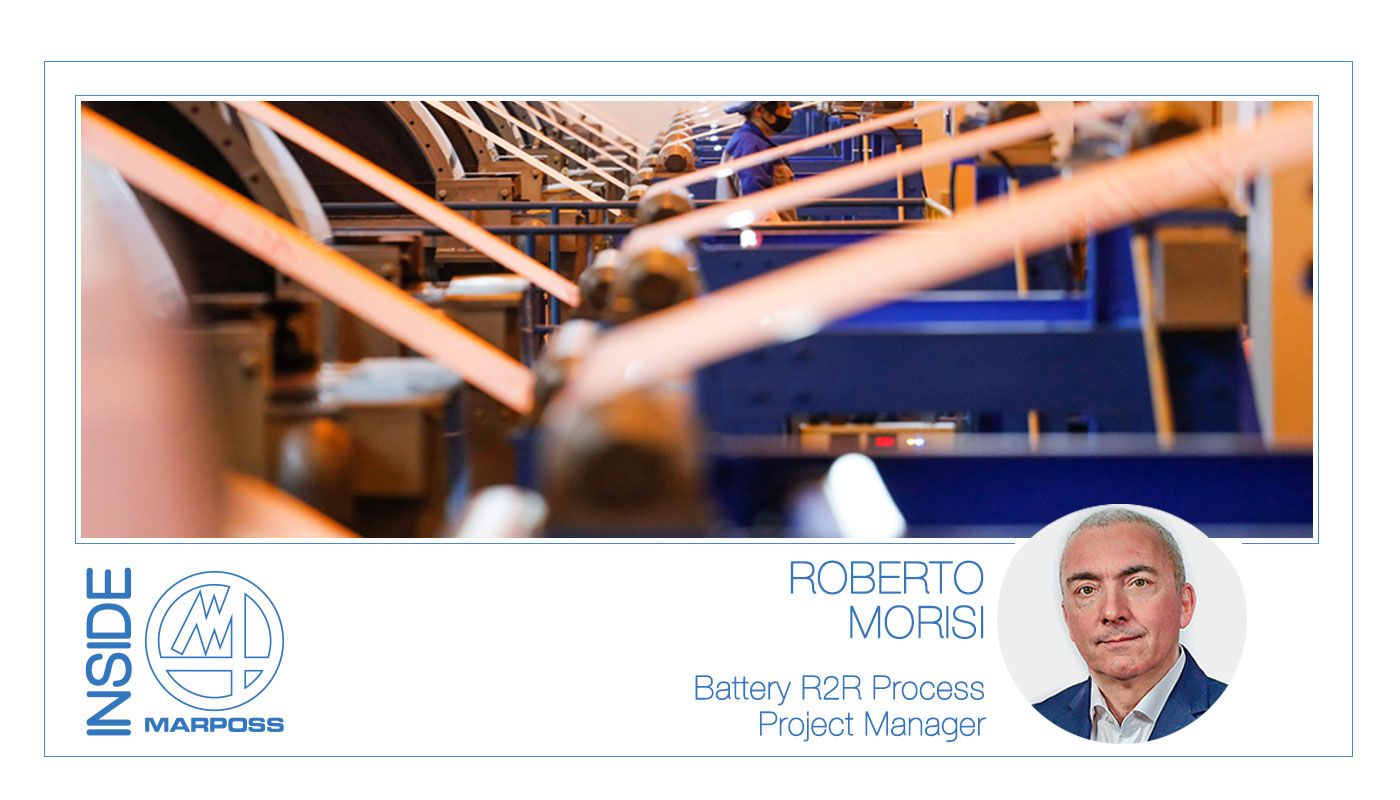
배터리는 과거의 발명품...
배터리. 200년 전의 발명품으로 현재는 그 어느 때보다 관련성이 높습니다.
우리가 알고 있는 최초의 현대 배터리는 1800년대에 이탈리아의 물리학자 알레산드로 볼타에 의해 발명되었습니다. 배터리는 항상 에너지를 포집하고 저장하는 데 중요한 역할을 수행했으며, 특히 현재 리튬 이온 배터리(LIB)에서는 더욱 그렇습니다.
오늘날 리튬 이온 기술은 연구에 대한 막대한 투자와 전자 생활제품 및 전기 자동차(EV 모빌리티)에 대한 대규모 생산의 혜택을 받고 있습니다.
... 미래를 위한 핵심 기술
기후 변화에 대한 시급하고 보다 집중적인 조치의 필요성은 전 세계적으로 널리 인식되고 있습니다. 따라서 LIB는 향후 10년 동안 지속 가능한 개발과 기후 변화 완화에 기여할 수 있습니다. 배터리는 온실가스 감축에 관한 파리협정을 달성하기 위한 핵심 기술로서 엄청난 잠재력을 가지고 있습니다.
더 저렴한 기술은 재생 에너지원으로의 전환을 가속화하는 데 도움이 될 수 있습니다. 이와 관련하여 전기 자동차의 인기가 높아짐에 따라 향후 몇 년 동안 LIB에 대한 수요가 크게 증가하고 있습니다. 수많은 기가 팩토리를 만드는 데 필요한 고품질 생산 장비의 글로벌 시장 규모는 2030년까지 매년 30% 이상 성장할 것입니다.
LIB의 고비용 생산 체인에서 'Roll to Roll'(R2R) 공정을 이용한 전극 포일(양극 및 음극)의 가공은 생산 체인에서 가장 중요한 단계 중 하나입니다. 여기서 생산라인의 속도를 높이고 낭비를 최소화하면 비용을 절감하고 따라서 위의 목표를 달성하는 데 도움이 될 수 있습니다.
Marposs: LIB 생산 공정을 위한 인라인 측정, 검사 및 품질 관리
전극 제조와 관련된 과제는 단계별로 다릅니다. 전극 제조의 주요 작업은 무엇이며 마르포스가 인라인 측정, 검사 및 품질 관리 시스템에 적합한지 살펴보겠습니다.
전극 코팅 및 건조공정 측정: 공초점(Chromatic Confocal) 프로브
전극 성형을 위해 성분(금속박 및 슬러리)을 용매와 혼합하여 금속 기재에 액체 피막으로 roll-to-roll 코팅을 합니다. 금속 호일은 가능한 한 얇아야 하며, 양극은 20μm(알루미늄), 음극은 10μm(구리) 미만입니다. 전극막 표면의 코팅량은 미래의 LIB 셀의 요구 사항에 따라 결정됩니다.
고 에너지 애플리케이션은 더 높은 특정 정격용량을 위해 훨씬 더 두꺼운 필름이 필요합니다. 이는 일반적으로 30~200μm 범위의 건조된 전극 두께 를 가지고 있습니다. LIB 전극 생산 라인에서 건조 단계는 코팅 단계 바로 다음에 있습니다.
이러한 공정의 단계에서 코팅된 전극의 균질성(기공 없음)과 균일성 (일정한 두께)을 관리하는 것이 필수적입니다. 표면 결함이나 오염이 있고 코팅의 가장자리 형상이 깨끗하지 않더라도, Chromatic Confocal 기술을 사용하면 코팅 두께와 가장자리 형상을 인라인 검사방식의 높은 정확도와 높은 주파수의 샘플링으로 측정할 수 있습니다.
마르포스는 계열사 STIL과 함께 다양한 고성능 광학 장비를 제공하고 있습니다. 약 30년의 역사를 가진 STIL은 비접촉 센서를 위한 선도적인 색차 공초점 (Chromatic Confocal) 이미징 기술을 개발하였습니다. STIL은 이 혁신적인 기술을 기반으로 2가지의 센서 제품군을 설계했습니다.: 포인트 센서 (측정영역: 0.1mm에서 최대 100mm) 및 라인 센서 (라인길이: 측정영역별로 1.35mm에서 최대 4mm).
전극 캘린더링 측정 및 검사: 공초점 기술
양극 및 음극의 전극은 건조 단계를 지나서 에너지 밀도를 증가시키기 위해 필름을 캘린더링합니다. 캘린더링 동안 전극 코일은 롤 프레스를 통과하여 활물질을 압축하여 필름 두께와 다공성을 감소시킵니다. 주요 목표는 부피당 밀도를 높이고 표면을 평탄하게 하기 위해 전극의 부피를 압축하는 것입니다.
전극을 너무 많이 압축하면 전해질이 구조에 침투할 수 없는 수준으로 다공성이 감소할 수 있습니다. 여기서 품질 관리 요구 사항은 이전 코팅 단계 공정의 요구 사항과 매우 유사합니다. 최종 전극의 두께 편차는 신중하게 관리되어야 합니다. 또한 코팅 단계에서 형성된 불균일성의 결과로 코팅 벗겨짐, 치명적인 손상 및 핀홀과 같은 결함을 검사해야 합니다.
Stil/Marposs 공초점 기술은 이 중요한 공정 단계에서 기하학적 측정 및 검사를 위한 최적의 솔루션을 나타냅니다.
전극의 슬리팅: 레이저 마이크로미터 측정 시스템
슬리팅(Slitting)은 큰 전극 코일(Mother 롤)을 여러 개의 작은 전극 코일(Daughter 롤)로 분할하는 분리 공정입니다.
롤에서 롤로 처리되는 원시 전극의 총 길이는 1000mm보다 큰 폭으로 최대 2000m가 될 수 있습니다. 이 공정에서 요구되는 사항은 매우 연마력이 강한 음극 재료를 세라믹 블레이드로 전극을 절단하기 때문에 다릅니다.
기하학적 측정 데이터는 블레이드 또는 절단할 전극의 잘못된 위치를 식별하는 공정의 중요한 단계입니다. 전극 가장자리의 절단 품질과 코일의 청결도가 주요 품질 기준으로 고려됩니다. 절단된 작은 Daughter 롤의 절단 폭은 셀 설계에 따라 달라질 수 있으며, 많은 애플리케이션 분야에서 60mm와 300mm 사이에 있습니다.
품질 측정 및 비접촉 기술과 같은 인라인 품질관리를 통해 전극 생산의 과도한 스크랩 비율을 줄이기 위해 이 단계의 폭 공정을 모니터링하는 것이 중요합니다.
기존의 접촉식 솔루션으로는 직접 접촉하여 측정할 수 없는 약한 재료에 대해 인라인 폭 측정을 수행하기 위해 마르포스/AEROEL은 자체 레이저 스캔 마이크로미터를 제안합니다.
비접촉식 측정 기능 덕분에 AEROEL 레이저 스캐너를 R2R 산업 공정에 빠르고, 정확하고, 효율적으로 적용할 수 있습니다. 또한 LIB 전극 생산을 위해 레이저 광학 기술을 사용하여 공장에서 일관되고 객관적이며 정확한 결과를 보장합니다. 특허로 보장되는 혁신적인 기술 솔루션을 통해 일반적으로 생산 환경의 측정 결과에 영향을 미치는 온도 변화, 진동, 호일 움직임, 먼지 및 기타 환경 조건에 민감하지 않은 품질 관리 시스템을 실현할 수 있습니다.
전극 분리(Notching) 검사: 머신 비전 솔루션
파우치 셀 제조에는 분리 또는 노칭이 필요하며 양극, 음극 및 분리막 시트를 롤 재료(Daughter 롤)에서 분리하는 방법을 설명합니다. 노칭 공정은 일반적으로 연속 공정에서 전단 절단 (펀칭 도구) 또는 레이저 절단으로 수행됩니다.
이 공정 단계에서 검사해야 하는 가장 중요한 품질 매개변수는 버(Burr) 품질, 절삭날 형상, 외부 금속 이물입자 및 전극 미세 구조의 변형입니다.
마이크로미터 크기의 금속 부스러기는 약한 분리막을 손상시킬 수 있고, 완성된 셀에서 단락을 일으킬 수 있습니다. 따라서, 전극 코팅 밖으로 나오는 결함의 경우 (전류 및 전기장 또는 단락의 영향) 매우 위험합니다. 따라서 전극의 공칭 중심 위치에서 금속박 (알루미늄 또는 구리)의 편차를 확인하는 것이 중요합니다.
Marpos는 특허 출원 중인 인라인 머신 비전 솔루션 덕분에 결함 관리를 해결할 수 있습니다. 시스템은 버, 접힘 및 박리의 존재를 식별하는 전극 프로파일의 품질에서 부정적인 경향을 통계적으로 검사하고 추적할 수 있습니다.
Vision Inspection System에는 전극의 가장자리를 프레임화하고 일련의 디지털 이미지를 획득하는 고해상도 선형 카메라가 있습니다. 이 이미지는 금속 버의 존재 유무를 확인하기 위해 분석됩니다. 이 시스템에는 전극 가장자리와 선형 카메라 사이의 거리 변화를 감지하는 매트릭스 카메라도 포함되어 있습니다. 처리 장치(컨트롤러)는 전극 가장자리와 광학 시스템 사이의 거리 변화에 따라 선형 카메라의 초점을 변경하도록 구성됩니다.
이 시점에서, 이러한 R2R 공정 단계들이 끝나면, LIB 전극들은 셀 조립 공정을 위한 준비가 됩니다. 이 공정에는 적층, 포장, 충전 및 씰링이 포함되며, 이어서 첫 번째 전기 충전이 뒤따릅니다.
LIB 프로세스 개선 분야에서는 주로 전극 제조 및 셀 마무리 기술 혁신이 생산량 증가에 기여하고 있습니다.
마르포스는 또한 다양한 매개변수 모니터링 및 기술을 통해 생산 흐름을 위한 LIB 셀 어셈블리 품질 측정 및 검사 솔루션을 보장할 수 있습니다.
마르포스 그룹은 광범위한 기술과 솔루션을 통해 E-모빌리티 세계에서 품질 및 공정관리에서 주도적인 역할을 하는 것을 목표로 합니다.
자세히 알아보기 Marposs Inline Measurement & Inspection solutions for R2R process