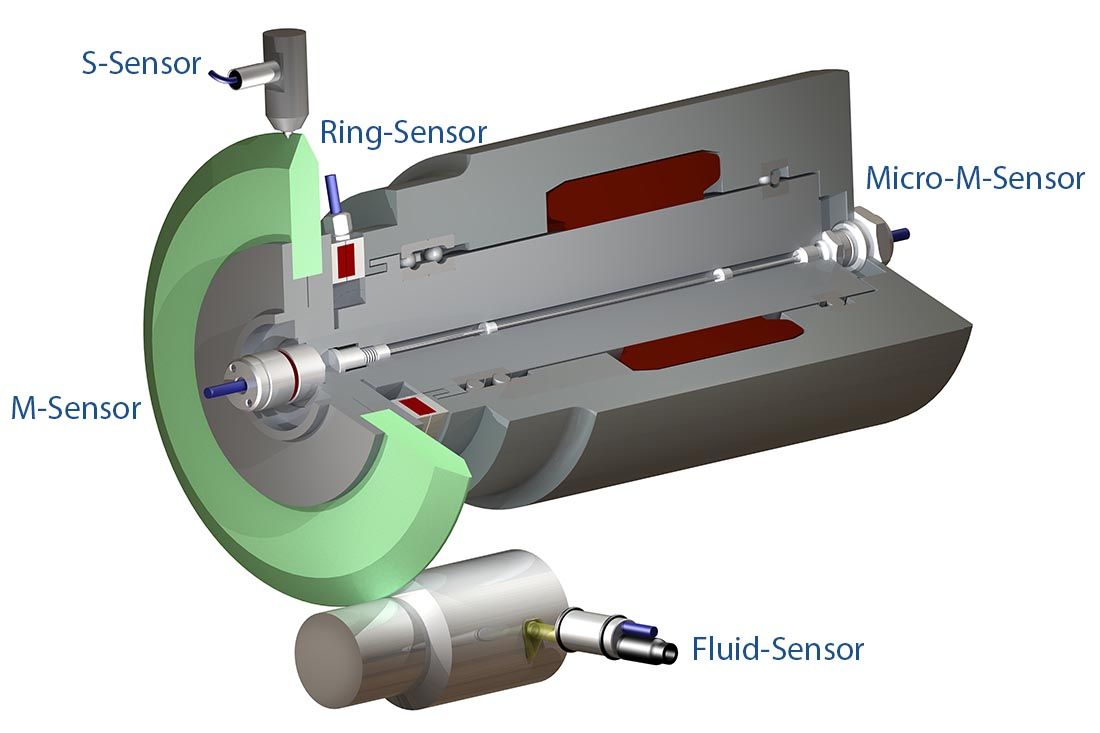
The monitoring systems based on acoustic technology, monitor the noise emitted when the grinding wheel touches the part or the dresser. The noise is generated during the cutting action and is transmitted through the grinding as ultrasound waves. As these waves pass through the various machine components, the frequency and amplitude change. By monitoring these waves any changes during the machining can be checked and therefore corrective actions can be implemented on the machine. The effectiveness of the sensors is dictated by their positioning, as close as possible to the machining area.
Monitoring with acoustic sensors is used to determine the contact between the grinding wheel and the part or the dresser, reducing the air gap time. The changes in the acoustic emissions can indicate changes in the force due to the cutting conditions of the grinding wheel and allow the cycle to be adapted, thus optimising the production process.
There are two series of acoustic sensors:
- Fixed acoustic sensors: the sensors consist of a single piece and the signal can be transmitted in air or through a liquid. Different dimensions are available to meet every application requirement.
- Contactless acoustic sensors: the sensors consist of a fixed part (stator) and a rotary part (rotor), but have different shapes and dimensions to meet every application requirement. The signal is transmitted without a direct contact between the rotor and stator.
The sensors can be connected to the following systems:
- Production process monitoring
- Air gap check and reduction of the cycle times
- Collision check and reduction of the risk of serious damages to the grinding wheel and the machine
- Reduction of the maintenance costs and overall costs
- Longer life of the machine parts
- Frequency response: up to 1000 KHz
- Rotation speed: up to 120,000 RPM
There are different versions of acoustic sensors available to allow the positioning as close as possible to the machining area, where there is the best signal/noise ratio.
Fixed acoustic sensor: ultrasonic acoustic emissions sensor with surface propagation and signal transmission via cable. The sensor is positioned on the part or on the push rod dresser.
Fluid acoustic sensor: ultrasonic acoustic emissions sensor with surface propagation and signal transmission via cable. The signal is transmitted from the part or the part support or the tool through the machine lubricant/coolant.
Rotary acoustic sensor: ultrasonic acoustic emission sensor with contactless signal transmission. The sensor is positioned on the spindle, on the grinding wheel support flange or on the dresser disk.
Internal spindle acoustic sensor: ultrasonic acoustic emission sensor with contactless signal transmission. The rotary part is split and consists of the piezoelectric sensor and the electronic signal transmission part. The dimensions of the sensor can be adapted to specific application requirements. The sensor is positioned on the grinding wheel or dresser spindle.
Ring acoustic sensor: ultrasonic acoustic emission sensor with contactless signal transmission. The fixed and rotary part have a ring shape and are available in various dimensions and shapes so that they can be installed externally on different models of grinding machines. The sensor is positioned on the flange of the grinding wheel, on the spindle or on the part support head.