AIR LEAK TEST BENCH FOR E-MOTOR
Leak testing of the EDU case is important to ensure the tightness of the compartment that houses the stator and, where present, the compartment that houses the inverter, as well as the tightness of the cooling circuit that typically 'wraps' around the stator housing and in some cases also passes through the inverter compartment.
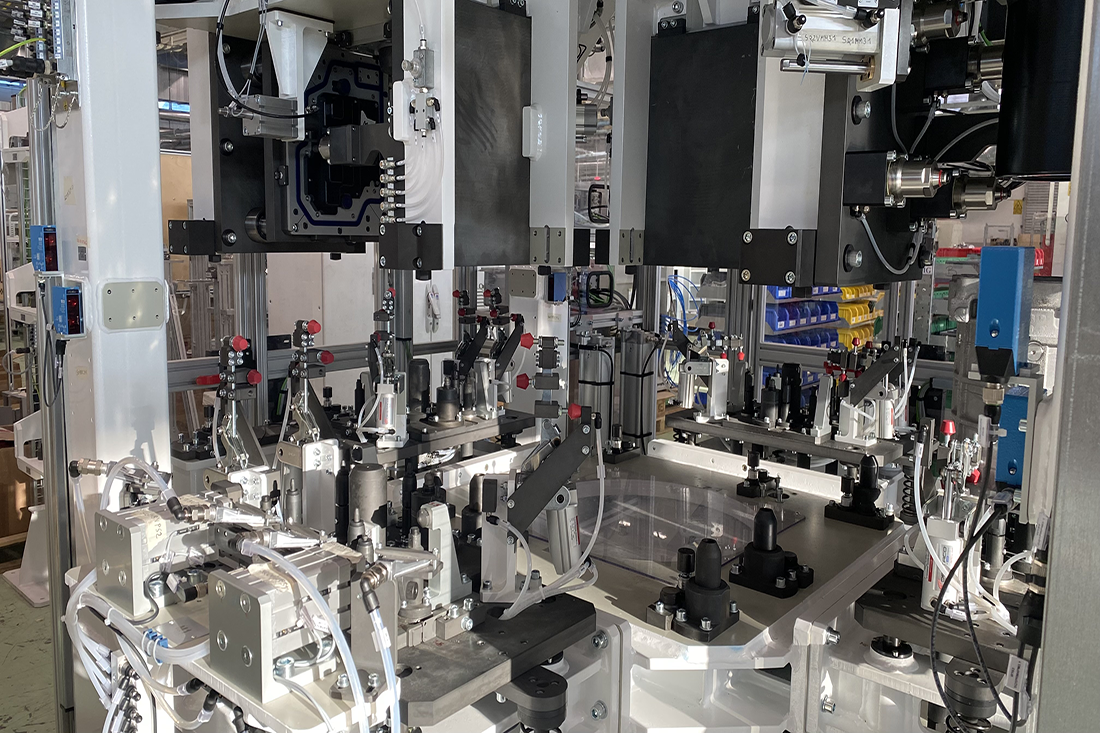
The leak test, when performed on blanks, typically aluminium castings, allows any porosity and defects in the part to be identified before more costly machining is undertaken. The figure below shows an example of a raw part application where the cooling circuit, inverter compartment and stator housing are tested at different stations.
After the machining phase, it is usually necessary to proceed with the assembly of some technological plugs (cup plugs, thread plugs, spheres or sealing rivets) required to close any machining holes, rather than core support holes, during the casting process.
Once the plugs have been fitted, it is necessary to carry out a leak test on the plugs alone or on the entire circuit to which the plugs have been fitted.
Having a single supplier for both the connector assembly machine and the subsequent leak test offers the end customer the advantage of having a single point of contact for these two essential operations to guarantee the quality and functionality of the finished part.
For this reason, we offer our customers both applications (assembly and leak testing) either as separate solutions or integrated in an automated cell.
- Robotised island for ball seating and leak testing
- Automatic robotised cork screwing units
- Cork stopper leak testing station
- Leakage test up to 5 bar
- Possibility to perform crossover tests between circuits
- Cycle time from 25 to 60 sec
Robotic island for ball press-fitting and leakage test:
- Ball press-fitting with electromechanical or hydraulic presses up to 50KN
- Possibility to integrate cycles for checking the correct functioning of the presses
- Cycle time from 25 to 60 sec
Automatic groups for screwing caps serviced by a robot:
- Possibility of managing cycles with multiple or single screwdriving
- Possibility of integrating cycles to check the correct functioning of the screwdriving
- Cycle time from 25 to 60 sec
Cap tightness test station:
- Leak test in air up to 5 bar
- Possibility of testing caps individually or in a single cycle
- Cycle time from 20 to 45 sec
- Manufactured to customer specification
- Dedicated or flexible solutions
- Solid construction
- Easy to maintain with easily accessible components
- Support in your country with technicians who speak your language
- Excellent pre- and after-sales support team