Leak Testing Of Battery Pack With Helium In Accumulation Chamber
Leak testing is a fundamental operation in the battery pack assembly process, to check the hermetic seal of the battery pack, in order to prevent the entry of water, humidity, dust or other external contaminants, which could cause a short-circuit on the high voltage components contained inside.
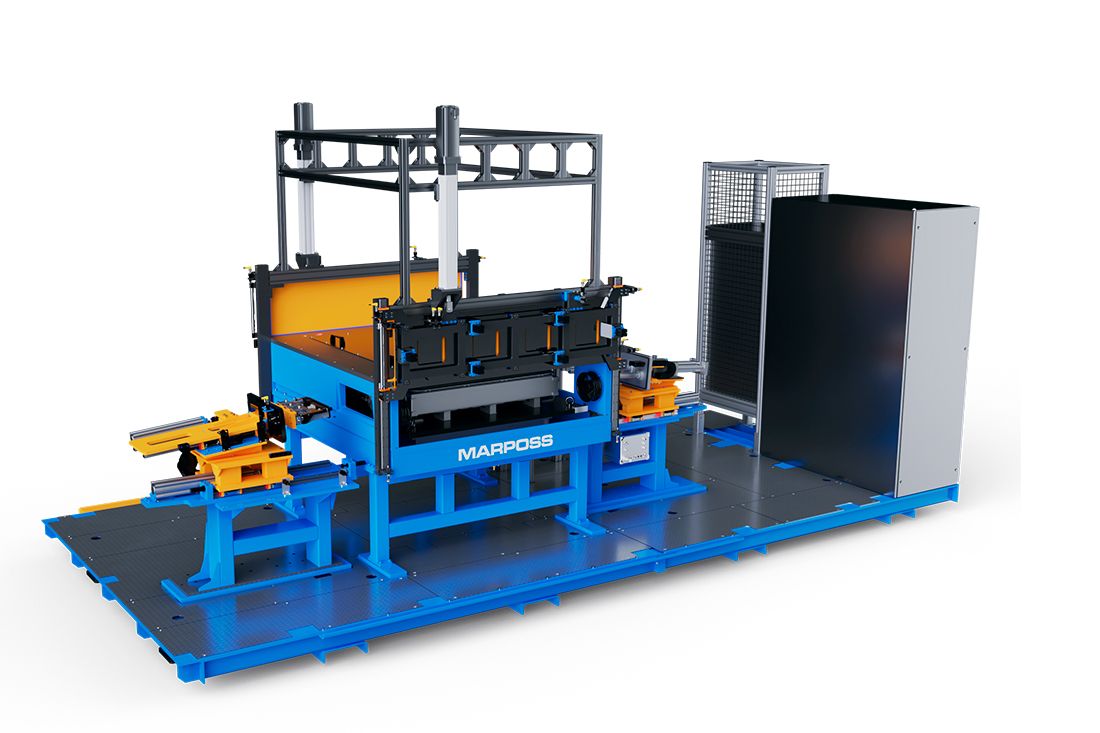
For 100% quality check in mass production, global leak testing methods could be requested to minimize the testing time
Whenever it’s not possible to apply air methods (pressure decay or mass flow), because they are not compatible with the testing specifications, helium tracing in accumulation chamber represents an optimum compromise for highest testing sensitivity and minimum cycle time.
The part under test is introduced into a sealed chamber at ambient pressure, and successively filled with helium, in order to detect through a mass spectrometer any passage of tracer gas from the part to the chamber.
This technique of control on the finished components and total assembly provides a reliable method to guarantee the global sealing and prevent the entry of water inside the pack
The testing method with tracer gas guarantees the maximum sensitivity and the possibility to identify extremely low leaks, also for big volumes and in any environmental condition.
Our helium leak test systems in accumulation chambers are capable of testing leaks with thresholds in the range of 10-2 - 10-4 SCC/sec. This technology provides great results in this range and makes the application simple and reliable.
The application is completed with air testing method (pressure decay or mass flow) for checking of the assembled cooling circuit.
- Detects leaks up to 10-4 SCC/sec
- Tracer gas method independent on part and ambient temperature
- Suitable for testing of parts with big volumes and deformable housing
- Cycle time optimization, not depending on the extension of the sealing surfaces
- Built according to customer’s specifications
- Dedicated or flexible solutions
- Robust construction
- Fully automatic solution or manual loading
- High reliability
- Low running costs
- Detected leaks up to 10-4 SCC/sec
- Cycle time depending on the specific application requirements
- Fully automatic testing station
- Possible manual application, for low volume production lines
- Integrated air method (pressure decay or mass flow) for testing of the cooling circuit