Technologies -- Digital Scanning
Digital scanning is a measuring technology that can be applied when one or more static inspections are not sufficient enough to fully qualify the dimensional characteristics and shape of the measured component. It is often required for the measurement of mechanical components that must work in the most precise matching conditions. In general, it is a suggested measuring technology for the detection of specific shape errors of the workpiece.
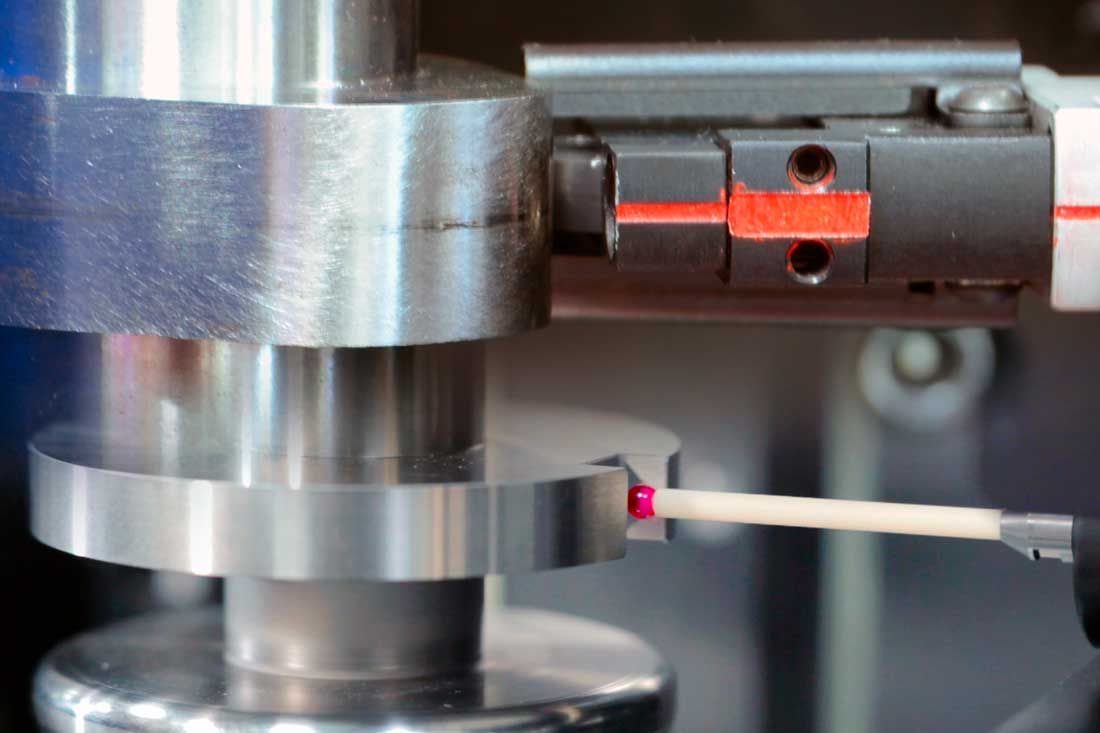
In respect to the static inspection of mechanical parts, digital scanning is able to provide several advantages:
-
Detailed inspection and data collection along the full extension of the scanned surface
-
Evaluation of the functional behavior of the component
-
Information useful for the set-up and control of the machining process
The measuring unit and the measured component are maintained continuously in relative motion, one respect to the other, during the acquisition of the measurement. The result of this operation is a vector of measurement samples which represent the dimensional profile of the component in the scanning direction. This vector, which can be suitably filtered and processed on the basis of various possible methodologies, is then used to elaborate measurements representative of the actual state of the workpiece, relatively to its size and shape tolerance.
The scanning speed and the sampling frequency depend on the accuracy that is requested for the specific measuring application.
Axial scanning of cylindrical components
A common example of digital scanning can be represented by the axial scanning of cylindrical components such as holes and pins.
To ensure the correct functional behavior of components that have to work in particularly precise matching conditions - such as injection bodies, needles, valves, or pumps - it might be necessary to measure the matching diameter, its shape errors, and the axial extension of the matching surface, by a complete scan.
For this purpose, several different measuring devices can be used:
- pneumo-electronics measuring plugs and rings
- contact-electronics measuring units
- optical gauges
- scanning probes
In the case of digital scanning of a hole, the plug is maintained in a constant movement along the axis of the bore during the acquisition of the diameter values. The vector of the acquired samples represents the profile of the diameter, its variations, and the scanning axis.
On the basis of this vector of samples, it is then possible to elaborate measurements according to different formulas relative to the average diameter, absolute maximum, and absolute minimum of the entire explored surface. Other measure shape errors like taper, barrel shape, and straightness can be elaborated as well.
Circumferential scanning of cylindrical components
The same concept of digital scanning can be applied to measure dynamic diameter and circularity of solids of revolution. In this case, the measured part is carried in rotation with constant speed during the acquisition of the parts diameter measurement.
Depending on the number and arrangement of the measuring points needed, several part measurements are elaborated. For example, the average minimum or maximum diameters, and shape errors such as ovality and roundness.
For more complex parts, like a cam-shaft, the digital scanning for the profile of the cam must be performed to control the real shape and evaluate the correct functional behavior of the component.
Scanning inspection is always applied to gauging equipment with dynamic measurements. Typical applications are:
- M39S Scanning System, for the axial scanning of injection components
- M57 Profile and M110 Profile, for scanning of the cam profile
- OPTOQUICK for scanning of camshafts and crankshafts
- G25 probe for scanning on grinding machines, machines for gears and machining centers