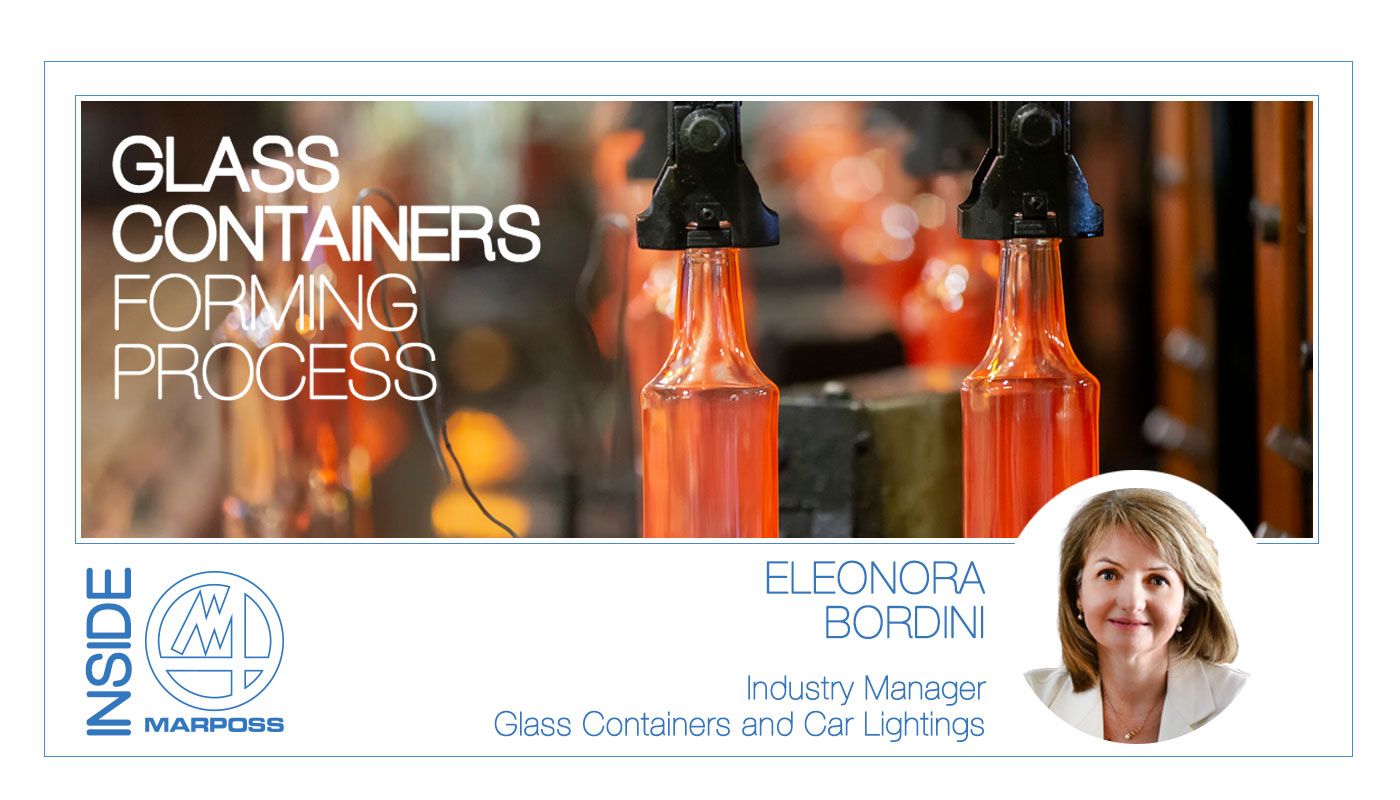
The evolution of glassmaking
Glass is one of the oldest materials. The history of glass dates back to 3500BC. The first hollow glass container was manufactured, by the Egyptians, in 1500 BC.
A technological revolution occurred when the blowpipe was invented, in the first century BC. Anyway, the real revolution came with the first automatic bottle blowing machine, invented in the USA by Michael Owens, at the beginning of the 20th century. It allowed to manufacture up to 2.500 containers/hour, making glass containers production possible on an industrial scale.
The technology was furtherly improved in 1925 with the first IS (Individual Sections) machine using the blow & blow or press & blow techniques, which are still applied today. Every section produces one or more containers independently. A gob of melted glass falls in a blank mould where, based on the technique, it is pre-blown or pressed with a plunger. The pre-shaped gob (parison) is delivered into a finish mould where blowing is completed.
Nowadays forming machines can have up to 20 individual sections, each one producing 1 to 4 containers simultaneously. This means that 1 to 4 gobs (SG=single gob, DG=dual gob, TG triple gob, GD=quad gob) of melted glass fall in 1 to 4 moulds present in each section. And this happens in parallel in each section. Depending on the container’s size and shape, the production speed can be as fast as 700 containers/min.
Glass containers: properties and virtues
Glass containers are used as packaging for different industries:
- food and beverage
- perfumery and cosmetics
- pharmaceutical
Glass is inert: nothing passes from the glass into the product and nothing penetrates from outside through the glass into the product.
Glass is sustainable (100% recyclable).
Glass is beautiful and enhances the perceived value and quality of the product, as compared to other packaging materials like plastic and aluminium.
Anyway, with respect to other materials, glass is much heavier. The manufacturing process has been improved, in the last years, to obtain lightweight containers. Glass containers are now up to 40% lighter with respect to 20 years ago. Weight reduction is a necessity, not only to reduce transportation costs but, above all, to save raw materials and energy.
Significant technology improvements have been done on melting furnaces as well, to reduce energy consumption and CO2 emissions.
Glass containers have become more and more complex in shape. Unique shapes increase the product value (premiumization) and brand awareness. Let’s think, for example, how easy it is to recognize a Coca Cola bottle or a Nutella jar, even though the container is empty and without the label.
Glassmaking trends: improve quality control
Glass containers manufacturers are more and more concentrated also on the quality of their production, with the goal to reduce scrap parts and avoid issues connected to customers’ complaints.
Quality control should be anticipated at the earliest possible stage of the glassmaking process, with the purpose to immediately take the necessary actions.
Inspection for defects detection, on the bottom, body, neck and finish of the containers is carried on the entire production with in-line inspection machines mainly based on contactless technology (cameras and other optical sensors).
Dimensional control is carried out, on a sample basis, near the production line, with go-no-go gauges or, alternatively, with manual gauges or semi-automatic/automatic gauging systems in the QC Lab.
Dimensional controls required on glass containers include:
- total height
- verticality
- mouth parallelism
- external diameters, or long/short sides, and diagonals on the body
- external diameters on the neck
- many different parameters on the finish (e.g. diameters, heights, radiuses, angles…) on any kind of finish
Control with go-no-go gauges presents a whole set of issues: it does not provide any quantitative information and it relies on the operator’s skills. Moreover, it implies high costs since a set of dedicated go-no-go gauges is required for each article produced and these hard gauges have to be managed and periodically re-calibrated. Furthermore, from this method, it is not possible to collect any data and perform statistical analysis to improve the process.
Semiautomatic gauging systems can be based on contact or optical technology. The container to be measured is manually loaded/unloaded and the measuring cycle is carried out automatically. Systems based on optical technology are flexible and can measure many different articles regardless of their size, shape and colour without any job change.
In automatic gauging systems the container handling, as well as measurements, are carried out fully automatically, without any human intervention. They are mainly based on contactless technology and, in addition to external dimensions, they can also measure other features like mouth inside diameter and profile, wall thickness, weight, push-up, labelling area profile.
The advantage of automatic gauging systems, over semi-automatic ones, is to dramatically reduce manpower costs.
The results of the measurements performed with semi-automatic and automatic gauging systems are sent to a MES (Manufacturing Execution Software) and are used by decision-makers to fine-tune and monitor the manufacturing process in real-time.
Other controls and tests carried out on glass containers on a sample basis in the QC Lab include:
- impact test
- vertical load
- internal pressure test
- internal volume measurement
- residual stress
Learn more about Marposs' complete range of solutions for glass containers measurement