Central Electrónica para Control de Calidad mediante Corrientes de Foucault
E70S - E59N
E70S y E59N son sistemas de corriente parásita diseñados para comprobar tanto la calidad de la superficie como las características del material usando sondas de de corriente parásita sin contacto. Pruebas no destructivas (NDT) con corriente parásita (ET) se usan para comprobar los defectos superficiales como grietas, poros o burbujas. Esto se realiza para comprobar la precisión del tratamiento de calor y efectuar una monitorización de la mezcla de materiales, sin dañar ni contaminar las muestras probadas.
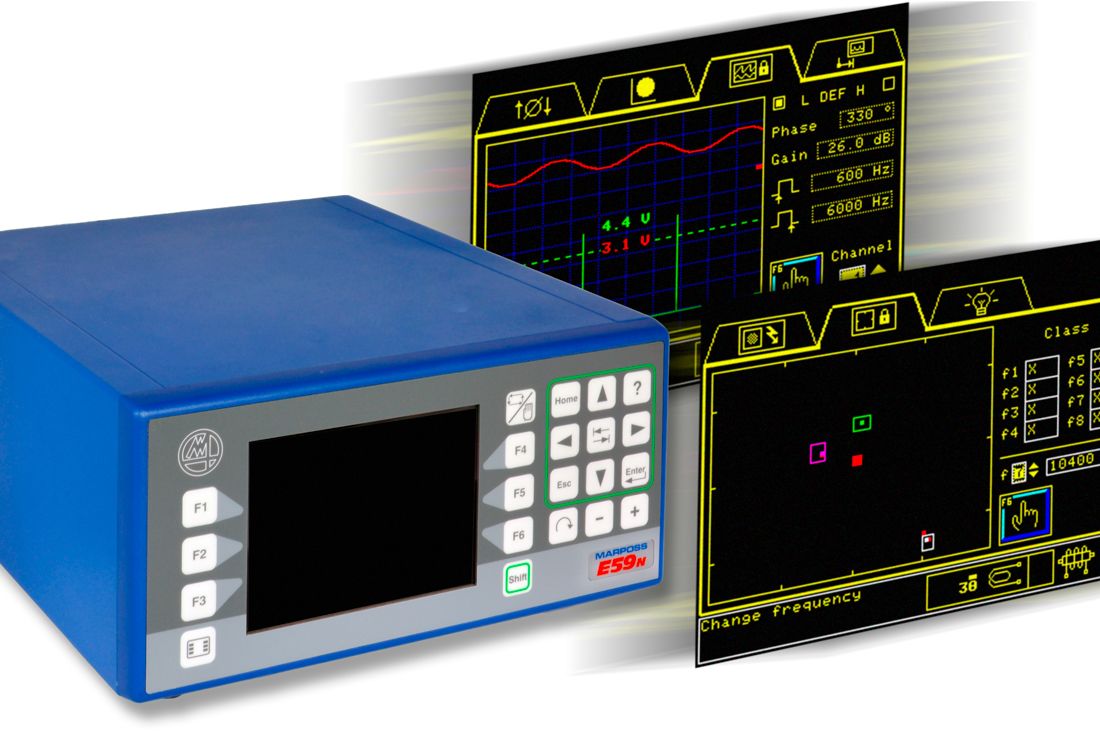
Las pruebas no destructivas electrónicas (NDT, por sus siglas en inglés) realizadas por los dispositivos E70S y E59N de Marposs se basan el principio de funcionamiento de la corriente parásita, esta técnica genera en la pieza que se está probando la llamada «corriente parásita», que son pequeños bucles de corriente eléctrica inducidos por un campo magnético que varía con el tiempo.
La presencia de defectos o diferencias superficiales en la composición del material provocará un cambio en el comportamiento normal de la corriente parásita. Estos cambios debidos a las corrientes parásitas son detectados en los dispositivos electrónicos E70S y E59N para diferenciar las piezas correctas de las defectuosas.
Se genera un campo magnético con una sonda de corriente parásita, adecuadamente diseñada para resolver los problemas de aplicación. La fuerza del campo magnético es suficiente para detectar defectos superficiales o desviaciones del material sin riesgo de dejar una magnetización residual en la pieza probada, de manera que puede completar el proceso de producción.
Las centrales electrónicas E70S y E59N pueden utilizarse como parte de las aplicaciones llaves en mano de Marposs o como componentes que pueden integrarse en las aplicaciones del cliente.
En caso de problemas aplicativos dudosos, Marposs puede examinar la viabilidad de la comprobación realizando pruebas en las piezas sugeridas por el cliente y sugiriendo una combinación adecuada de sensores y electrónica.
Los procesos de mecanizado como torneado, rectificación, taladrado, tratamientos térmicos o de fusión pueden generar defectos que deben ser detectados para evitar la rotura de los componentes mecánicos; si no se detectan, estos componentes pueden poner en peligro la seguridad del usuario. La certificación de calidad de todas las piezas fabricadas prueba que es fundamental tener una tecnología fiable que revisa el 100% de las piezas fabricadas con índices típicos en la línea de producción.
Las pruebas no destructivas (NDT) basadas en corriente parásita permiten probar las propiedades de los materiales sin necesidad de preparar la pieza, por ejemplo con una limpieza a fondo o un desengrasado. E70S y E59N, en combinación con sensores de corriente parásita adecuadamente diseñados, ofrecen una solución en el taller para los sistemas de inspección automáticos de componentes de producción en masa que se deban comprobar:
- integridad el material para detectar defectos superficiales como grietas, porosidad, burbujas, etc.;
- propiedades de material para comprobar la dureza superficial y la profundidad de la carcasa;
- identificación del material para evitar mezclas de materiales de las piezas que tienen la misma geometría pero están realizadas con diferentes materiales.
Gracias a las siguientes ventajas de la tecnología de corriente parásita:
- No es necesaria la preparación de la pieza
- no hay contacto entre la sonda de corriente parásita y la pieza inspeccionada
- posibilidad de usar tanto sondas fijas como de exploración
Es posible una velocidad de test más elevada que con otras técnicas NDT, lo que lo hace útil para realizar las pruebas automáticamente en el 100% de la producción, como inspección final.
Desde el tornillo más simple al cigüeñal más complejo, con soluciones automáticas realizadas a medida y más de 350 sondas de corriente parásita en cartera, puede resolverse cualquier problema de inspección específico.
- De 1 a 12 canales de prueba
- frecuencia de funcionamiento programable con un intervalo de 10Hz a 10MHz
- procesador de señales digitales DSP para el análisis de la señal
- número de parámetros fijados en la memoria: hasta 256
- compensación de la distancia de la pieza a la sonda para detectar los defectos
- modo multifrecuencia (hasta 8) para la inspección de las propiedades del material
- función de configuración automática
- menús guiados
- pantalla de color de alta definición
- LCD gráfico 320x240 píxeles, ¼ VGA
- panel del operador local o remoto
- configuración independiente o montada en panel disponibles
- alimentación de potencia de 24 Vdc (-15/+20) %
- consumo de potencia 8 A (max)
- conexión I/O: profibus, profinet o I/O optoaislada
- BCD/Binario: 32 (16 out, 8 in, 8 in/out programable)
- I/O específica de elevada velocidad
E59N
Electrónica de corriente parásita, adecuada para aplicaciones automáticas pequeñas o bancos, gestiona hasta 4 canales con las siguientes configuraciones:
- Hasta 4 canales para la inspección de defectos (máximo 8 sondas con función multiplexor interna)
- hasta 4 canales para inspección de dureza
- 2 canales para inspección de defectos + 2 canales para la inspección de dureza
E70S
Electrónica de corriente parásita, adecuada para aplicaciones automáticas pequeñas o bancos, gestiona hasta 12 canales con las siguientes configuraciones:
- Hasta 12 canales para la inspección de defectos (máximo 24 sondas con función multiplexor interna)
- hasta 12 canales para inspección de dureza
- una combinación de inspección de defecto y dureza según requiere la aplicación
CIGÜEÑAL
M110 máquina para las pruebas de grietas y porosidad en el cigüeñal
Se han conectado 3 unidades E70S electrónicas a 30 sensores ND para comprobar los cinco cojinetes principales, cuatro cojinetes de la muñequilla, y la brida del cigüeñal.
ÁRBOL DE LEVAS
Motores de combustión interna, compresores y las bombas son algunos de los muchos componentes que usan ejes con levas excéntricas diseñadas para desplazar otros componentes mecánicos. Los procesos de producción de estas piezas, así como los tratamientos térmicos y los posteriores procesos de mecanizado mecánicos, pueden provocar la formación de defectos de superficie, como:
- Porosidad
- Grietas provocadas por tratamientos térmicos
- Grietas provocadas por mecanizado mecánico, como por ejemplo, torneado y rectificación
- Cavidades y material no presente provocados por contracciones por fundición
La presencia de los defectos antes mencionados pueden provocar el fallo del árbol de levas bajo esfuerzos, poniendo en peligro el funcionamiento correcto del producto acabado. Por lo tanto, debe comprobarse la calidad de la superficie del excéntrico durante el proceso de producción del árbol de levas individual o de la leva individual.
La geometría compleja de las levas tradicionalmente hacen necesario el uso de los procedimientos de prueba que consisten bien en una inspección manual (sujeta a la influencia del operador) o pruebas con tecnologías que es difícil automatizar, como líquidos penetrantes y/o polvo magnético, que requieren una gestión complicada del ciclo de la pieza en términos de limpieza.
La solución diseñada por Marposs utiliza corrientes parásitas que, gracias a un diseño especial de los sensores, permiten la inspección de las superficies afectadas que debe realizarse directamente en las líneas de producción para una inspección al 100%.
La unicidad de las sondas Marposs reside en la presencia de pequeños diamantes fijados en el cuerpo de los sensores que permiten que las sondas, montadas en seguidores mecánicos, mantengan una distancia operativa correcta respecto a la pieza, siguiendo el perfil de la misma para identificar grietas y porosidad.
La forma especial de los diamantes y la fuerza de contacto con la que se aprietan los sensores en la superficie de las piezas que se están probando garantizan un posicionamiento mecánico correcto sin dañar la superficie que se está inspeccionando.
La inspección consiste en la exploración de toda la superficie con un movimiento giratorio de la leva y un movimiento de traslación de los sensores para comprobar con una espiral suficientemente compacta, toda la superficie útil del excéntrico.
Máquina M110 para prueba de grieta y porosidad en el árbol de levas
Se conectan dos E70s a 16 sensores ND para la comprobación simultánea de diez lóbulos y seis muñones del árbol de levas. Los sensores exploran toda la superficie del eje.
ORIFICIO DEL CILINDRO
Los procesos de seguimiento de los cárteres del motor pueden llevar a la formación dentro de los orificios del cilindro de defectos, como porosidad (provocada por la fusión en cárter de hierro colado y aluminio) y grietas (después de problemas en el montaje de orificios de acero sobre todo el cárter de aluminio).
La presencia de estos defectos pone en peligro tanto la fiabilidad del motor como su rendimiento en términos de contaminación. Un exceso de aceite situado en la porosidad de la superficie aumenta las emisiones contaminantes en la atmósfera, y hace que el motor no respete las normas relativas a las emisiones. Por lo tanto, identificar los defectos de la superficie reviste una importancia fundamental para eliminar los componentes que no respetan la normativa del ciclo de producción.
Estos tipos de defectos pueden identificarse con tecnología de corriente parásita y un tampón giratorio diseñado específicamente por Marposs para revisar la superficie interior de los orificios del cilindro.
El tampón ND incorpora dos sondas de corriente parásita (una delante de la otra) que giran a una velocidad entre 1000 y 3000 RPM, basándose en el tiempo de ciclo de la línea.
El tampón está disponible en dos versiones:
- Solo prueba ND con la posibilidad de hasta tres secciones de diámetros diferentes
- Prueba ND integrada con prueba de dimensiones neumáticas
La solución ND y la solución dimensional permiten realizar una prueba completa del orificio del cilindro en términos de calidad (presencia de defectos de superficie) y geometría, y controla el diámetro, ovalidad y conicidad con dos secciones de medida neumáticas en los ángulos derechos X-Y.
La solución integrada ofrece unas ventajas claras y reduce los tiempos de prueba, el tamaño y los costes de la aplicación.
Las aplicaciones pueden integrarse completamente en las líneas de producción, completando la revisión del cárter y añadiendo los tampones para los orificios del cilindro, un tampón para revisar el eje del transmisión del motor. La inspección final del cárter resultante integra las pruebas ND y dimensionales.
Basándose en el índice de producción de la línea, la máquina se diseñará con uno o más tampones para probar todos los cilindros del cárter en pasos o simultáneamente.
La estructura mecánica de la aplicación incorpora tampones acoplados en sistemas flotantes y retráctiles que garantizan una perfecta introducción en los orificios del cilindro, incluso si hay pequeños errores de alineación en el cárter.
El sistema también ha sido desarrollado para mapear la posición del defecto individual dentro del orificio del cilindro para definir áreas con diferentes sensibilidades, como por ejemplo la cámara de combustión (donde deben identificarse los defectos pequeños) o el plano de deslizamiento
Máquina M125 para pruebas de porosidad e inspección dimensional en los orificios del cilindro del bloque motor
La unidad electrónica E70S está conectada a los sensores ND montados en el tampón giratorio para la prueba de porosidad de los orificios de cuatro cilindros. El tiempo de exploración para toda la superficie interior de un orificio individual es de 4-5 segundos. El tampón también está equipado con boquillas de aire para la inspección dimensional del orificio del cilindro. El tamaño del diámetro se muestra en la unidad electrónica E9066.
CUBOS
Máquina M100 para test de grietas y porosidad en cubos
La unidad electrónica E70s se puede conectar a 10 sensores ND que exploran simultáneamente toda la superficie de la pieza para comprobar si hay grietas y porosidades.
FRENO DE DISCO
Banco M50 para prueba de grietas y porosidad en cubos
La unidad electrónica E70s se conecta a 12 sensores ND que exploran simultáneamente toda la superficie de la pieza para comprobar si hay grietas y porosidades.
PASADOR DEL PISTÓN / EJES
La necesidad de realizar pruebas no destructivas con corrientes parásitas en el 100% de la producción de piezas con geometría cilíndrica, como pasadores, varillas de los amortiguadores, rodillos de cojinetes, etc., han llevado al desarrollo por parte de Marposs de un sistema de sonda giratoria.
La sonda giratoria permite identificar los defectos de la superficie en la parte exterior de las piezas probadas con dos sondas de corriente parásita una delante de otra.
El sistema de transmisión de señal sin contacto elimina el problema de los contactos deslizantes y la consiguiente necesidad de mantenimiento del sistema.
Las sondas de corriente parásita giran a velocidades elevadas (hasta 3000 RPM) alrededor de la pieza que se está revisando, explorando toda la superficie con un movimiento helicoidal que garantiza la prueba del 100% de la parte exterior. Los cambios en la distancia sonda-pieza no suponen un problema gracias a la función de compensación de distancia automática.
Los defectos típicos de las piezas comprobadas son porosidad, grietas y faltas de material provocadas por el proceso de producción, mecanizado mecánico y tratamientos térmicos.
La velocidad de rotación de la sonda puede adaptarse a los requisitos de producción para inspeccionar piezas en las líneas de producción con velocidad de transferencia de piezas de hasta un máximo de 6 m/min. El intervalo de inspección del diámetro actualmente cambia de un mínimo de 4 a un máximo de 70 mm. La longitud de la pieza es virtualmente ilimitada.
Gracias al software de procesamiento único de la señal de la sonda de corriente parásita (AED, Detección automática de borde) el sistema puede detectar automáticamente el principio y el final de la pieza, y habilita y deshabilita la medida sin necesidad de recurrir a sensores externos adicionales. También puede suspenderse el procesamiento si la pieza tiene ranuras que deben excluirse de la inspección.
Las unidades electrónicas E59N o E70S de Marposs puede gestionar de manera independiente la cola de las piezas producidas con la lógica integrada de registro de desplazamiento, que realiza correctamente un sistema de separación de las piezas descartadas en la línea y envía la información a la lógica de la máquina.
El sistema puede instalarse directamente después de la última operación de rectificación como unidad autónoma e integrarse directamente en el transportador existente, haciendo que la estación de inspección sea extremadamente compacta y fácil de mantener.
El sistema de sonda giratorio puede integrarse con las siguientes opciones:
- Una unidad de expulsión para las piezas descartadas
- un sistema de inspección para un tratamiento térmico correcto con un detector de anillo
- un sistema de desmagnetización antes de la prueba N.D.
El equipo ha sido diseñado para resolver el problema del la inspección al 100% de los pasadores de pistón o ejes lo más cerca posible de la línea de producción sin necesidad de gestionar una pieza de elaboración especial para mantener lo más bajos posibles el espacio y el coste.
CONTROLES NO DESTRUCTIVOS EN LA RECTIFICACIÓN SIN CENTROS
La demanda cada vez mayor de un control de calidad que cubra el 100% de la producción requiere soluciones técnicas flexibles que puedan garantizar el máximo rendimiento posible con unos costes razonables.
Los defectos de la superficie pueden identificarse en la parte exterior de las piezas mecánicas cilíndricas como pasadores, pistones para sistemas de frenado, vástagos de amortiguadores de gas, barras cilíndricas, varillas de dirección, tampones, y otros. Esta operación se realiza de una manera original y segura integrando el control ND directamente en la rectificación sin centro y realizando la prueba durante el ciclo de mecanizado.
Se aprovecha la estabilidad mecánica de las piezas, garantizada por las operaciones de rectificación, y el hecho que son giradas y desplazadas por la rectificación. El control ND puede realizarse junto con el mecanizado mecánico. Se realiza sin necesidad de estaciones adicionales en la línea de producción existente y por lo tanto, se optimizan los tiempos de control.
Marposs ha desarrollado sensores ND con tecnología de corriente parásita con diferentes formas y tamaños que pueden acoplarse directamente en la referencia mecánica que guía las piezas durante el tránsito dentro del proceso de rectificación.
Los materiales y las tecnologías utilizados para los sensores de corriente parásita se integran en los sensores, lo que garantiza una impermeabilidad completa para que puedan soportar los entornos más duros. También pueden usarse para detectar defectos de superficie en el parte exterior como microgrietas, porosidad y burbujas.
Se han diseñado específicamente funciones SW especiales para controles en máquinas rectificadoras sin centro. El equipo electrónico puede habilitar y deshabilitar automáticamente la medida durante el paso de las piezas, sin sensores externos adicionales, como micros inductivos o mecánicos.
La sonda de corriente parásita identifica el inicio de la pieza de manera independiente, de manera que el control ND puede habilitarse a unos milímetros respecto el borde de la pieza. Esto se realiza mientras se sujeta el extremo opuesto de la pieza.
Las especificaciones SW también permiten la exclusión automática para las secciones de la superficie no implicadas desde un punto de vista funcional y que pueden tolerar los defectos de superficie.
La parametrización del ciclo de control asegura que el sistema de control puede adaptarse fácilmente a cambios de las piezas incluso en presencia de ranuras, bien sean axiales o transversales.
El sistema puede gestionar una cola de piezas producidas. Si se detecta una pieza defectuosa, la unidad electrónica guarda la información. Entonces, mediante la lógica integrada, transfiere la pieza a la estación donde el dispositivo de expulsión mecánico empujará la pieza descartada fuera de la línea.
ENSAYOS NO DESTRUCTIVOS DE RESALTES DE LEVA
ENSAYOS NO DESTRUCTIVOS DE ORIFICIOS DEL CILINDRO
BROCHURES AND MANUALS
Catálogo | |
---|---|
Inglés |
E70S: (221.17kB)
E59N: (236.14kB) |
Italiano |
E70S: (374.82kB)
E59N: (310.87kB) |
Alemán |
E70S: (228.39kB)
E59N: (315.03kB) |
Francés |
E70S: (230.53kB)
E59N: (273.10kB) |
Checo |
E70S: (400.85kB)
E59N: (319.05kB) |
Japonés |
E59N: (587.31kB)
E70S: (666.52kB) |