VTS and Total Tool Inspection
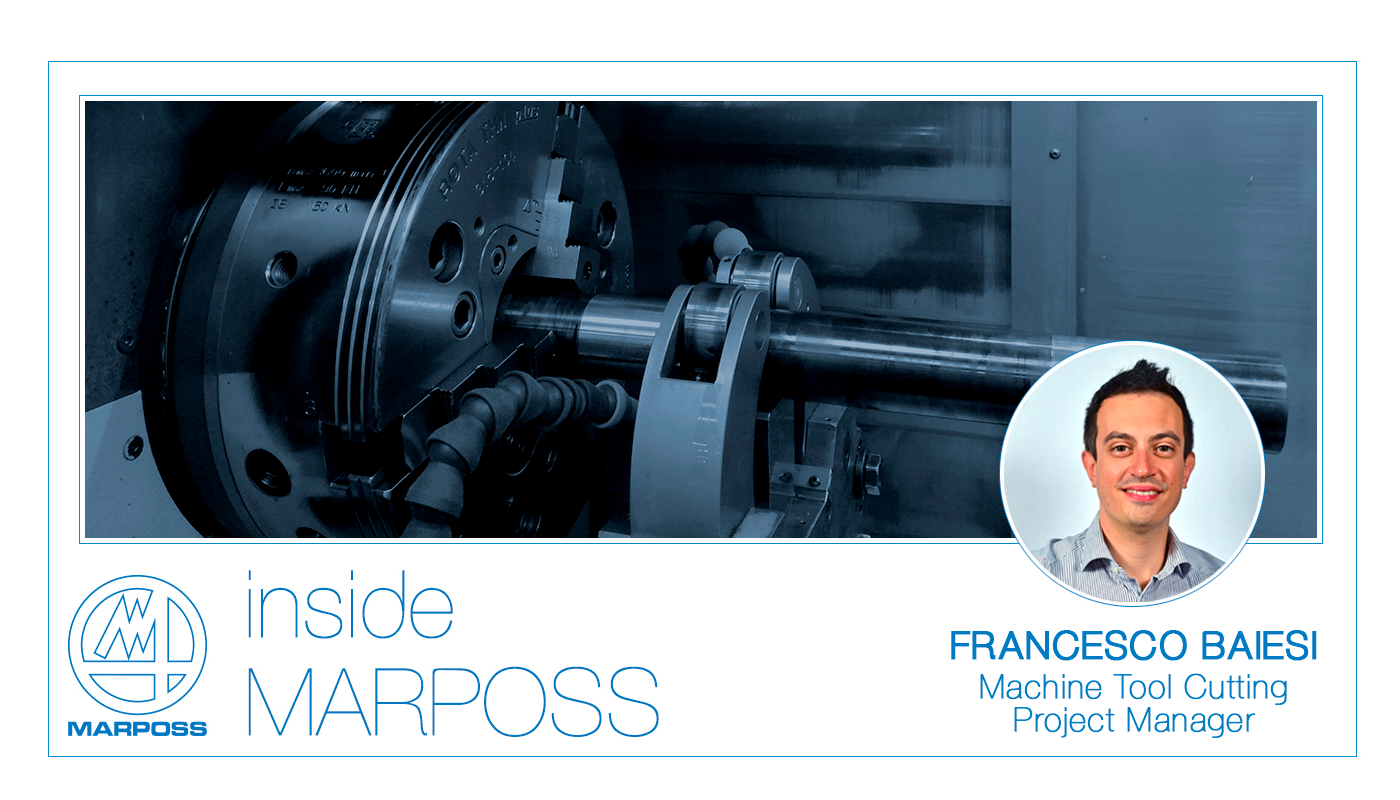
It is difficult to measure turning and boring tools using traditional Non Contact Tool Setters, but not with VTS: the only commercially available device capable of measuring static tools in the machine in the blink of an eye and inspecting the integrity of each individual cutting edge.
Total Tool Inspection with VTS - Visual Tool Setter - exploits the vision in order to define the fingerprint of each individual tool, providing unique information about it.
The VTS indexes the machine spindle in order to assume the angular position necessary to measure each cutting edge on the tool as quickly as possible, including details that are hard to measure using other types of instrument, such as surface wear and the cutting profile.
In-machine tool gauges offer a series of intrinsic advantages that are common to all in-machine gauges. In addition, the visual gauge is also capable of performing measurements that other systems cannot carry out, rapidly and precisely.
The VTS works on the shadow projection principle: the illuminated object projects its shadow onto the VTS camera, which uses the resulting outline to acquire information, such as the “radius of curvature” and the radial and axial dimensions, that may be used to obtain a perfect cut.
In addition to carrying out perfect measurements on the tool in the machine, the VTS also checks the state of the cutters, taking a reference photo of each elements in order to document the history of the tool and all its parts.
It detects whether the cutters are broken, chipped or worn while in use, so that it is possible to implement solutions in advance.
With Total Tool Inspection and VTS it is possible: to check the profile integrity of cutters and/or their surfaces; check the radius of curvature, runout, measure length and diameter, and all in a fraction of the time required when using traditional tool setters.
Simply position the tool inside the device, frame it with the camera and take a photograph. Device software generates the various measurements in a single step, some of which are impossible to detect using other types of tool setter.
The VTS measures the axial and radial position of the tools and, thanks to the calculation performed by the measurement macro (a program running on the numerical control system), the tool length and diameter are determined. The results are independent of the shape of the part.
Tools may also be measured using Double Side mode (Double side Tool diameter) when it is possible to frame both extremities of the tool (the left and right hand parts), resulting in a direct measurement of the tool diameter.
Alternatively, in the case of very large tools, it is possible to determine the diameter even when only one side is visible (Single side Tool diameter), thanks to the indirect measurement feature.
The brand new VTS WF (Wide Field) version has been designed to meet every type of requirement - especially in the case of Turning Centres - and is capable of resolving a wide range of problems, thanks to its increased measurement area, which permits it to measure large tool diameters and to inspect a wide range of tools for turning processes.
It can be used to measure any type of tool, including tappers; drill bits; mills; face milling cutters; contouring milling cutters; spherical head milling cutters etc., at diameters ranging from 40 microns up to 80 mm.
It is the ideal system for applications requiring perfect, defect-free parts, such as the jewellery, watch-making, biomedical, automotive and aerospace sectors, where highly sophisticated machines are used to produce high quality parts with excellent surface finishes, which may be guaranteed only by constantly monitoring the dimensions and condition of the tool.
By measuring the runout error, the VTS safeguard the integrity of the tool, interrupting the machining process when they are observed to rotate out of axis or simply by monitoring dynamic tool diameter in order to avoid rejects during production.
Thanks to the precision of the vision technology, VTS exceeds the performance specifications of all other in-machine tool setters. The VTS may be used to measure tools having differing diameters and shapes, maintaining the accuracy error at around 1 micron, thus reducing costs and processing times!
✔ Traditional Tool Setters = 5 μm < ACCURACY < 15 μm
✔ VTS = ACCURACY < 1.3 μm