TTV - Total Thermal Vision: infrared vision technology by Marposs
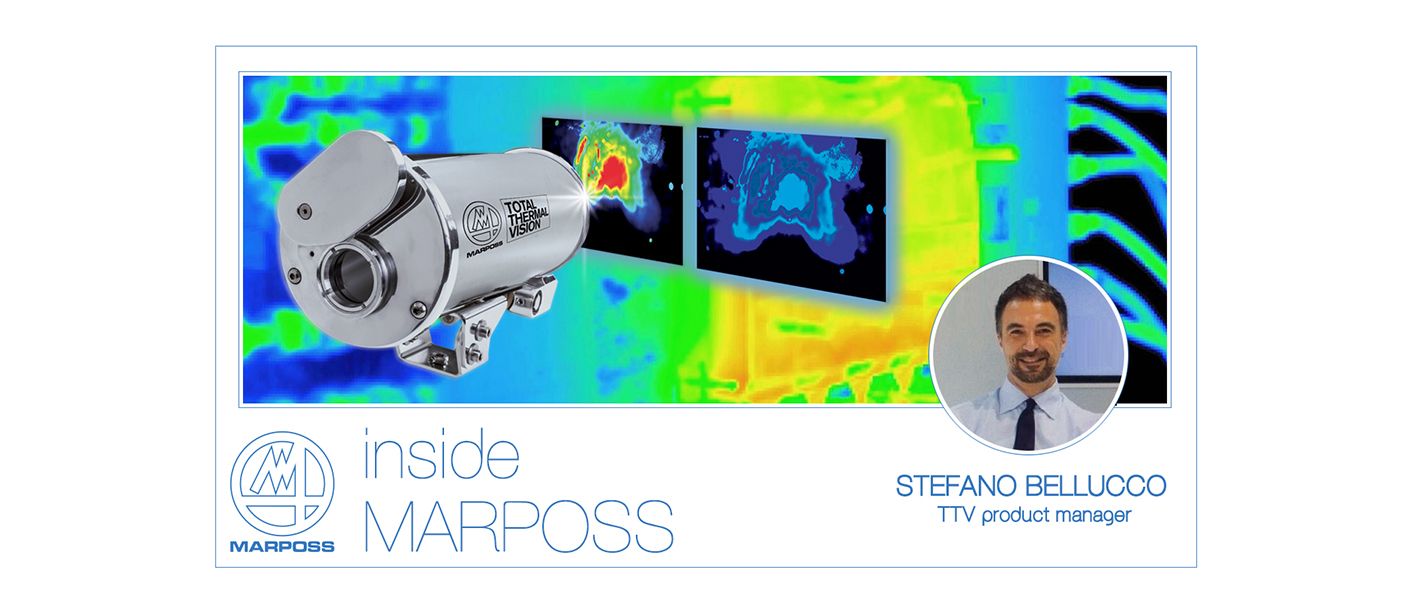
The innovative system for monitoring the surface temperature of moulds during die-casting.
How many tons of molten aluminium are wasted by foundries in warm up phases? How many defects can an incorrect distribution of the temperature on the mould surface generate?
Marposs TTV has been specifically designed to provide an effective solution to this kind of problem. Our new infrared vision technology allows the start-up phase to be optimised with the following benefits: increased mould lifespan, initial rejects reduced by up to 70% and cycle time optimised.
The result? Major savings obtained in just one year thanks to thousands of standard approved casts and increased press efficiency.
Temperature distribution on the surface of the mould is the key factor for maintaining an efficient process with high quality levels.
Shrinking during hardening, porosity, cracks and bubbles: many cast defects are caused by out-of-control temperatures or non-optimised distribution. To create aluminium casts, even large ones, like the engine blocks or crankcase (parts that can weigh up to 10/12 kilos), the average cycle varies between 20 and 90 seconds. In such a short time temperature distribution is fundamental to ensure that parts solidify with no defects.
Marposs TTV captures the temperature distribution on the surface of the mould in a single thermographic image, giving a complete overview of information that other technologies cannot. Pyrometers or thermocouples, for example, can only measure temperatures in one specific point at a time.
Total Thermal Vision offers you the chance to monitor and ensure temperatures are correct without affecting the cycle time. This optimises both the process and the final quality of the casting.
This system, originally designed for high-pressure die-casting is now also available for low pressure and gravity casting. It has repeatability features that allow you to check temperature distribution across the entire mould surface and the stability of the whole process.
Total Thermal Vision is supplied with two high definition Infrared Camera Units connected to the Controller. They are installed on the mould plates: one on the fixed half, which is part of the machine structure; the other on the movable half, that opens at every cycle to enable the casting to be extracted and to let the sprayer start the lubrication phase.
TTV is the only thermographic system with High Definition Infrared cameras supplied as standard. These present the temperature distribution with extreme accuracy, through Regions of Interest (RoI) designed to monitor the most important and critical cast details.
If the TTV detects that the temperature is within the defined range, the cast is considered good and the cycle proceeds. On the other hand, any temperature distribution outside the range is flagged and zones with temperatures that are higher or lower are indicated.
Why choose Marposs TTV?
Marposs TTV reduces the investment payback period of the whole die casting cell.
In traditional systems, a die cast is considered good or defective only after being created and the process has an initial average scrap rate of between 5 and 20: this is a fixed initial cost before reaching operating range and production with no defects.
Therefore TTV drastically reduces costs due to rejects and inefficiency .
Marposs TTV optimises die casting cell performance and efficiency.
Thanks to surface temperature monitoring throughout the entire process, TTV highlights critical aspects that allow corrective actions to be taken and avoid the most common defects.
Marposs TTV reduces thermal stress of the mould.
The process moves from high to low temperatures, rapidly and continuously (every 30/40 seconds per mould, typically for 100,000/300,000 pieces).
Using TTV decreases the thermal stress of the mould, minimizing differential mould expansion, contraction and consequential cracks and breakages.
Marposs TTV does not affect cycle time.
No process changes are required when TTV monitoring system is installed. The cycle time is not extended and there are no machine stops.
TTV allows cycle time improvements: as the temperature distribution is known beforehand, lubrication and air blowing can be optimised and reduced.
Marposs TTV is intuitive and user-friendly.
Monitoring operations can be conducted immediately without any in-depth process knowledge being required. The Operator is provided with a touch screen interface, where all the useful data to monitor the process are displayed at a glance.
The screen provides four images - two for each Infrared Camera - with the visual temperature alarms covering up to ten Regions of Interest (RoI) .
TTV is Marposs.
Thanks to its experience in process monitoring, acquired from both machine tools and part manufacturing processes, Marposs has all the know-how required to extend this system from high pressure die casting to other light alloy casting technologies.
Last but not least, the Company can support customers throughout the entire production chain by providing a complete solution for all the various processes.