SOFC Stack: End-of-Line Testing Station
End of Line testing is a necessary part of the manufacturing process, since it is the last checkpoint before a product leaves the factory. End of Line station is a testing system positioned at the end of the fuel cells assembly line. It allows the quality control and the performance testing of the SOFC fuel cell stack by checking the most relevant parameters of the component.
The SOFC stack tested is one type, and it consists of no.70 cells grouped in no.10 different cluster. Utilizing a different stack interface and, eventually, an SW modification, it is possible to test other types of stacks of similar size.
The diagnostic test performed is the Polarization curve at 700°C: during this test, the voltage of each cluster of the stack is measured with a gradual increase of the current. The bench has to perform a heating curve (defined by the Customer), that consists of a gradual heating of the stack up to a maximum temperature of 910 °C and a controlled cooling of the system to room temperature.
The station is controlled by an electrical control cabinet, designed to manage five additional stations.
This test is the most important of the Fuel Cells production chain because it guarantees the perfect functionality of the product and its readiness to be mounted in a Fuel Cells final equipment. It also guarantees the quality and safety standards required by the market.
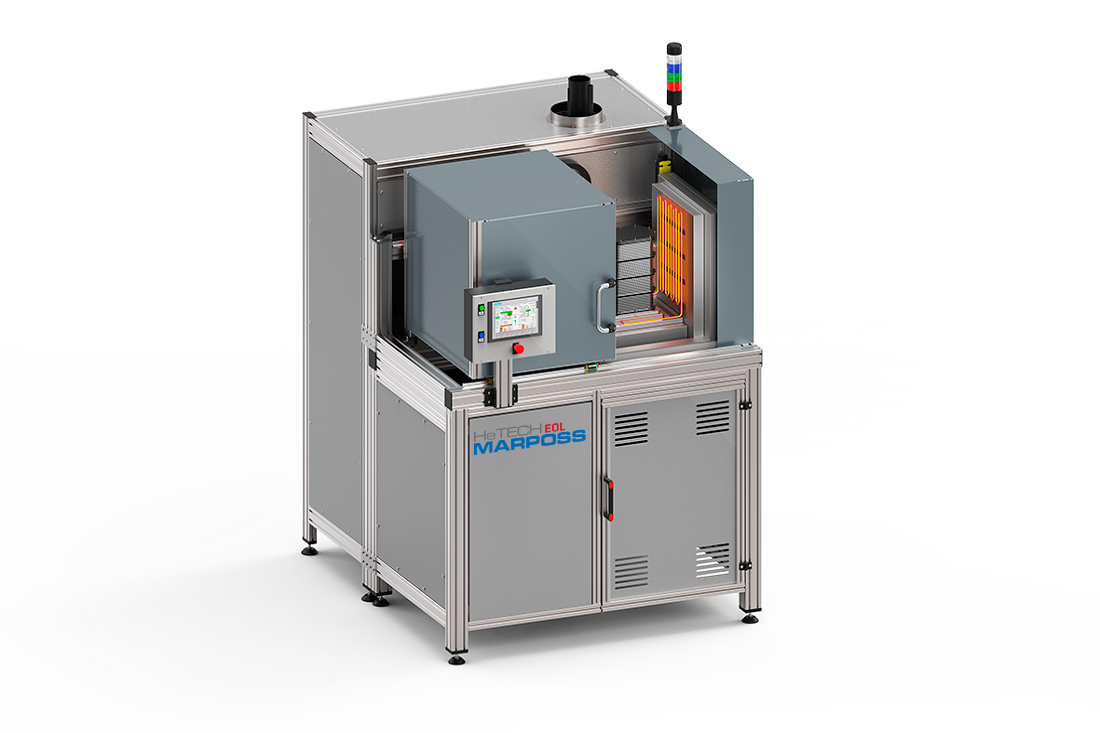
The machine provides one station assembled on aluminium profile frames, covered by removable panels. It is mainly composed of a furnace, which main body slides horizontally in order to manually enclose the stack to be tested. Automatic closing (by pneumatic or electrical devices) is also feasible.
On the front, there is a small electric local box, that manages the measurement instruments installed in the bench.
In the rear part of the station, there are three separate inlet ports for the process gases: air, nitrogen, and hydrogen. The process circuits develop from these ports and the gases are preheated to the stack operating temperature. At the stack outlet, the exhausts gases are mixed with dilution air and conveyed to the chimney.
For safety purposes, a hydrogen detector is installed in the rear part of the bench, to potentially detect leaks from fittings and flanges.
The electric switchboard has a dedicated cabinet. Furthermore, the control cabinet accommodates the electronic load, the electrical device that allows it to perform the polarization curve.
A local HMI touch panel is integrated in the station for the visualization of the main parameters. A central industrial PC is integrated in the control cabinet for the communication with the PLC of the station and the data management.
The machine is provided by CE mark, according to the European norms, and by ATEX certification.
The station tests a SOFC stack with a nominal power of 1,5kW.
- Evaluation of the quality of the product, stability, and yield of the production process.
- Reliable detection of failed drives, reduction of the rejection rate and maximization of the output.
- Certainty that stacks are produced according to appropriate specifications and standards.
- Indication of when to start troubleshooting to reduce failure rates.
- Experience gained in a significantly increasing new market segment to support other customers in the development of similar projects.
Basic configuration of the machine:
Stack nominal electric power |
1,5 kW |
Operating temperature |
up to 910°C |
Qualification time | 24 h |
Polarization test time | 45 min |
Manual loading/unloading (upgrade possibility for semi-automatic and automatic loading/unloading) |