Technologies -- Balancing, Acoustic & Vibration Sensors
In recent years, there has been an increase in the rotation speed of grinding machine spindles and in the use of CBN grinding wheels. The reason for this, is to obtain machines that are capable of achieving superior levels of surface finish. With such levels of performance, the vibrations caused by the imbalance of rotating mechanical parts, in particular the grinding wheel support spindle, as well as the operating conditions of the grinding wheel, need to be constantly monitored.
Today the demand for highly reliable and flexible machining processes is constantly growing. Therefore, the grinding process must become more and more intelligent.
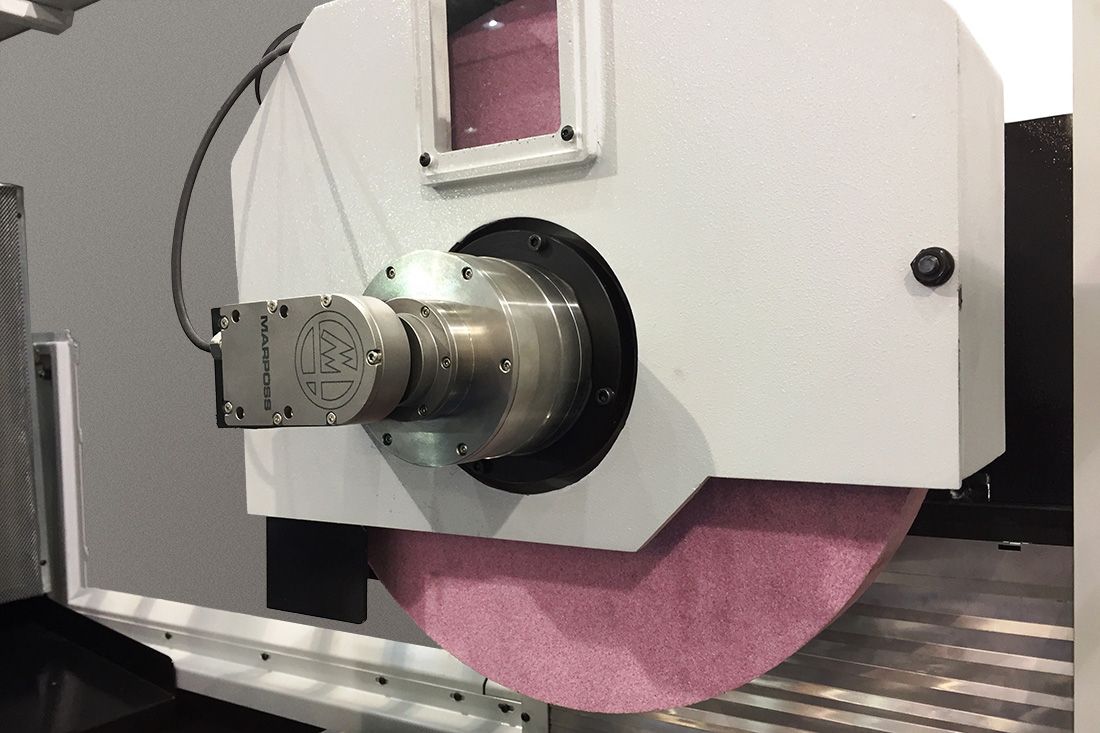
BALANCING AND VIBRATION SENSOR
The vibration is caused by an imbalance of mechanical parts, especially the rotating grinding wheel. Vibration is also caused by the following:
- Uneven distribution of the grinding wheel;
- Assembly dissymmetry in the grinding wheel and assembly flange;
- Uneven wear of the grinding wheel;
- Splintering of the grinding wheel and absorption of coolant.
In order to compensate the aforementioned imbalance, the vibration must be measured first, in its frequency, amplitude, speed, and acceleration, with a vibration sensor (accelerometer) using piezoelectric technology.
The vibration sensor consists of a seismic mass connected to a piezoelectric transducer (usually quartz), that reads the vibration in acceleration and converts it into an electric signal to be processed.
The static (1 plane) or dynamic (2 planes) imbalance can be corrected automatically by a balancing system, usually electro-mechanical, that continuously and automatically compensates the imbalance with mechanical counterweights.
Balancing systems can be installed externally or internally to the spindle, on most grinding machines for exteriors, centreless grinding, grinding for tables, gears, and special grinding.
Almost all grinding wheels are balanced manually by the operator who places compensation weights on the flange of the grinding wheel. However, these operations require qualified personnel and can take a long time for the task to be performed correctly. Grinding wheels can be balanced more easily and effectively by installing an automatic balancing system directly in the machine. This solution provides various advantages when compared to manual methods, such as:
- Greater balancing accuracy;
- Short cycle time (down to a few seconds);
- A completely automatic balancing cycle;
- Compensation on one plane (static imbalance) or on two planes (dynamic imbalance);
- Qualified personnel no longer required;
- Constant check of the vibration throughout the life of the grinding wheel.
ACOUSTIC SENSOR
The grinding operation can be divided in the following two processes:
- Grinding wheel conditioning process (positioning and dressing)
- Part machining process
The grinding wheel conditioning process, is necessary after the part machining process in order to return the grinding wheel profile to its original condition. Note: it’s extremely important when using super abrasive grinding wheels.
For the part machining process, useful information must be supplied to optimise the process. This includes cycle-time and total machining cost, as well as monitoring any unexpected failure (e.g. crash).
These processes can be monitored by sensors using ultrasonic technology (acoustic emission) that can monitor the noise emitted at the point where the part or the dresser touch the grinding wheel. The noise is usually referred to as acoustic emission signals that are elastic waves with a wide frequency range (up to 1000 kHz); generated by the energy stored and released inside the machine structure.
The acoustic sensors placed on the grinding machines must, therefore, become the machine and operator's sixth sense. That is mostly needed as the current automation of the machining processes no longer allows a direct view of the part, due to the high operating pressures of the lubricants and coolants required to work at high speed. Installing the sensors directly in the machine provides the following advantages:
- The air gap check reduces cycle-times by optimising the change in the grinding wheel approach speed.
- The crash check greatly reduces the risk of operator’s injury and of catastrophic damages to the grinding wheel or machine.
- The dressing control detects the grinding wheel-dresser contact, to speed up the dressing cycle and prevent damages to the grinding wheel.
- The CBN grinding wheels require a specific acoustic analysis to optimize the dressing operation, due to the extreme cutting conditions and high costs of the abrasive material.
- System monitoring reduces the costs of the grinding operations and saves the grinding wheel.
- System monitoring increases the safety of personnel and prevents damages along with high maintenance costs.