MAINDO: Empowering Quality Management and Process Optimization in Manufacturing
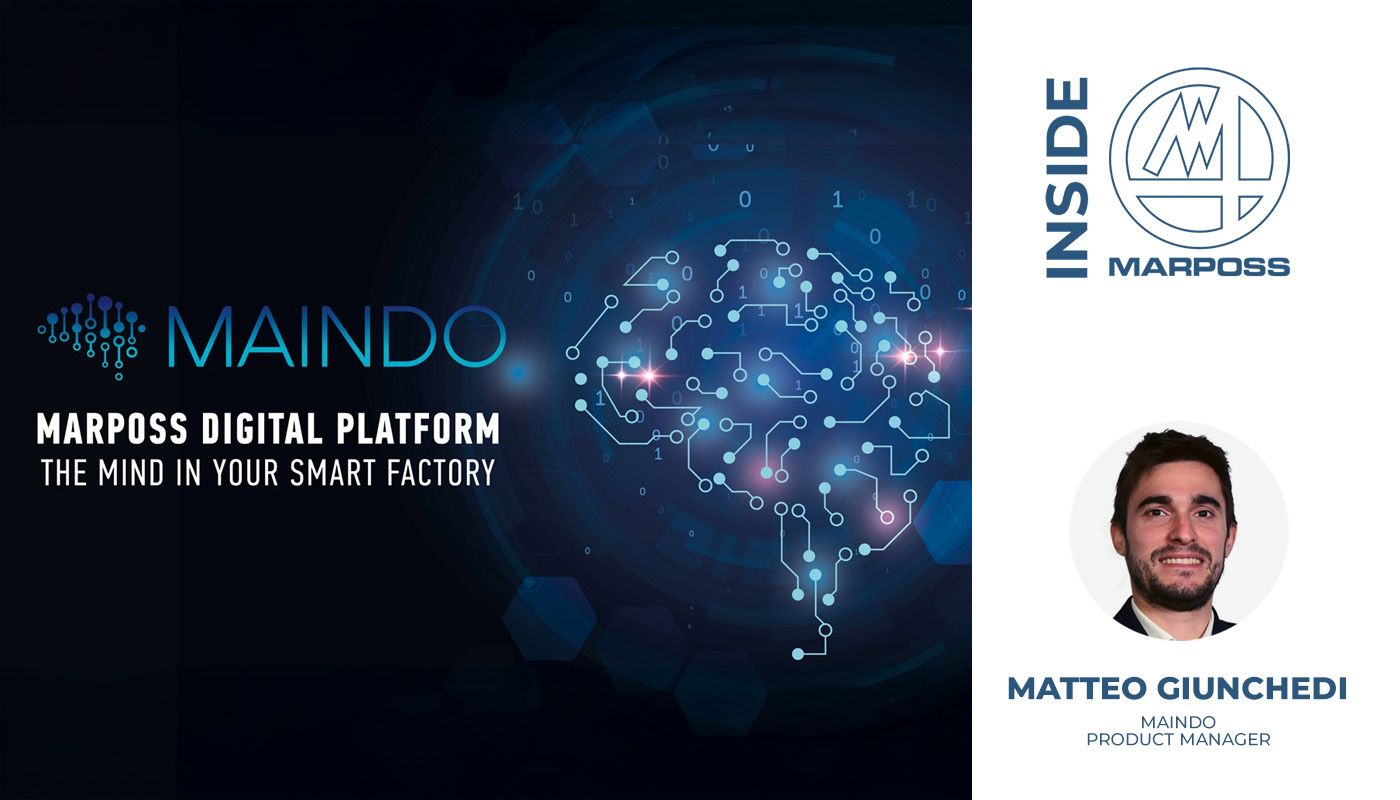
In today’s competitive manufacturing environment, managing quality data and ensuring compliance are critical for staying ahead. The task of securely connecting shop floor systems to cloud-based solutions and handling data from multiple devices can be daunting. Disparate systems, manual data entry, and potential security breaches lead to inefficiencies and costly errors. MAINDO addresses these challenges with a centralized, secure platform for data management, traceability, and quality assurance.
Introducing MAINDO: A Secure, Web-Based Platform with Seamless Integration and Flexibility
MAINDO is a comprehensive solution for streamlined quality management through data centralization and real-time monitoring. Designed for flexibility, MAINDO is cloud-based but also offers an on-premise option for those with specific IT infrastructure needs. This adaptability enables manufacturers of any scale to integrate MAINDO with existing MES and ERP systems seamlessly.
Accessible from any device via a web-based interface, MAINDO allows quality managers, operators, and executives to monitor and manage data from anywhere. MAINDO’s security is enhanced by the MAINDO Edge device, a hardware-software solution installed on-site that acts as a secure gateway between production stations and the central server or cloud. By managing data traffic locally, MAINDO Edge minimizes latency and ensures real-time data access for analysis and decision-making.
MAINDO’s Standout Features: Inspection Plans Integration, Instrument Management, and Real-Time Insights
MAINDO’s advanced integration enables it to manage inspection plans and synchronize them across all measuring devices on the shop floor. Any updates to an inspection plan are instantly reflected across connected stations, eliminating manual reconfigurations and significantly reducing the risk of errors.
The platform also simplifies instrument management, covering everything from certification to calibration tracking and maintenance schedules. This data links directly to measuring systems on the shop floor, ensuring that tools are calibrated and ready when needed. The result is a reduction in manual data entry and an increase in precision and reliability in quality assessments.
Unmatched Capabilities for Traceability, Real-Time Monitoring, and Process Optimization
Traceability is a core capability of MAINDO, allowing users to track quality management events across all production stages—from inspection measurements to instrument calibrations and plan updates. With just a few clicks, users can search by batch or serial number, retrieve specific measurements, and generate reports. This instant access to detailed records simplifies compliance processes and enhances accountability across the production floor.
MAINDO’s real-time monitoring keeps quality and production performance in check around the clock. A centralized dashboard displays data from all measuring devices, enabling operators to quickly assess whether production processes meet standards and address deviations early to prevent downtime.
Beyond simply providing data, MAINDO enables manufacturers to analyze it holistically for process optimization. By consolidating production data, MAINDO empowers manufacturers to analyze trends, identify improvement opportunities, and make data-driven decisions that reduce costs and enhance product quality.
Real-World Impact: How MAINDO Transforms Battery Testing
Consider a manufacturer using MAINDO to tackle quality management challenges. With data coming from multiple machines, frequent manual data entry, and no real-time monitoring, this customer needed a way to centralize data, automate processes, and enhance quality control. They needed to ensure that their new production line of battery packs met the highest quality standards while maintaining traceability for all tests performed. Each part produced undergoes testing, with a report generated for each, resulting in over 160,000 measurements daily, all of which require proper storage and traceability.
With MAINDO, they saw immediate improvements across the production floor:
- Central Supervisor: Previously, updating test recipes was a time-consuming manual process. Now, updates are automated with MAINDO, saving time and minimizing errors.
- Real-Time Monitoring: MAINDO’s dashboard provides full visibility of the production line. Operators can view live data from each machine, quickly identifying and resolving issues in real time, which significantly reduces downtime.
- Centralized Data and Traceability: MAINDO centralizes data from all machines, ensuring complete traceability for each part and simplifying audits by making all measurement records easily accessible.
Since implementing MAINDO, this customer has experienced substantial gains: action time has decreased by 20% compared to other production lines, and manual data entry errors have been virtually eliminated. With real-time data readily available, they optimize production processes quarterly, improving efficiency and ensuring full compliance with industry standards.
Experience the Future of Manufacturing Quality Management
Imagine a production environment where quality monitoring, compliance verification, and process optimization are all accessible from a single, secure platform. MAINDO turns this vision into reality, transforming complex data management into a seamless quality control system. With web-based access, flexible deployment options, and the security of the MAINDO Edge device, MAINDO provides manufacturers with a complete solution for managing production quality.