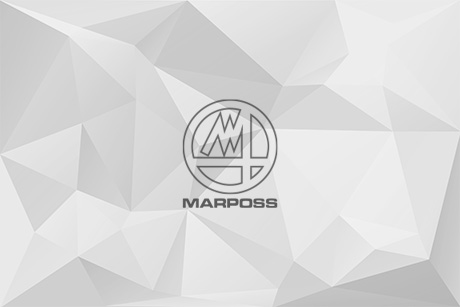
The most common acoustic emission sensors monitoring systems are used to detect contact between wheel and a workpiece or dresser and to prevent catastrophic mistakes, but acoustic sensors have a wide range of other capabilities. By combining multisensor inputs with sophisticated analytical algorithms, today's systems provide new opportunities for a more completed working and dressing processes monitoring.
In particular about grinding situations such as dressing of CBN wheels, Marposs P7 system detects vibration at the exact moment of contact between dressing tool and grinding wheel guarantees an high accuracy positioning.
As the dressing tool travels across the wheel surface, Marposs P7 units establish an acoustical pattern based on the duration of contact. A wheel in good condition emits a steady, continuous signal, and damaged areas on the wheel surface will produce gaps or an interrupted emission, meaning further dressing is necessary. Also, duration of contact sound during wheel dressing can indicated the exact moment to stop, minimising the loss of abrasive material.
With sensors mounted directly to the top surface of the dressing tool or internally within dressing spindle Marposs P7 allows an high degree of sensitivity. During wheel dressing or truing, this sensitivity permits "to hear" that less than half micron (0,5 µm) amount of wheel surface is being removed by the dresser.
Experiences attribute these favourable results to the wide frequency range of Marposs AE sensors and P7 ability to acquire a background noise level prior the dressing, making it easier to isolate signal from noise.
Now Marposs P7 ability has been improved add new sophisticated analytical algorithms called "Dynamic Thresholds" (time variable limits), capable to control the grinding process or shaped CBN wheels along their entire width, to be dressed to a proper geometry.
The Acoustic Emission monitoring actives during all grinding operations can indicate that the working and dressing processes are out of defined parameters for an optimal process. These monitoring prevents burns, bad geometry of the ground workpieces, bearings wear or machine down time and more expensive machine damages.