Tool Setting and Geometric Checking on Wood Working Machines
Those who work with wood-working machines, understand very well, the problem of scrap parts that are caused by broken, worn, or incorrectly measured tools. It is quite common, that end users are not provided with instruments that can detect the real tool dimensions during working cycles; which is fundamental information for the proper execution of production.
Tool Setting grants one the ability to automatically acquire the exact values of length and diameter of cutters or drills; this can be done before, during, and after the machining process. Tool Setters measure tools inside the machines' working areas thus, in real machining conditions. In this regard, tool check becomes more meaningful and faster than pre-setting outside the machine.
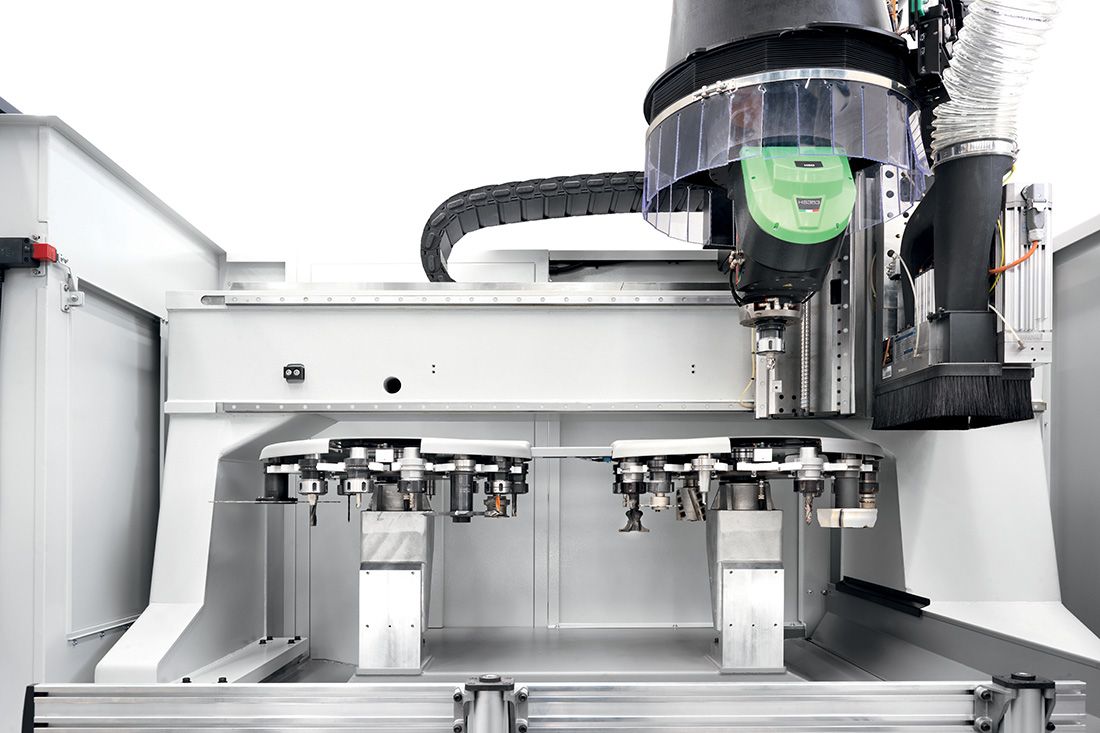
Tool setters enable two fundamental measurement phases: presetting and tool verification.
Thanks to the presetting phase, tools are measured on the machine before starting the machining process. This is done so that that axis movements are done with respect to their real dimensions and not theoretical ones. Furthermore, it is possible to detect and compensate run-out errors, due to wrong clamping of tools on the spindle.
Tool verification grants the ability to have an intermediate check between processes to detect wear or breakage on cutters and drills in order to keep cutting quality under control. Moreover, it compensates thermal drift, which can influence the tool length.
- Increase of production quality
- Constant level of production quality
- Time-saving in comparison with external or manual tool check
- Increase of machine productivity
- More accurate measurements, as they are performed in the real working conditions
- Possibility to check the tools between one working phase and another
- Automatic acquisition of measured values and tool table update
- Facilitation of operators’ activities
- Elimination of mistakes due to manual input of measurement values on a CNC
Marposs proposes a wide variety of tool setters, which cover the different application requirements:
- Contact Tool setting, both wireless and wired applications, allowing measures of static or rotating tool, of at least 1 mm diameter. It is possible to realize presetting operations to obtain diameter and length values along with integrity checks
- Non-contact Tool Setting, in case you want to measure tools smaller than 1 mm or more, complex measurements are necessary (e.g. run out, integrity check of cutter profiles)
Marposs also develops measurement software cycles for every tool setter typology.