Medición E Inspección De Horquilla En El Área Decapada
Varias investigaciones han mostrado que existen unas ventajas significativas en el uso de bobinados de horquilla de cable plano en algunos tipos de motores. Las ventajas es un factor de relleno de cobre de la ranura mucho mayor, lo que reduce y mejora el par y la densidad de potencia, que en última instancia puede reducir el tamaño del motor en la aplicación EV.
Sin embargo, para obtener una mejora en el rendimiento, es necesario garantizar un nivel de calidad adecuado del componente y que el proceso de producción está perfectamente bajo control.
Uno de los aspectos más críticos en la producción de horquillas afecta al proceso de decapado y el control de una eliminación perfecta del esmalte de aislamiento de los terminales antes de la soldadura. De hecho, la combustión de los restos de esmalte u otros contaminantes durante la fase de soldadura puede generar inclusiones de gas y cavidades en la junta de soldadura, lo que provoca una reducción en la resistencia mecánica de la junta y un aumento de la resistencia eléctrica.
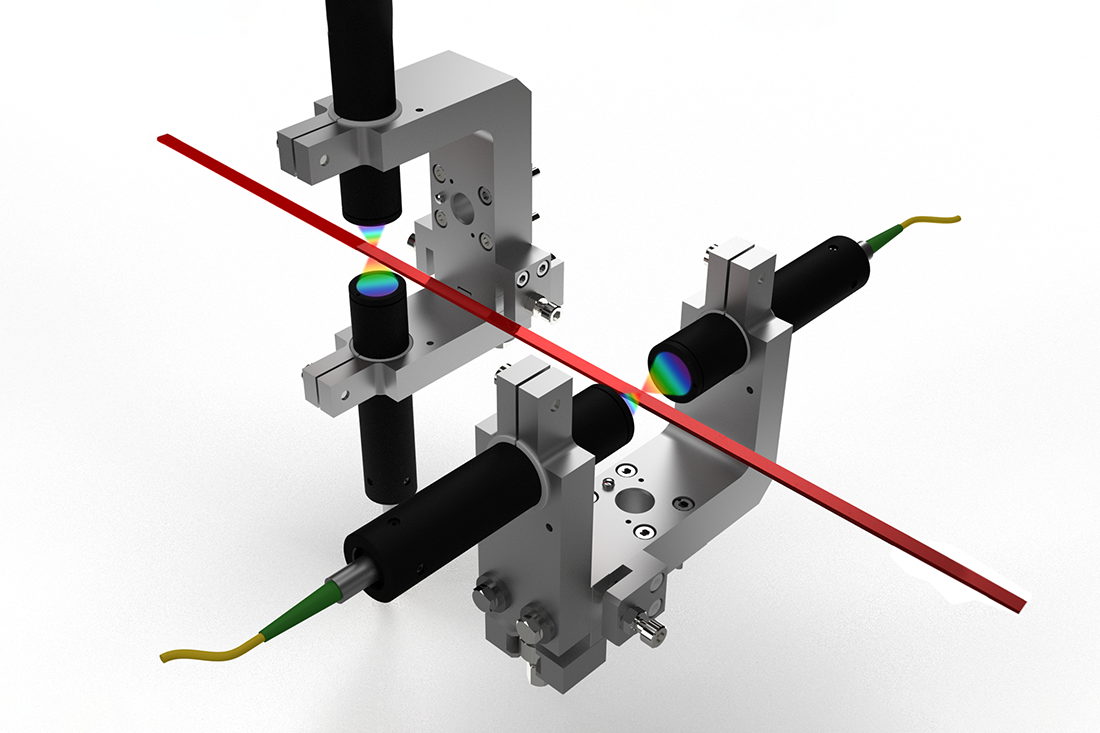
Dependiendo del método de decapado adoptado, pueden producirse diferentes tipos de defectos y por lo tanto es necesario proponer diferentes estrategias de control de proceso.
La tecnología confocal cromática puede medir el grosor del recubrimiento de esmalte en los cables magnéticos, cuando el recubrimiento es transparente a la luz blanca, como normalmente sucede.
Cuando la operación de extracción de esmalte se realiza mecánicamente con una herramienta de fresado, puede ser necesario medir en línea la cantidad de material extraído, para comprobar que la herramienta ha alcanzado el núcleo de cobre y no queda esmalte. En este caso, el uso de sensores confocales en línea puede permitir medir el grosor de esmalte en la sección del cable no elaborada y la altura del paso en el área decapada. Entonces, la introducción de múltiples sensores confocales en configuración de horquilla permite una medición completa de las dimensiones y la simetría de la zona decapada.
En cambio, en operaciones de ablación de láser queda una fina capa de esmalte en algunas áreas específicas, dependiendo del número y orientación de los cabezales láser. En este caso, el uso de tecnología interferométrica permite medir la cantidad de esmalte restante, a partir de un grosor de unas pocas micras.
El interferómetro de luz blanca puede utilizarse en estaciones de medición fuera de línea para realizar una comprobación demuestra el proceso de eliminación de esmalte por láser. Cuando se conoce la ubicación de las concentraciones de esmalte restante, la misma tecnología puede integrarse en línea para un control total del proceso.
En otros casos, puede ser necesario revisar toda la superficie limpiada, buscando defectos y contaminantes como restos de esmalte carbonizados por el láser. El uso de tecnología confocal STIL, aplicada en los sensores ópticos lineales con la familia MPLS, garantiza un elevado campo de enfoque y por lo tanto permite realizar análisis en línea de toda el área decapada e identificar diferentes tipos de defectos.
- Medición dimensional completa e inspección del área decapada
- Posible uso para control del proceso de decapado
- Se evitan defectos en la operación de soldadura de horquilla
- Disponibles soluciones para comprobación fuera de línea y en línea
- Medición del grosor de esmalte con sensores confocales
- Medición completa del área decapada con múltiples sensores confocales
- Medición del grosor de esmalte restante con interferómetro de luz blanca
- Sensores en línea ópticos confocales MPLS para la inspección de defectos en el área decapada
- Posible integración de múltiples tecnologías en la misma estación de medición
Definido según los requisitos del cliente.