Electrical Test Of Battery Packs
Marposs, strengthened by the knowledge and skills already proven in the field of electro-mobility, provides testing systems dedicated to battery packs. Downstream of the cell and module test applications, Marposs completes the manufacturing chain of electric accumulators with systems dedicated to packs of different size and composition, whose electrical characteristics are detected and measured both in terms of performance efficiency and compliance to safety standards.
Semi-automatic solutions can be set up, where an operator connects and disconnects the connections or fully automated applications in which the packs are handled by AGV and the wiring takes place without human intervention.
These machines can be used for the end-of-line test (EoL test) in the production of packs in multiple configurations, given the modularity with which they are conceived.
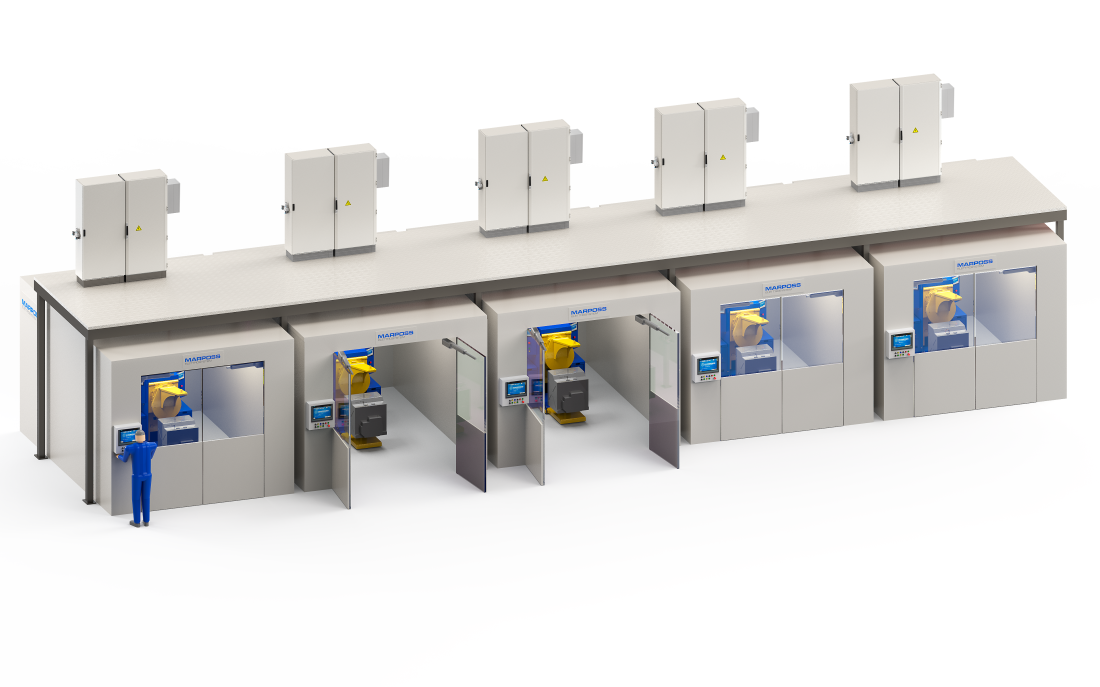
Example of pack testing machines.
A compact solution, in which the electrical and electronic components are located on a structure that insists above the test cabin. Connection and disconnection is the responsibility of the operator. The safety of the test area is guaranteed by appropriate devices for opening the electrical circuit, by a thermal camera for constant detection of the temperature of the pack under test and by fire prevention systems connected to the plant network.
The electrical test can be integrated with pneumatic or helium leak testing of the battery pack.
The electrical tests performed on the pack are:
- Insulation measurement and electrical rigidity test
- Electrical continuity test
- OCV control and comparison with internal measurement
- Fully configurable pulse power test
- Functional check of the BMS
- HVIL safety functionality check
- Check of OCV homogeneity of the cells in the module and their temperature
- Verification of the SOH and internal logic of the CMC
- Possible cooling of the pack with fluid
- Measurement of module and pack capacity (statistical check)
- E9066 PC integrability for statistical control and control charts
- CAN traffic log in a file associated with the part number
- Firmware flashing
This configuration is particularly suitable for use in production lines for medium-high volumes. The modular concept allows you to easily increase the capacity by gradually adapting it to the needs of mass production.
- Architecture based on industrial PLC hardware particularly robust and flexible
- Modularity of the power supply
- Calibration and certification procedures for each electrical measurement
- High degree of adaptability to any module shape and connector position
- Solution designed for manual or automatic part loading
- Wide range of electrical tests available and freely configurable by the customer
- Xivity of the active test
- Energy exchange with the electricity grid during the pack discharge phase
- Recovery of thermal energy dissipated by fluid for the benefit of the plant's winter air conditioning
- Data logging for Industry 4.0 compliance
- Compact solution
- Minimum maintenance
- Manual part handling
- Automatic part handling
- Manual connection of power and signal cables
- Automatic connection of power and signal cables
Dimensions (HxWxD) | 3000 x 3500 x 4500 mm (without upper cabinet) |
Efficiency | 98% |
Cycle time | depends on the pulse power cycle (from 3 min to 30 min) |
Min / Max power range of the module | 18kW / 1.2MW |
Maximum test power | 1500V, 800A |