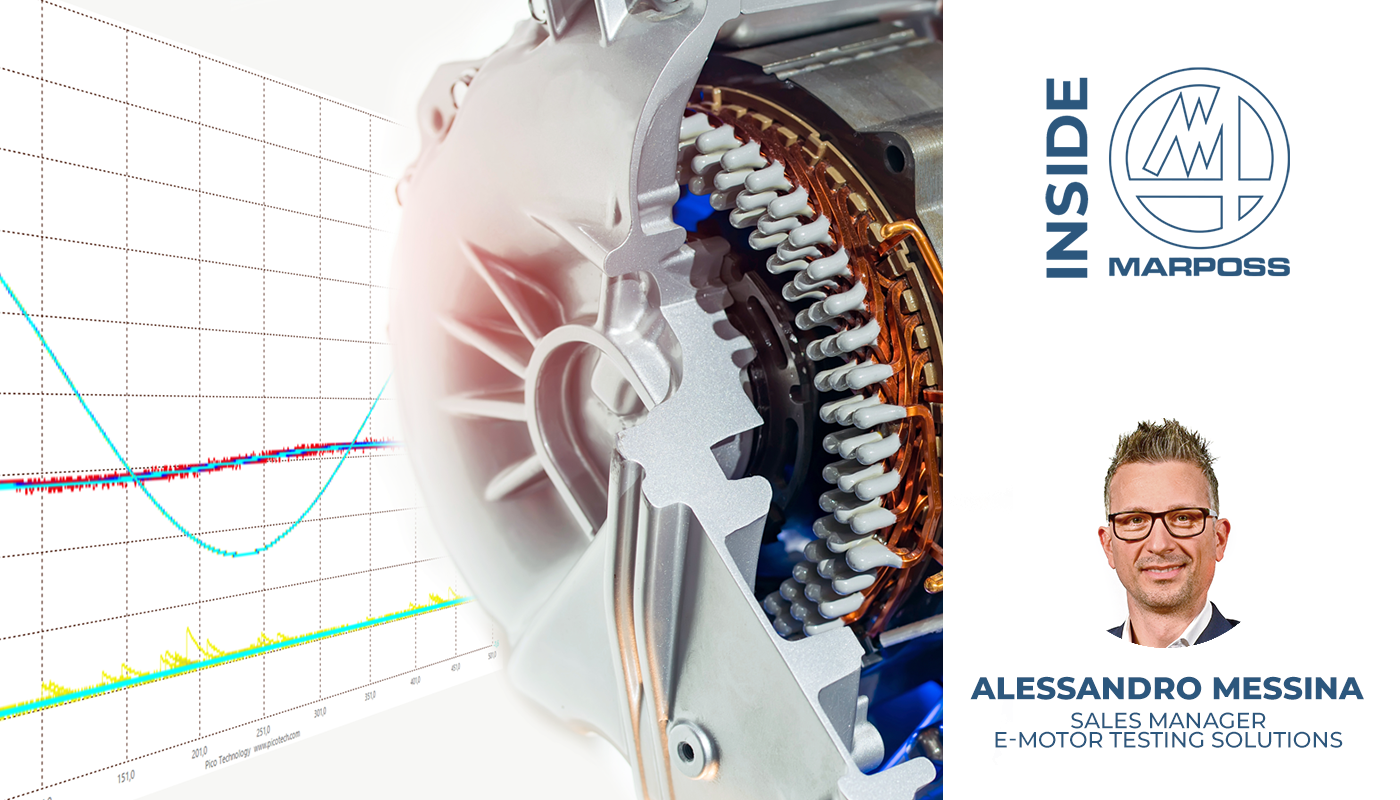
The transition underway in the automotive sector, from internal combustion engine to electric powertrain, is producing important changes in the criteria used for quality and process control in the production of electric motors. As electric motors become ubiquitous in automotive applications, ensuring their long-term reliability is paramount.
Detecting insulation defects in stator and rotor windings is critical for ensuring motor efficiency and longevity. This test has always represented a crucial operation, both in the design phase and during fine-tuning and in the control of the production process. Insulation defects can generate a short circuit between the turns of the same phase or between the different phases of a stator or between the windings and the casing, When a short circuit occurs, it creates an unintended low-resistance path for current flow. This can lead to excessive current, overheating, and ultimately damage to the motor windings. Insulation defects can result in decreased motor efficiency and potential malfunctions or failures.
In order to detect the presence of such insulation defects, the regulations provide for the execution of specific tests such as SURGE and HI-POT, which must be carried out on 100% ofproduction, in order to guarantee the quality of the final product.
However, not all insulation defects can be detected by these tests, but only those where the loss of insulation is such as to generate perforation of the insulation with high energy transfer. HI-POT are inadequate for detecting latent defects, which can cause insulation perforation over time. These defects, though seemingly harmless initially, can trigger catastrophic failures, especially in motors driven by inverters. Therefore, a sensitive and reliable testing method capable of detecting these latent defects is needed.
There is a wide range of small insulation defects thatare not capable of generating a high current flow t and therefore cannot be detected by these tests: small air bubbles trapped in the enamel of the wire or hairpin, small tears in the insulating paper in the stator slots, imperfect or incomplete resin impregnation of the windings on the stator itself, produce a reduction in insulationqualitythat is not sufficient to cause a short circuit.
If these defects are unlikely to cause a short circuit during testing, the reader might wonder why he should bother to detect them. Unfortunately, these are the most insidious defects, those that can be defined as latent defects , apparently harmless in the early stages of use of the motor, but which can act as a trigger capable of leading to complete perforation of the insulation in a short time.
The small air bubble in the insulating enamel, when it appears, for example, on the contact surface between two hairpins, is not capable, at least initially, of generating a massive current passagebut only micro discharges, the so-called partial discharges . However, these partial discharges,which are continuously repeated at each voltage peak, are capable of producing a continuous weakening of the insulation, whichinevitably leads to its perforation. Perforation can occur after a few days or a few months of use, depending on the size of the latent defect and the severity of the working conditions of the motor.
The phenomenon is particularly noticeable on motors driven by inverters , such as all traction electric motors (... but not only), where the modulation of the pulse amplitude generates overvoltages that can aggravate the thermal and electrical stress of the insulation.
The particular severity of the operating conditions, combined with the traditionally high quality control standards of the automotive world, have made the study and prevention of latent insulation defects has become an essential necessity in the production of traction e-motors.
The Partial Discharge Testing Method is a reliable method to detect all latent defects. The analysis of insulation conditions using the partial discharge testing method is first used in the design and development phase of the process. The test is carried out in Laboratory mode and consists of repeating the test with progressively increasing voltage, until the first partial discharges are triggered, thus determining the PDIV (PARTIAL DISCHARGE INCEPTION VOLTAGE). Keeping in mind what the nominal conditions of use of the motor should be, it is therefore possible to vary the project parameters (e.g. choice of insulating material) or the process parameters (e.g. duration of the impregnation cycle) in order to guarantee a sufficient safety margin with respect to the inception voltage By conducting these tests during the design and development phase, engineers can optimize insulation materials and manufacturing processes to ensure a sufficient safety margin. Additionally, performing these tests on the production line ensures the absence of partial discharges at nominal voltages, guaranteeing the quality of the final product.
Quality and process control then require that the same type of test is repeated 100% on the production line, to verify the absence of partial discharges at the nominal test voltage.
From what has been said, it is clear how important it is to have a test method capable of detecting partial discharges generated by latent insulation defects, with high sensitivity and reliability, both in the laboratory and on the production line.
In fact, there are various techniques for performing this type of test with excellent performance; but not all of them are equally reliable in a production environment!
Marposs compared the performance of three alternative methods for the measurement of partial discharges (PD) produced by three-phase stators during tests with sinusoidal or pulsed voltages. The three methods that Marposs considered are those described in IEC 61934 for tests with pulsed voltages.
Capacitor coupling proposed by Marposs is the method required by IEC 60270 and allows the level of PD measured during tests with sinusoidal voltages with frequencies up to 400 Hz to be expressed in units of C, therefore allowing for a direct comparison of measurements obtained with different instruments. The level of PD is expressed in nC for tests with sinusoidal voltage and in mV for tests with pulsed voltage. This is the method we use in all our machines.
Antenna method is based on the measurement of the electromagnetic radiation emitted by PD. The result is always expressed in mV.
High-Frequency Current Transformer (HFCT) method senses current peaks occurring in the cables supplying the test voltages to the device under test as a consequence of PD. The result is always expressed in mV.
A direct comparison of the levels of PD measured using the three approaches would be difficult because the second and the third methods only produce a result in mV, whose amplitude depends on the internal operation of the instruments and therefore they are not suitable for a comparison between different instruments unless some kind of calibration procedure is performed.
However, a comparison of the behaviour of the three methods is possible if the PD Inception Voltage (PDIV) is considered. This is the voltage (rms value for tests with sinusoidal signal, peak value for tests with pulsed signal) at which the level of PD exceeds a predefined threshold. Given the aforementioned difficulty in the comparison of the absolute outcomes of the different measurements, we chose to consider as relevant the voltage at which the measured PD signal becomes clearly distinguishable from the background noise.
As a representative of our instruments based on the capacitor coupling method, a Marposs e.d.c. LT400 machine was used. This machine has been designed to be used in laboratories during the design phase of new products, and in quality departments before starting the production of the final model, in order to choose the best test parameters to be used for testing at the end of the production line. Since this machine runs the same software as our machines for production lines, transferring the test parameters to the production line is straightforward. Moreover, the LT400 serves as a high-voltage generator for PD tests, ensuring precise and reliable measurements.
For this comparative analysis, we have used an instrument operating within the UHF band of 200 and 500 MHz, and able to guarantee adequate flexibility by accepting input from either an Antenna or an HFCT. The resulting analog outputs, with broadened PD peaks, simplify subsequent processing, aiding in accurate PD measurement. In order to directly compare the signals measured by the two instruments, both were acquired, together with the high-voltage signal applied to the device under test, using a Picoscope digital sampling scope connected to a laptop..
These tests showed that the three considered methods for the measurement of partial discharges are essentially equivalent for offline tests with both sinusoidal and pulsed voltages. In particular, the capacitor coupling method is at least as sensitive as the antenna- and HFCT-based approaches to real partial discharges.
As far as vulnerability to external electromagnetic noise is concerned, the capacitor coupling showed a much better behaviour, with very small when not totally negligible sensitivity to disturbances, which is fundamental when working in noisy environments like production plants. The antenna and HFCT sensors, on the other hand, showed a higher sensitivity to noise, as may be expected given the physical phenomena on which such sensors are based.
An additional advantage of the capacitor coupling approach is that it allows for a simple and robust calibration of the test systems, thus making the comparison of the measurements produced by different instruments possible. Calibrators are available, for both the sinusoidal and pulsed voltage tests, that generate signals corresponding to predefined levels of partial discharges, expressed in nC for the tests with sinusoidal voltage and in mV for those with pulsed voltage.
As the demand for reliable PD measurement solutions continues to grow, the capacitor coupling method emerges as a robust and versatile approach, offering precise measurements and enhanced resilience to external noise. While alternative methods such as antennas and HFCTs provide valuable insights, their susceptibility to noise underscores the importance of selecting the most suitable technique for specific applications.
Detecting latent insulation defects is essential for ensuring the long-term reliability of traction e-motors. The Partial Discharge Testing Method offers a sensitive and reliable solution for identifying these defects, thereby preventing potential failures. By implementing this method in both laboratory and production line environments, manufacturers can uphold stringent quality standards and deliver robust electric motors for automotive applications.
Innovative solutions like the Marposs e.d.c. LT400 pave the way for advancements in PD measurement, driving reliability and safety in electrical systems. By leveraging the latest technologies and methodologies offered by Marposs for the entire e-powertrain production process, engineers and researchers can continue to push the boundaries of e-mobility.