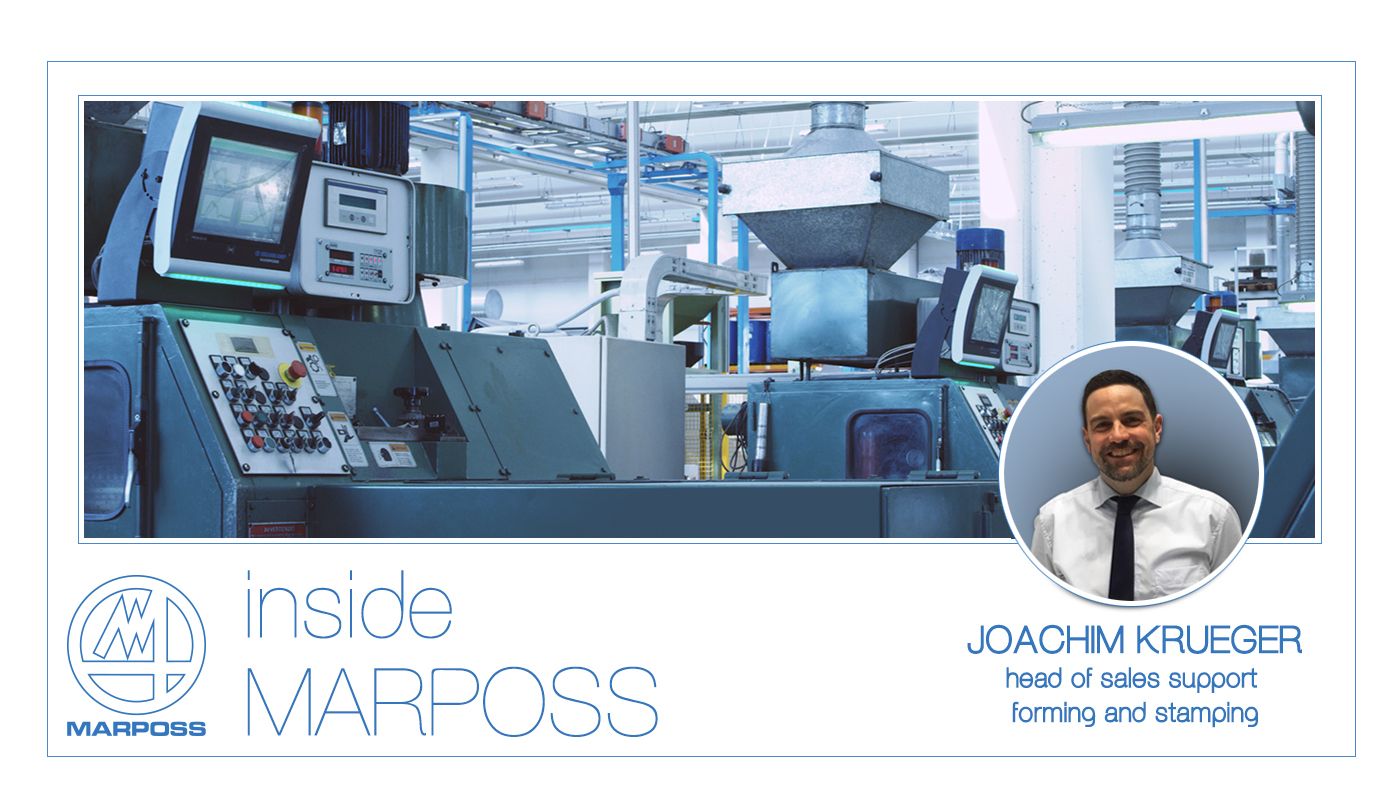
Marposs offers innovative technologies for machine, tool and process monitoring and real time process control - on every type of stamping and forming machines - and provides support for quicker machine set-up.
The Marposs Monitoring Solutions prevent process errors, protect machine and tooling.
Cracks on formed parts represent a typical failure that often occurs randomly in work pieces.
This type of failures are only detected using in-process monitoring on all parts manufactured and various machines in the cold-stamping and forming industry.
The Marposs monitoring systems offer an effective way to observe and control the machine by detecting, right at the deformation stage, part defects or abnormal conditions, to prevent overload or fractures in tool elements.
In case of malfunctions, the systems stop indeed the machine in time to limit costly damages.
As soon as a significant change in the process signal occurs, the machine can be stopped as quickly as possible to prevent expensive machine and tool damage or the defective parts can be sorted out via a sorting gate. Various sorting logics are available for this purpose, as the conditions on the various production machines vary.
Additionally, the signals of sensors are elaborated with algorithms which allow the improvement of machine efficiency and save machining time in setting operation.
Brankamp Marposs systems have become an integral part of the manufacturing operations, they helping our worldwide customers to increase productivity and decrease total life cycle costs of machine tools, moreover provide all relevant production data for data collection systems and are prepared to be integrated into Industry 4.0.
Vario Duo Sensor
In production processes with parts - like hexagon head bolts, collar bolts or nuts - finished pressed parts can be transferred to the next forming stage in the incorrect orientation.
Characteristic "ears" or scrapings occur on, e.g. collar screws with hexagonal heads. Sporadically occurring defects which are often not found during a manual, statistical quality inspection.
During the production of hexagon head screws, so-called turned parts which are not transferred or inserted correctly are always present when pushed into the die.
The defects can range from slight, hardly noticeable scraping to clear quality defects. The forces during part introduction that occur are very low and therefore represent a particularly high requirement for process monitoring.
With the newly developed Vario Duo, this sporadically occurring “rotation or inserting” problem can be identified at the existing measuring position using two sensor elements inside one sensor body and a special software in an additional monitoring channel. The sensor positions prepared by the machine manufacturer can be used without additional preparation.
This means enormous cost savings for the customer, since simple installation is possible.
Vario Duo Sensor Benefits
New monitoring logic allows damaged parts to be sorted out and headers equipped with sorting gates can produce at the best possible speed and process reliability.
- 2nd sensor element for Rotator or Acoustic monitoring
- simple upgrade, no machine preparation necessary
- easy exchange of a standard sensor to Vario Duo
- improved monitoring accuracy
- introduction and transfer / rotation failures detectable
The X-Series System
For the process monitoring for metal forming, we developed the X-Series System, which are high quality in-process monitoring system for nearly all metal forming processes, for example: heading, threading, forging and stamping.
The X-Series system allows the monitoring of different types of machines, different types of sensors and with different types of monitoring modes (Quattromatic, Zoom, Systomatic, Rotator, Binary).
In addition to the multichannel touch display, all systems have various analysis functions: automatic recording of runtimes, set-up and downtimes as well as different counters and storage media, to store all relevant monitoring and production data for different tools or orders.
X3s features and functioning
- up to 12 monitoring channels with automatic calculation of amplification and monitoring window
- 9“ touch display with fast image refresh and high resolution
- various, flexible counter functions: order, tool, dosage, ghost shift, quality counter and many more.
- Stop&Go diagram shows the run-time behavior of the machine in detail
- device protocol records date, time and reason of process failures
- superlux: Multicolored, integrated LED warning lamp
- option: data collection terminal masks ready for FactoryNET® 4.0 and XBrowser
X5s features and functioning
- up to 24 monitoring channels with automatic calculation of amplification and monitoring window
- 12“ touch display with fast image refresh and high resolution
- high resolution signal acquisition (24 Bit A/D conversion)
- various, flexible counter functions: order, tool, dosage, ghost shift, maintenance, shift and stroke
- Stop&Go diagram shows the run-time behavior (up to 90 days) with spm graph device protocol
- records failure curves incl. date, time, stop duration and reason of process failure
- extensive tool and product storage
- option: data collection terminal masks ready for FactoryNET® 4.0 and XBrowser
Marposs guarantees the highest manufacturing quality
Thanks to over 40 years of experience in this industry, our products are highly reliable and easy to handle. Furthermore our own sensor production guarantees highest sensitivity and enables us to ensure the required quality requirements of our products.
Due to the worldwide local service and sales offices, we are able to have contact persons for e.g. regular operator training in the local language at the customer's site.
Our over 50.000 Brankamp Systems installed worldwide are evidence of our competence and dedication.
Discover the Marposs Forming & Stamping Machines