Messelektroniken für Qualitätskontrollen mit Wirbelstrom
E70S - E59N
E70S und E59N sind Wirbelstrom-Kontrollsysteme, mit denen mithilfe berührungsloser Wirbelstromsonden sowohl Prüfungen der Oberflächenqualität auch Werkstoffanalysen durchgeführt werden können. Zerstörungsfreie Prüfungen (NDT), die mit Wirbelstrom (ET) durchgeführt werden, dienen zur Prüfung auf Oberflächenmängel wie Rissen, Poren oder Lufteinschlüsse. Mit diesen Tests wird die Fehlerfreiheit der Wärmebehandlung überprüft und die Materialmischung überwacht, ohne die Teststücke zu beschädigen oder zu verunreinigen.
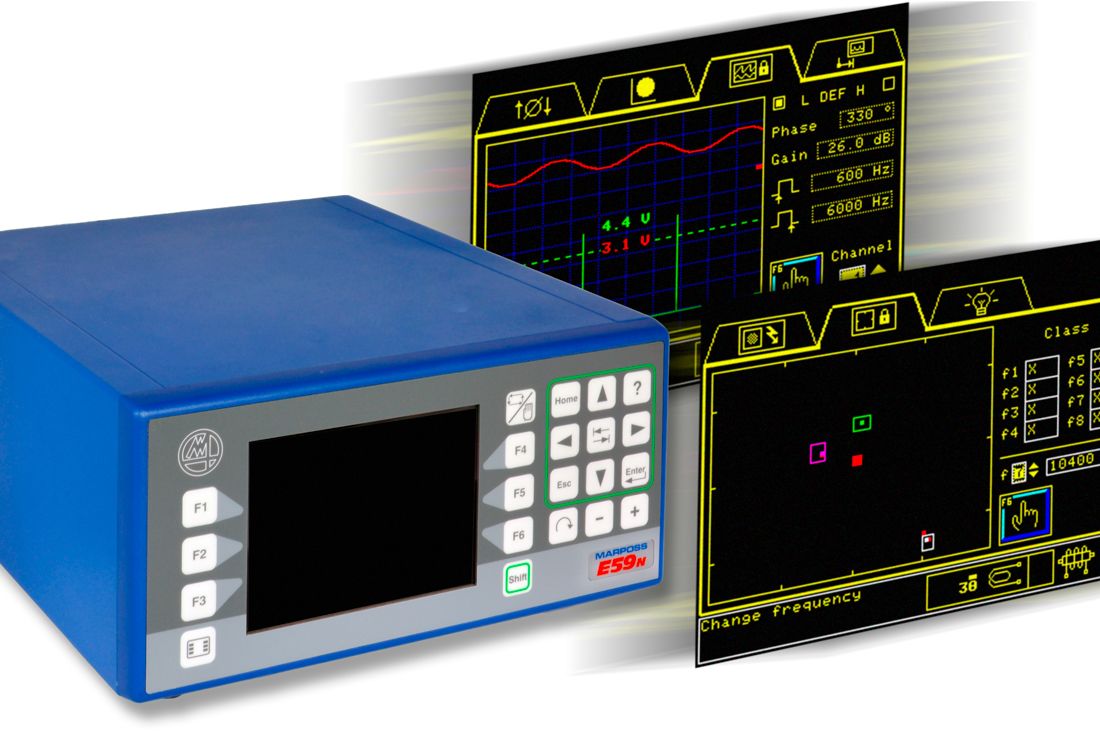
Die Marposs-ZfP-Messelektroniken E70S und E59N arbeiten mit dem Prinzip der Wirbelstromprüfungen. Dabei wird der sogenannte Wirbelstrom, bei dem es sich um kleine Stromschleifen handelt, die durch ein wechselndes Magnetfeld erzeugt werden, am Prüfteil entlang geführt.
Falls Beschädigungen der Oberfläche oder Unterschiede in der Zusammensetzung des Werkstoffs vorliegen, verhält sich der Wirbelstrom anders als normalerweise. Die Änderungen werden von den Wirbelstrom-Messelektroniken E70S und E59N erfasst. Dadurch können Schlechtteile aussortiert werden.
Ein Magnetfeld wird von einer Wirbelstromsonde erzeugt, die so beschaffen ist, dass sie zu jeder Anwendung passt. Das Magnetfeld ist stark genug, um Defekte der Oberfläche oder Werkstoffabweichungen zu erfassen, ohne jedoch die Gefahr zu laufen, dass am geprüften Werkstück ein Restmagnetismus bleibt. Dadurch kann das Werkstück problemlos weiterverarbeitet werden.
Die Messelektroniken E70S und E59N können direkt in die kompletten Marposs-Einrichtungen integriert oder auch als einzelne Komponenten zum Einbau in die Einrichtungen der Kunden erworben werden.
Bei besonders kniffligen Fällen prüft Marposs gerne die Machbarkeit der Prüfung durch Tests mit bereitgestellten Werkstücken und empfiehlt daraufhin die optimale Zusammenstellung aus Messköpfen und Messelektroniken.
Bearbeitungsverfahren wie Drehen, Bohren, Wärmebehandlungen oder Gießen können zu Defekten führen, die ermittelt werden müssen, um den Bruch mechanischer Komponenten zu vermeiden. Wenn solche Defekte nicht erfasst werden, können die betroffenen Komponenten zu einer Gefahr für die Sicherheit der Anwender werden. Um die Qualität jedes einzelnen hergestellten Werkstücks zu garantieren, benötigt man eine zuverlässige Technologie, um 100 % der hergestellten Werkstücke innerhalb der normalen Taktzeiten der Produktion zu überprüfen.
Zerstörungsfreie Prüfverfahren (ZfP - auch ND oder NDT, nach der englischen Bezeichnung) mithilfe von Wirbelstrom erlauben die Prüfung der Werkstoffeigenschaften, ohne dass die Werkstücke vorher vorbereitet werden müssen, zum Beispiel durch Tiefenreinigung oder Entfettung. Die Messelektroniken E70S und E59N, zusammen mit entsprechend konzipierten Wirbelstromsensoren, stellen für Werkstätten die ideale Lösung für folgende automatische Prüfungen an Werkstücken aus der Massenproduktion dar:
- Integrität des Werkstoffs, um Oberflächenbeschädigungen wie Risse, Poren, Lufteinschlüsse usw. zu erfassen
- Werkstoffanalysen, um die Härte der Oberfläche und die Einsatzhärtungstiefe zu überprüfen
- Materialverwechslungsprüfung, um die Vermischung von Werkstoffen bei Werkstücken mit derselben Geometrie, die aber aus verschiedenen Materialien hergestellt werden, zu vermeiden.
Die Wirbelstromtechnik bietet dabei folgende Vorteile:
- Die Werkstücke müssen nicht extra vorbereitet werden
- Die Wirbelstromsonde und das geprüfte Werkstück kommen nicht miteinander in Berührung
- Es können sowohl fest montierte Sensoren als auch Scan-Messköpfe verwendet werden
Die Prüfgeschwindigkeit ist höher als bei jeder anderen ZfP-Technik, daher eignet sich die Wirbelstromprüfung ideal zur automatischen finalen Überprüfung jedes einzelnen Werkstücks einer Produktion.
Von der einfachsten Schraube bis hin zur komplexesten Kurbelwelle: Durch die genau auf die jeweiligen Anforderungen zugeschnittenen automatischen Lösungen und mit über 350 verschiedenen Wirbelstromsonden, die zur Auswahl stehen, kann jedes Prüfproblem gelöst werden.
- 1 bis 12 Prüfkanäle
- Programmierbare Betriebsfrequenz im Bereich von 10 Hz bis 10 MHz
- DSP-Prozessor zur Signalanalyse
- Anzahl der speicherbaren Parametersätze: bis zu 256
- Abstandskompensation Werkstück - Sonde zur Erfassung von Defekten
- Mehrfrequenzmodus (bis zu to 8) zur Prüfung der Werkstoffeigenschaften
- Automatische Einstellfunktion
- Menüführung
- Farbdisplay mit hoher Auflösung
- Grafik-LCD 320x240 pxls, ¼ VGA
- Lokales oder externes Bedienfeld
- Als Einzelgerät oder zum Tafeleinbau erhältlich
- 24 Vdc (-15/+20) % Stromversorgung
- Stromverbrauch: 8 A (max.)
- E-/A-Anschlüsse: Profibus, Profinet oder optoisolierte Ein-/Ausgänge
- BCD-/Binärausgang: 32 (16 Out, 8 In,8 In/Out programmierbar)
- Eigene Hochgeschwindigkeits-I/O
E59N
Wirbelstrom-Messelektronik, am besten für kleinere automatische Anwendungen oder Bänke geeignet, verwaltet bis zu 4 Kanälen mit folgender Konfiguration:
- Bis zu 4 Kanäle für Defektprüfungen (max. 8 Messköpfe mit interner Multiplexer-Funktion)
- Bis zu 4 Kanäle für Härteprüfungen
- 2 Kanäle für Defektprüfungen + 2 Kanäle für Härteprüfungen
E70S
Wirbelstrom-Messelektronik,am besten für komplexere automatische Anwendungen oder Bänke geeignet, verwaltet bis zu 12 Kanäle mit folgender Konfiguration:
- Bis zu 12 Kanäle für Defektprüfungen (max. 24 Messköpfe mit interner Multiplexer-Funktion)
- Bis zu 12 Kanäle für Härteprüfungen
- Eine Kombination für Defekt- und Härteprüfungen, die genau auf die Anforderungen abgestimmt wird
KURBELWELLE
Messmaschine M110 zur Prüfung auf Risse und Porosität an Kurbelwellen
3 E70S-Messelektroniken sind mit 30 ND-Sensoren verbunden, um die fünf Hauptlager, die vier Hublager und den Flansch der Kurbelwelle zu überprüfen.
NOCKENWELLE
Verbrennungsmotoren, Kompressoren und Pumpen sind nur einige der zahlreichen Elemente, bei denen Wellen mit Exzentern verwendet werden, die dazu dienen, andere mechanische Komponenten anzutreiben. Bei den Fertigungsverfahren für diese Teile sowie bei den Wärmebehandlungen und den späteren mechanischen Verarbeitungsprozessen können Oberflächendefekte wie folgende entstehen:
- Porosität
- Risse durch Wärmebehandlungen
- Risse durch mechanische Verarbeitung wie zum Beispiel Drehen und Schleifen
- Hohlräume, Lunker und fehlendes Material aufgrund des Schrumpfens nach dem Gießen
Wenn solche Defekte vorliegen, kann es geschehen, dass die Nockenwelle bei Belastung nicht mehr richtig arbeitet oder gar bricht, was den Betrieb des fertigen Produkts empfindlich beeinträchtigen kann. Daher muss die Oberflächenqualität des Exzenters während der Fertigung der Nockenwelle beziehungsweise des Nockens überprüft werden.
Die komplexe Geometrie der Nocken erforderte früher Prüfverfahren, bei denen entweder eine manuelle Inspektion erfolgte (d.h. eine subjektive Bewertung), oder die Überprüfung mit Techniken, die nur schwer automatisierbar waren, wie etwa Eindringprüfungen mit Flüssigkeiten und/oder Magnetpulver, und die außerdem den Fertigungszyklus verkomplizierten, da die Werkstücke danach gereinigt werden mussten.
Bei der von Marposs entwickelten Lösung wird Wirbelstrom angewendet, der durch die besondere Form der Sensoren die komplette Prüfung der jeweiligen Oberflächen direkt in der Fertigungslinie erlaubt.
Die Messtaster von Marposs sind einzigartig, da kleine Diamanten in den Sensorkörper eingesetzt sind. Dadurch halten die Messköpfe, die an mechanischen Nachlaufsystemen montiert sind, den richtigen Arbeitsabstand von den Werkstücken und folgen dem Profil, um mögliche Risse und Poren zu erfassen.
Die besondere Form der Diamanten und die Kontaktkraft, mit der die Messköpfe auf die Oberfläche der geprüften Werkstücke gedrückt werden, gewährleisten die korrekte mechanische Position der Messköpfe ohne Beschädigung der geprüften Oberfläche.
Bei der Prüfung wird die gesamte Oberfläche mit einer Drehbewegung des Nockens und einer translatorischen Bewegung der Sensoren gescannt, um in einer ausreichend kompakten Spirale die gesamte Nutzfläche des Exzenters zu überprüfen.
Messmaschine M110 zur Prüfung auf Risse und Porosität an Nockenwellen
Zwei E70S-Messelektroniken sind mit 16 ND-Sensoren verbunden, um gleichzeitig zehn Kuppen und sechs Zapfen der Nockenwelle zu kontrollieren. Die Messköpfe scannen die gesamte Oberfläche der Welle.
ZYLINDERBOHRUNG
Bei der Herstellung von Motor-Kurbelgehäusen kann es zu Defekten in den Zylinderbohrungen kommen, zum Beispiel zu Poren (die bei Kurbelgehäusen aus Gusseisen oder Aluminium durch Probleme beim Schmelzen entstehen) und Rissen (aufgrund von Problemen bei der Montage von Stahlrohren in Gehäuse, die hauptsächlich aus Aluminium bestehen).
Solche Defekte gefährden sowohl die Zuverlässigkeit des Motors als auch seine Umweltfreundlichkeit. Wenn sich zu viel Öl in den Oberflächenporen ablagert, steigen schädliche Emissionen und der Motor entspricht nicht mehr den Emissionsvorgaben. Es ist daher von wesentlicher Bedeutung, Schäden der Oberfläche zu ermitteln und Komponenten, die nicht normgerecht sind, aus dem Produktionszyklus zu entfernen.
Diese Arten von Defekten können anhand von Wirbelstromverfahren erfasst werden. Marposs hat dazu spezielle Dreh-Messdorne entwickelt, um die Innenfläche der Zylinderbohrungen zu überprüfen.
Der ND-Messdorn ist mit zwei Wirbelstromsonden ausgestattet (die einander gegenüber liegen), die je nach Taktzeit der Fertigungslinie mit einer Drehzahl zwischen 1000 und 3000 rpm rotieren.
Die Messdorne sind in zwei Versionen erhältlich:
- Nur ZfP mit der Möglichkeit, bis zu drei verschiedene Durchmesser-Abschnitte einzustellen
- Integrierte ZfP mit pneumatischer Dimensionsprüfung
Bei der integrierten ZfP- und Dimensionsprüfungslösung kann die Zylinderbohrung vollständig überprüft werden, das heißt Qualität (Oberflächendefekte) und Geometrie sowie Durchmesser, Ovalität und Konizität mit zwei pneumatischen rechtwinkligen X-Y-Messabschnitten.
Die integrierte Lösung bringt deutliche Vorteile: Die Prüfzeiten sind kürzer und das System ist kleiner und günstiger.
Die Systeme sind vollständig in Fertigungslinien integrierbar. Die Überprüfung des Kurbelgehäuses kann komplett erfolgen, indem man zu den Messdornen für die Zylinderbohrungen einen weiteren Messdorn zur Kontrolle der Achse der Motorwelle hinzufügt. Das Messsystem für Kurbelgehäuse, das sich daraus ergibt, vereint zerstörungsfreie und Dimensionsprüfungen.
Je nach Produktionstakt der Linie wird das System mit einem oder mehreren Messdornen ausgestattet, um alle Kurbelgehäuse Schritt für Schritt oder gleichzeitig zu kontrollieren.
Die mechanische Struktur des Messsystems beinhaltet Messdorne, die an schwimmenden Systemen mit Auflaufsicherung befestigt sind. Dadurch ist gewährleistet, dass sie perfekt in die Zylinderbohrungen eingeführt werden können, auch falls das Kurbelgehäuse kleine Fluchtungsfehler haben sollte.
Außerdem wurde das System konzipiert, um auch die Lage der einzelnen Defekte in der Zylinderbohrung abzubilden. So können Bereiche mit unterschiedlicher Empfindlichkeit definiert werden, wie etwa der Brennraum (wo kleinste Defekte gefunden werden müssen) oder die Gleitfläche.
Messmaschine M125 zur Porositäts- und Dimensionsprüfung in den Zylinderbohrungen des Motorblocks
Die Messelektronik E70s ist für die Porisitätsprüfung der vier Zylinderbohrungen mit den ND-Sensoren verbunden, die am Dreh-Messdorn montiert sind. Die Abtastdauer für die gesamte Innenfläche einer einzelnen Bohrung beträgt 4 - 5 Sekunden. Der Messdorn ist außerdem mit Luftdüsen zur Dimensionsprüfung der Zylinderbohrung ausgestattet. Der Durchmesser wird am Display des elektronischen Messrechners E9066 angezeigt.
NABE
Messmaschine M100 zur Prüfung auf Risse und Poren an Naben
Die Messelektronik E70s ist mit 10 ND-Sensoren verbunden, die gleichzeitig die gesamte Fläche des Werkstücks auf Risse und Poren kontrollieren.
BREMSSCHEIBE
Messeinrichtung M50 zur Prüfung auf Risse und Poren an Naben
Die Messelektronik E70s ist mit 12 ND-Sensoren verbunden, die gleichzeitig die gesamte Fläche des Werkstücks auf Risse und Poren kontrollieren.
KOLBENBOLZEN / WELLEN
Die Anforderung, zerstörungsfreie Prüfungen mithilfe von Wirbelstrom an der gesamten Produktion von Werkstücken mit zylindrischer Geometrie, wie Bolzen, Stoßdämpferrohren, Lagerrollen und weiteren, zu ermöglichen, führte bei Marposs zur Entwicklung des Systems mit rotierenden Messköpfen.
Drehmessköpfe erlauben die Erfassung von Oberflächendefekten an der Außenseite der geprüften Werkstücke durch zwei Wirbelstromsonden, die einander gegenüber liegen.
Das System zur berührungslosen Signalübertragung vermeidet Probleme durch Schleifkontakte und dementsprechend den Bedarf nach Systemwartung.
Die Wirbelstromsonden rotieren extrem schnell (Drehzahlen bis zu 3000 rpm) um das Prüfstück. Dabei tasten sie mit einer spiralförmigen Bewegung, welche die hundertrpozentige Erfassung der Außenfläche gewährleistet, die gesamte Oberfläche ab. Durch die Funktion der automatischen Abstandskompensation sind auch eventuelle Veränderungen des Abstands zwischen der Sonde und dem Werkstück völlig problemlos.
Üblicherweise werden die Werkstücke auf Porosität, Risse und fehlendes Material durch den Fertigungsprozess, die mechanische Verarbeitung und die Wärmebehandlungen geprüft.
Die Rotationsgeschwindigkeit des Messkopfs kann an die Produktionsanforderungen angepasst werden, um Werkstücke in Fertigungslinien mit Werkstück-Transportgeschwindigkeiten bis zu 6 m/min zu kontrollieren. Der Prüfbereich des Durchmessers liegt aktuell zwischen 4 und maximal 70 mm. Die Länge des Werkstücks ist theoretisch unbegrenzt.
Durch die einzigartige Software zur Verarbeitung der Signale der Wirbelstromsonde (AED - Automatic Edge Detection, automatische Randerfassung) ist das System dazu imstande, den Anfang und das Ende des Werkstücks automatisch zu erfassen und den Messvorgang zu starten und zu beenden, ohne dass zusätzliche Sensoren notwendig sind. Die Signalverarbeitung kann auch unterbrochen werden, falls das Werkstück Rillen hat, die von der Prüfung ausgenommen werden sollen.
Die Marposs-Messelektroniken E59N und E70S können die Warteschlange der hergestellten Werkstücke durch die integrierte Schieberegister-Logik eigenständig verwalten und dadurch ein Ausschusssystem in der Linie korrekt betreiben oder die relevanten Informationen an die Steuerungslogik der Maschine weitergeben.
Das System kann direkt hinter der letzten Schleifbearbeitung als Einzeleinrichtung installiert und direkt in eine vorhandene Fördereinrichtung integriert werden. Dadurch wird die Prüfstation besonders kompakt und einfach zu warten.
Das Drehsondensystem kann durch folgende Vorrichtungen ergänzt werden:
- Eine Ausschusseinheit für Schlechtteile
- Ein Prüfsystem für die Güte der Wärmebehandlung mit einem Ringsensor
- Ein Entmagnetisierungssystem vor der zerstörungsfreien Prüfung
Die Einrichtung wurde mit dem Ziel entwickelt, das Problem der Komplettprüfung von Kolbenbolzen / Wellen so nahe wie möglich an der Fertigungslinie zu lösen, ohne dass ein spezielles Handling der Werkstücke nötig ist, um den Platzbedarf und die Kosten niedrig zu halten.
ZERSTÖRUNGSFREIE PRÜFUNG BEIM SPITZENLOSEN SCHLEIFEN
Die immer weiter steigende Nachfrage nach Qualitätskontrollen, die die gesamte Produktion erfassen, erfordert flexible technische Lösungen, die bestmögliche Leistung zu vernünftigen Preisen gewährleisten.
Oberflächendefekte können an der Außenfläche von zylindrischen mechanischen Teilen wie Bolzen, Kolben für Bremssysteme, Stangen von Gasdruck-Stoßdämpfern, Rundstäben, Lenkstangen, Kerzen und ähnlichen erfasst werden. Das geschieht besonders sicher, indem man die zerstörungsfreie Prüfung (ND-Kontrolle) direkt in die spitzenlose Schleifmaschine integriert und die Kontrolle während der Verarbeitung ausführt.
Dabei nutzt man die mechanische Stabilität des Werkstücks, die durch die Schleifvorgänge gewährleistet ist, und die Tatsache, dass die Werkstücke beim Schleifen gedreht und bewegt werden. So kann die ND-Kontrolle zusammen mit der mechanischen Verarbeitung erfolgen. Es sind keine weiteren Stationen innerhalb der Fertigungslinie nötig, was auch die Prüfzeiten optimiert.
Marposs hat ND-Sensoren mit verschiedenen Formen und Größen entwickelt, die mit Wirbelstrom funktionieren. Sie können direkt in die mechanischen Aufnahmen eingesetzt werden, in denen die Werkstücke während des Schleifverfahrens transportiert werden.
Die Materialien und Technologien, die bei den Wirbelstromsensoren verwendet werden, sind in die Sensoren selbst integriert. Dadurch sind sie völlig undurchlässig und können auch unter härtesten Umgebungsbedingungen eingesetzt werden. Außerdem können sie verwendet werden, um Oberflächendefekte an der Außenseite wie kleinste Risse, Poren und Lufteinschlüsse zu erfassen.
Für Kontrollen an spitzenlosen Schleifmaschinen wurden spezielle Software-Funktionen entwickelt. Die elektronischen Einrichtungen sind dazu imstande, das Messverfahren automatisch zu starten und zu stoppen, während die Werkstücke durchlaufen, ohne dass zusätzliche externe Sensoren wie induktive oder mechanische Mikroschalter eingesetzt werden müssen.
Die Wirbelstromsonden erkennen den Anfang des jeweiligen Werkstücks von alleine, so dass die ND-Kontrolle wenige Millimeter hinter dem Rand des Werkstücks beginnen kann und bis zum anderen Ende des Werkstücks aktiviert bleibt.
Außerdem ist es möglich, mithilfe der Software-Vorgaben bestimmte Abschnitte der Oberfläche automatisch von der Kontrolle auszuschließen, wenn diese keine besondere Bedeutung für die Funktion haben und somit Oberflächendefekte haben dürfen.
Die Einstellung des Kontrollzyklus anhand von Parametern stellt sicher, dass das Prüfsystem ganz einfach an Werkstückwechsel angepasst werden kann, sogar wenn Längs- oder Querrillen vorliegen.
Das System ist dazu imstande, eine Warteschlange hergestellter Werkstücke zu verwalten. Wenn ein Werkstück als defekt erfasst wird, speichert die Elektronik die entsprechende Information. Danach wird das Werkstück durch die integrierte Steuerungslogik zu der Station transportiert, in der eine mechanische Ausschussvorrichtung Schlechtteile aus der Fertigungslinie aussondert.
ZERSTÖRUNGSFREIE PRÜFUNG VON NOCKENKUPPEN
ZERSTÖRUNGSFREIE PRÜFUNG VON ZYLINDERBOHRUNGEN
PROSPEKTE UND HANDBÜCHER
Prospekt | |
---|---|
Englisch |
E59N: (236.14kB)
E70S: (221.17kB) |
Italienisch |
E59N: (310.87kB)
E70S: (374.82kB) |
Deutsch |
E59N: (315.03kB)
E70S: (228.39kB) |
Französisch |
E59N: (273.10kB)
E70S: (230.53kB) |
Tschechisch |
E59N: (319.05kB)
E70S: (400.85kB) |
Japanisch |
E70S: (666.52kB)
E59N: (587.31kB) |