Battery Module Electrical Test Systems
Marposs has combined its measurement experience and skills in automating complex systems into the development of battery module testing systems for electro-mobility applications. These solutions are capable of testing functionality, performance and electrical safety characteristics, as well as the logic management system.
These systems are available as semi-automatic solutions, where an operator manually joins the electrical connector to the battery module, or as fully automated applications where both the handling of the modules and the contact take place without human intervention.
These machines are used for the end-of-line test (Module EoL test) in the production of battery modules, as well as for beginning-of-line test (Pack BoL test), with possible Xion in classes, in the pack assembly lines.
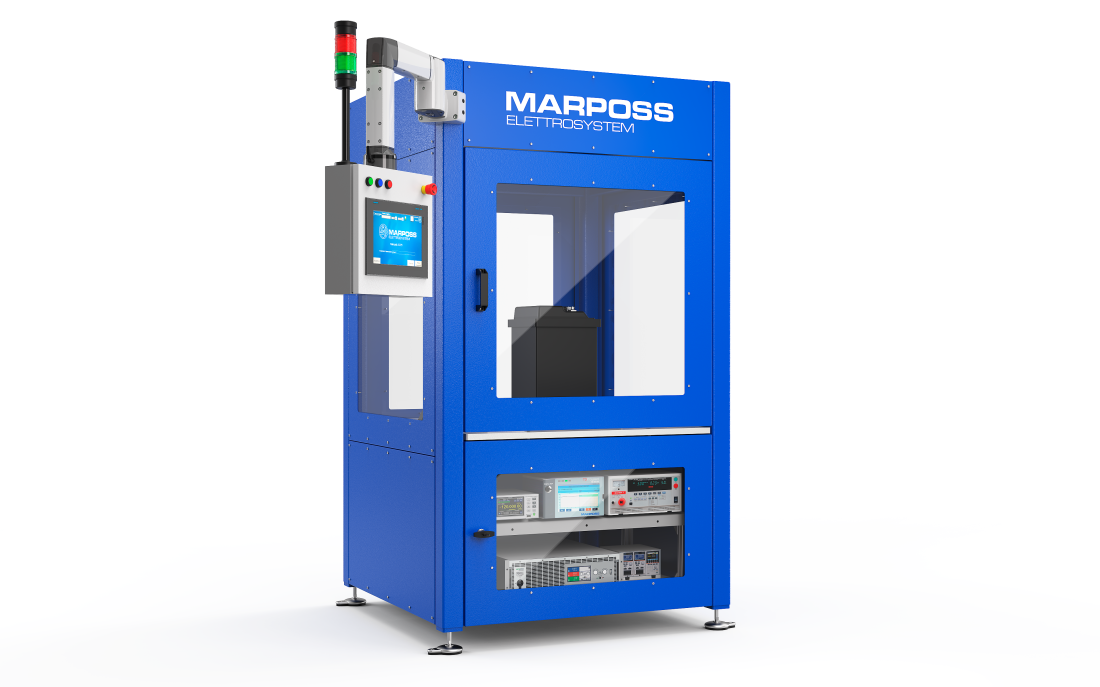
Example of a Semi—Automated Battery Module Test Bench.
This very compact solution is designed for use as a stand-alone test station with manual loading or potentially assisted with mechanical aids. The connection and disconnection of the battery module to the test system is performed by the operator, with safety checks incorporated during the connecting of the electrical circuit. Additional safety measures include constant monitoring with a thermal camera of the battery module temperature when subjected to electrical operating load, and a fire prevention system connected to the factory network.
The test system features robust connectors, designed to withstand up to 100,000 operating cycles.
The electrical tests performed on the battery module include:
- Insulation measurement and electrical rigidity test
- Electrical continuity test
- OCV control and comparison with internal measurement
- ACIR and DCIR control, possible pulse power test
- Functional check of the CMC or BMS
- HVIL safety functionality check
- Check of OCV homogeneity of the cells in the module and their temperature
- Verification of the SOH and internal logic of the CMC
- Measurement of module capacity (statistical check)
- E9066 PC integrability for statistical control and control charts
This type of configuration is particularly suitable for use in pilot lines or in production lines for medium-low volumes. Pneumatic or helium leak testing of the module cooling circuit can also be integrated with the electrical test.
For mass production, Marposs offers various fully automated solutions.
- Architecture based on industrial PLC hardware particularly robust and flexible
- Calibration and certification procedures for each electrical measurement
- High degree of adaptability to any module shape and connector position
- Solution designed for manual or automatic part loading
- Wide range of electrical tests available and freely configurable by the customer
- Xivity of the active test
- Energy recovery on the electricity grid in the module discharge phase
- Recovery of thermal energy dissipated by fluid for the benefit of the plant's winter air conditioning
- Data logging for Industry 4.0 compliance
- Possible applications for the classification and Xive assembly of modules in the package
- Compact solution
- Minimum maintenance
- Manual part loading
- Automatic part loading
- Manual connection of power and signal cables
- Automatic connection of power and signal cables
Dimensions (HxWxD) | 2000 x 800 x 800 mm |
Efficiency | 98% |
Cycle time | depends on the pulse power cycle (from 3 minutes to 30 minutes) |
Min / Max power range of the module | 1kW / 18kW |
Maximum test power |
800V, 90A |