멤브레인 측정과 검사
연료 전지 및 전해조의 핵심 부품 생산시, 주요 항목의 치수가 정밀해야 하며, 정확한 기능이나 효율을 저하시킬 수 있는 결함의 존재 유무 검사가 매우 중요합니다.
멤브레인, CCM(Catalyst Coating Membrane), MEA(Membrane Electrode Assembly), GDL(Gas Diffusion Layer), 플로우 플레이트 및 BPP(Bi-Polar Plates)와 같은 부품의 제조 공정은 스크래치, 찢김, 리플, 불순물, 오염물 등을 발생될 수 있으며, 이는 크기에 따라 특히 위험을 발생할 수 있습니다.
제품 개발 단계에서 분석과 생산 라인의 샘플링 검사를 위해 마르포스는 대형 평면 부품의 품질 관리용 반자동 측정 스테이션을 제공합니다. 이 시스템은 정밀한 치수 측정과 다양한 유형의 결함을 감지하기 위한 완벽한 검사를 수행하도록 설계되었습니다.
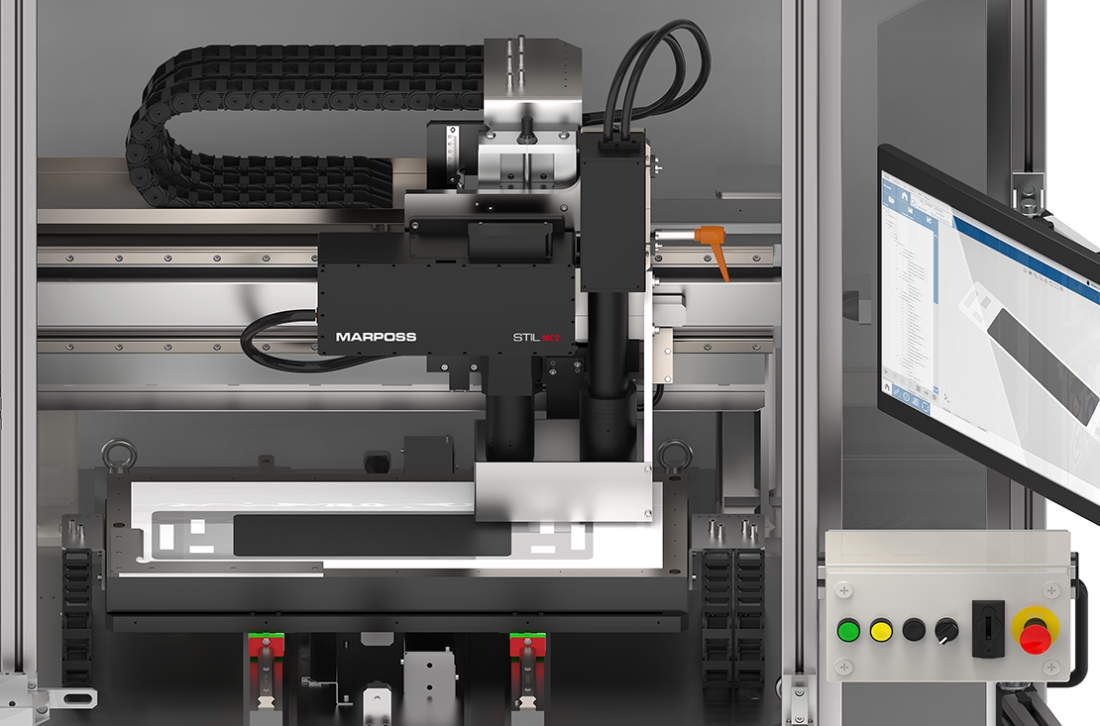
측정 스테이션에는 마르포스 STIL사의 다양한종류의 공초점 프로브 제품을 사용하며, 이 프로브는 측정과 스트로크 리툴링을 자동으로 수행하는 장비 제어축에 장착이 됩니다.
MC2 공초점 리니어 카메라는, 기존 광학 제품에 적용된 고해상도 카메라에서는 가능하지 못했던 최대 2.6mm의 심도에서 완벽하게 초점을 맞춘 초고해상도 이미지 획득이 가능합니다.샘플링 주파수가 매우 높기 때문에 짧은 시간에 표면을 스캔하여 다양한 유형의 결함을 감지할 수 있습니다.
기계 축에 MPLS 공초점 라인 센서를 장착하면 피측정물 전체의 x-y-z 치수와 감지된 잠재적 결함을 평가할 수 있습니다. 이러한 결함들의 치수 특성을 통해 피 측정 소재의 기능상 실제로 위험을 초래할 수 있는 결함을 판단할 수 있으므로 적절한 조치를 취할 수 있습니다.
피측정물의 유형과 요구되는 제어 사양에 따라 레이저 프로필러미터, 공초점 또는 간섭계 포인트 센서, 리니어 또는 매트릭스 카메라와 같은 기술 기반의 다양한 센서를 통합할 수 있습니다.
예를 들어, 피드 채널의 깊이와 폭에 대한 정확한 스캐닝 및 측정을 위하여 공초점 포인트 센서를 플로우 플레이트 및 BPP의 제어에 사용할 수 있습니다.
- 다양한 평면 부품 측정 및 검사를 위한 유연한 솔루션
- 측정시 소재의 손상 위험 없이 정확하고 신속한 포지셔닝을 위한 진공 시스템이 탑재된 기준 베이스
- 비접촉 측정 및 검사 기술
- 발생 가능한 모든 결함의 특성을 총체적으로 정의할 수 있는 완전한 검사.
- 검사할 소재 형태에 따라서, 인공지능으로 결함을 인식하는 AI 알고리즘의 커스터마이징 가능.
- 결함이 있는 영역에서만 치수 측정을 실행하는 컨트롤 싸이클 프로그래밍.
게이지 전체 치수 (WxDxH) | 2,0 m x 1,5 m x 2,2 m |
피측정 소재 최대 크기 (x-y) | 600 mm x 200 mm |
Z축 최대 측정 범위 | 2,6 mm (with MPLS DeepView) |
Z축 최대 이동 범위 | 50 mm (to measure parts of different height) |
스캐닝 속도 | Up to 200 mm/sec 요구 사양에 따름 |
Further technical data (measurement resolution in X, Y and z, accuracy, repeatability, cycle time, …) will depend on the Xed versions for MC2 and MPLS sensors.