R2Rプロセスにおけるリチウムイオンバッテリー電極のインライン測定および検査ソリューション
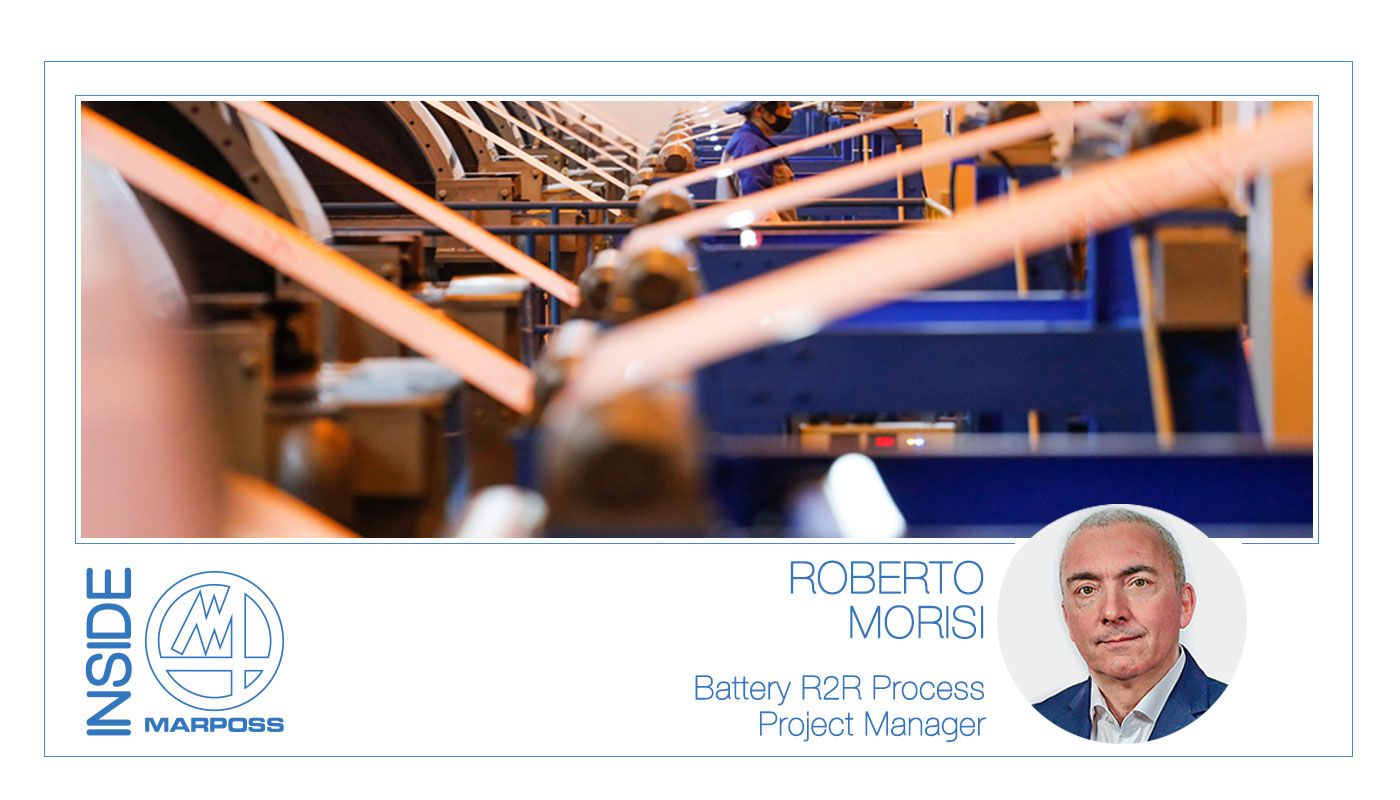
バッテリーの誕生から...
バッテリーは200年以上前の発明でありながら、従来以上に現在関心が高まっています。
最初の近代的なバッテリーは、1800年代にイタリアの物理学者 Alessandro Volta (アレッサンドロ・ボルタ)によって発明されました。バッテリー、特にリチウムイオンバッテリー(LIB)は、エネルギーの保存と蓄積において常に重要な役割を果たしてきました。
今日、リチウムイオン技術は、電子デバイス(黒物家電/娯楽家電)や電気自動車(EVモビリティ)の研究と生産増加のために、巨額の投資による恩恵を受けています。
未来に向けた重要なテクノロジー
気候変動に対する緊急かつより集中的な対策の必要性が世界的に広く認識されています。そのため、リチウムイオンバッテリーは今後10年間、継続的な開発と気候変動の緩和に貢献できます。バッテリーは、温室効果ガス排出量の削減に関するパリ協定を達成するための重要な技術として大きな可能性を秘めています。
より安価な技術は、再生可能エネルギー源への移行を加速させる可能性を秘めています。これにより、電気自動車への人気の高まりは、今後数年間でリチウムイオンバッテリーの大きな需要に拍車をかけるでしょう。そして、多数の大規模な生産工場を建設するために必要である高品質な生産設備の世界市場のボリュームが、2030年まで毎年30%以上成長していくと考えます。
リチウムイオンバッテリーの高コスト生産チェーンにおける「ロール・ツー・ロール」(R2R)プロセスを使用した電極フォイル(カソードおよびアノード)の処理は、生産チェーンの最も重要なステップのひとつです。生産ラインの速度を上げ、無駄を最小限に抑えることでコストを削減し、前述の目標を達成することができます。
マーポス:リチウムイオンバッテリー製造プロセスのインライン測定、検査、品質管理
電極の製造に関する課題は、ステージ固有のものです。電極製造における主なオペレーションの中で、マーポスのインライン測定、検査、品質管理システムが必要とされる場所を見てみましょう。
電極のコーティングと乾燥の測定:クロマチック共焦点プローブ
電極形成のために、成分(金属箔およびスラリー)は溶媒と混合され、液膜として金属基板上にロール・ツー・ロールでコーティングされます。金属箔は可能な限り薄く、陰極はわずか20μm(アルミニウム)、陽極は10μm(銅)未満です。電極膜の表面のコーティング量は、将来のリチウムイオンバッテリーセルの要求によって決まります。
高エネルギーアプリケーションでは、静電容量を大きくするために、はるかに厚いフィルムが必要です。これにより、通常、乾燥電極の厚さが30〜200μmの範囲になります。リチウムイオンバッテリー電極の生産ラインでは、乾燥工程はコーティング工程の直後です。
プロセスのこれらの段階では、表面に欠陥や汚れがなく、コーティングのエッジ形状がきれいであっても、コーティングされた電極の均一性(剥離の無い)と均一性(連続的な厚さ)を制御することが不可欠です。クロマチック共焦点技術により、コーティングの厚さとエッジの形状のインライン検査を高精度で高周波サンプリングできます。
マーポスは、グループ企業であるSTIL(スティル)とともに、幅広い高性能光学機器を提供しています。約30年の経験を持つSTILは、非接触センサーの最先端技術であるクロマチック共焦点イメージングの発明者です。STILは、この革新的なテクノロジーに基づいて、ポイントセンサー(測定範囲0.1mmから100mmまで)とラインセンサー(測定範囲が異なる1.35mmからライン長4mmまで)の2つのセンサーファミリーを設計しました。
電極カレンダリングの測定と検査:共焦点技術
カソード電極とアノード電極は、乾燥工程後にエネルギー密度を高めるためフィルムはカレンダー加工されます。カレンダリング中、電極コイルはロールプレスを通過して活物質を圧縮し、膜厚と気孔率を減少させます。主な目的は、電極の体積を減らして体積密度を上げ、その表面を平らにすることです。
電極を過度に圧縮すると、電解質がその構造に浸透できないレベルまでその多孔性が低下する可能性があります。ここでの品質管理要件は、前のコーティングステッププロセスの要件と非常に似ています。最終電極の厚さの偏差は注意深く制御する必要があります。また、コーティングステップ中に形成された不均一性の結果として、ドロップオフコーティング、致命的な損傷、ピンホールなどの欠陥を検査する必要があります。
STIL 共焦点技術は、この重要なプロセスステップでの幾何学的測定と検査に最適なソリューションです。
電極のスリッター:レーザーマイクロメーター測定システム
スリッティングは、大きな電極コイル(マザーロール)をいくつかの小さな電極コイル(ドーターロール)に切断するプロセスです。
ロールからロールへ処理される加工前の電極の全長は、最大2000mで、幅は1000mm を超える場合があります。この工程の方法は、要求により異なり、カソードの材質は非常に研磨性が高いため、電極はセラミックブレードで切断されます。
測定結果は、ブレードまたはスリットを入れる電極の間違った位置を特定するプロセスにおいて重要なステップです。電極エッジの切断品質と、コイルの清浄度が主な品質基準と見なされます。ドーターロールの切断幅は、セルの設計によって異なりますが、多くのアプリケーションで60mmから300mmの間です。
重要なことは、このステップの幅プロセスの監視で、品質測定と非接触技術などのインライン制御によって電極製造の無駄なスクラップ率を減少させることです。
従来の接触式測定では測定することができないデリケートな素材のインライン幅測定を行うために、AEROEL(エアロエル)は独自のレーザーマイクロメーターを提案しました。
非接触測定機能により、AEROELレーザースキャナーは、ロール・ツー・ロール生産プロセスにおいて迅速、正確、効率的に使用できます。また、リチウムイオンバッテリー電極の製造では、レーザー光学技術が工場で一貫性のある客観的で正確な結果を直接保証します。特許で保証された革新的な技術ソリューションが、通常は生産環境での測定結果に影響を与える温度変化、振動、箔の動き、ほこり、その他の環境条件に影響されない品質管理システムを実現します。
電極の分離(ノッチング)の検査:Machine Vision(マシン・ビジョン)ソリューション
パウチセルの製造には、分離またはノッチングが必要であり、ロール材料(ドーターロール)からのアノード、カソード、およびセパレーターシートの分離について説明します。ノッチングプロセスは通常、連続プロセスでせん断カット(パンチングツール)またはレーザーカットを使用して実行されます。
このプロセスステップで検査する最も重要な品質パラメータは、バリの品質、刃先の形状、異物金属粒子、および電極の微細構造の変形です。
ミクロン単位の金属の削りくずも、敏感なセパレーターを損傷し、完成したセルの短絡を引き起こす可能性があります。したがって、欠陥がコーティングから出てくると非常に危険です。(電流と電界の影響または短絡)したがって、電極の中心位置からの金属箔(アルミニウムまたは銅)のずれを確認することが重要です。
マーポスは、特許出願中のインライン・Machine Vision ソリューションにより欠陥管理を解決することができます。システムは、バリ、折り目、および層間剥離の存在を識別する電極プロファイルの品質における負の傾向を統計的にチェックし、追跡します。
ビジョン・インスペクション・システムは、電極のエッジをフレームに収め、一連のデジタル画像を取得する高解像度リニアカメラを搭載しています。これらの画像を分析して、金属バリの存在の可能性をチェックします。このシステムには、電極のエッジとリニアカメラの間の距離の変化を検出するマトリックスカメラも含まれています。処理装置(コントローラ)は、電極の端部と光学系との間の距離の変化に応じて、リニアカメラの焦点を変えるように構成されています。
この時点で、これらのロール・ツー・ロール工程で、リチウムイオンバッテリー電極は、積層、パッケージング、充填、シール等のセルアセンブリプロセスの準備ができ、最初の充電が実施されます。
リチウムイオンバッテリープロセスの改善においては、主に電極の生産とセルの最終仕上げに革新があり、生産の増加に役立っています。
マーポスは、さまざまなパラメータの監視と技術によって、生産フローのリチウムイオンバッテリーセルアセンブリの品質測定および検査ソリューションを保証します。
マーポスグループは、幅広い技術とソリューションにより、エレクトロモビリティの世界において品質およびプロセス制御における主導的な役割を果たすことを目指しています。
R2R プロセス向けマーポスインライン測定&検査ソリューションの詳細をご覧ください。