Gauging & Inspection Of Sofc Semi-Cell
The increasing focus on clean and sustainable energy production has given a significant boost to the study of innovative systems and among these, solid oxide fuel cells (SOFC), are those that offer the greatest advantages in terms of fuel use and high conversion efficiency. Due to the high temperatures that are generated during the production of energy, cathode and anode are made of ceramic materials. Despite the use of high performance ceramic materials, the very high temperatures reached by the cells mean that it is necessary to have components realized without defects in order to ensure high mechanical resistance to the stresses caused by thermal expansion.
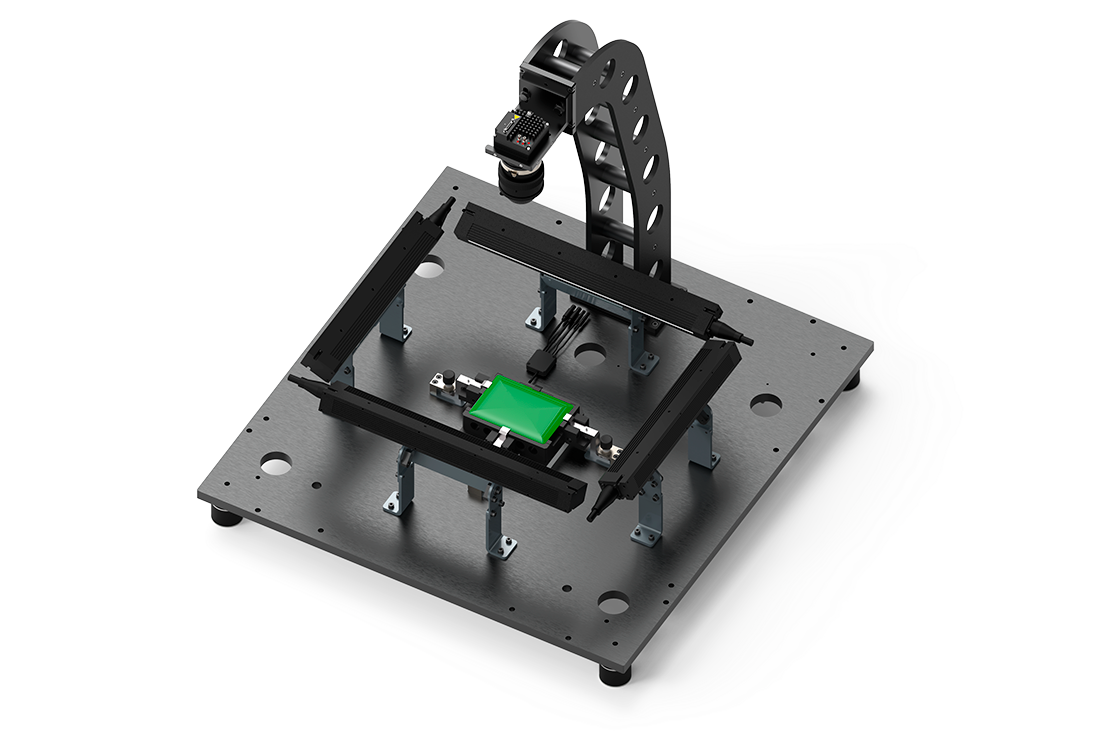
The production of cathode and anode by sintering, leads to the formation of defects on the surface that can cause the malfunctioning of the single component, affecting the operation of SOFC once assembled. Typical surface defects are porosity, scratches, hollows, and the general presence of contaminants such as granules. The solution proposed to verify the presence of these types of defects is the use of machine vision systems able to detect surface unevenness through high resolution camera and grazing light to emphasize the presence of even the smallest defect.
It is also possible to verify the geometry of the electrodes by means of laser sensors that, scanning the surface, are able to reconstruct the 3D profile of the piece measuring overall dimensions and curvature.
- Contactless
- Fast and accurate
- Flexible for different part type
Depending on customer’s requirements