Stator Electrical and Functional Testing
The quality control of stators, in both wound and hairpin versions, requires the control of various functional characteristics along the entire production chain. Before impregnation, the resistances and inductances of the windings, as well as parasitic capacitances, are checked, together with the insulation conditions. After impregnation, the end-of-line test of the stator verifies that the impregnation process has preserved the integrity of the winding and improved the insulation.
With the E.D.C. product line, Marposs offers a complete range of electronics and test applications, both manual and automatic, to perform all the functional tests of the stators normally required in the laboratory or on the production line. The same product line can be used to perform similar electrical and functional tests on wound rotors for externally excited synchronous motors or for DC motors.
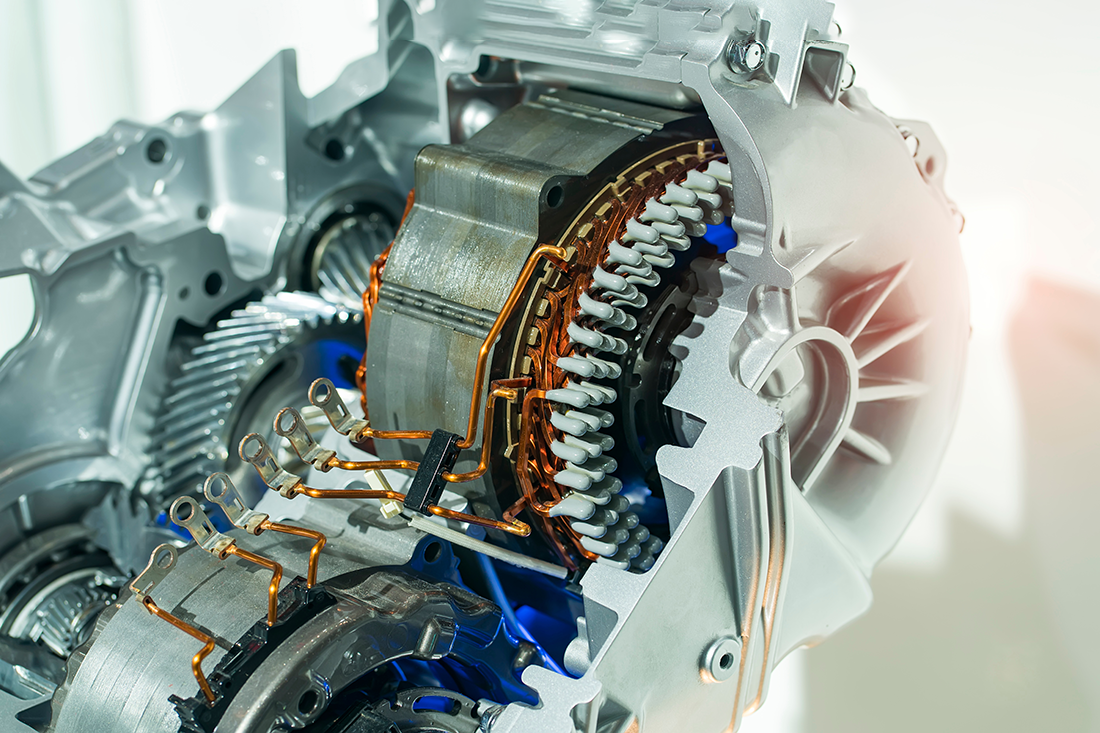
- AC Dielectric Strength Test: allows to identify short-circuited windings between them or with the thermal protector or in contact with the stator pack
- Surge Test: allows to identify short circuits between turns of the same winding, presence of corona effect, losses due to higher than normal parasitic capacitances
- Rotation Test: allows to identify errors that would produce reversals in the direction of rotation of the motor
- Ohmic Resistance Test: allows to identify permanent short circuits inside the winding, open circuits, windings with incorrect number of turns
- Inversion Test: in three-phase stators, allows to identify errors in the connection in which the beginning and end winding wires are inverted with each other
- Insulation test with partial discharge measurement: the PDIV (Partial Discharges Inception Voltage) test performed in production, and compliant with the EN 60034-18-41 standard, is able to identify the presence of latent defects in the insulation that do not immediately generate a loss of functionality of the component, but could determine a failure over time, especially for those motors controlled by inverters due to the overvoltage peaks generated.
- Laboratory/Quality tests for the detection of PDIV (Partial Discharges Inception Voltage) and PDEV (Partial Discharges Extinguish Voltage) with pulse source compliant with the EN 60034-18-41 standard (scanning test with applied voltage in steps), and with 50Hz AC source (scanning test with applied voltage in ramp).
Partial Discharge
Although not yet required by law, partial discharge tests are becoming established in the field of quality control of stators, wound rotors and complete electric motor groups, for use in the automotive sector. They are naturally recommended for all electric motors, even for non-automotive applications, for which a high level of quality and reliability must be guaranteed. The method developed by E.D.C. since 1998 for partial discharge measurement tests is based on capacitive coupling technology. This is a more sophisticated technique, less sensitive to external disturbances and therefore more suitable for applications in the production area, compared to antenna solutions normally available on the market.
Compared to antenna technology, capacitive coupling allows to obtain greater sensitivity and reliability in environments affected by electromagnetic noise, as typically occurs in industrial environments.
The partial discharge test functions are offered by E.D.C. within a complete product line that integrates in a single device all the electrical and functional test options normally required for characterization during design or for quality control on the production line.
To learn more visit www.edcnet.eu
- Advanced winding and stator qualification solutions for development, industrialisation and mass production.
- Customisation of winding and stator qualification solutions to meet specific customer requirements.
- Highly effective in identifying latent defects in the production phase that cannot be detected by traditional dielectric strength and surge tests: Partial discharge measurements allow criticalities and hidden defects to be identified during testing before they can affect the reliability of the product at the end customer. For more information, please refer to Technical Note TN148, which illustrates how Partial Discharge measurements during production testing can easily detect defects in windings.
- In the development and industrialisation phase, PDIV (Partial Discharge Inception Voltage) measurement can be used, for example, to:
- Check the quality of copper/aluminium wires or insulating materials from different suppliers, allowing an objective quality-price evaluation and consequently the selection of the optimum solution.
- Optimise process machine parameters in wound stators, such as selecting the correct winding speed, i.e. the highest speed that can be used without compromising the insulation quality of the wire.
- For hairpin stators, verify that the design parameters (e.g. geometries and bending angles) and the manufacturing process (hairpin bending and insertion into the stator) are such that criticality and latent defects are avoided.
- Monitor the impregnation process by measuring the characteristics of the same stator before and after impregnation. For more details on this subject, see Technical Note TN146, which describes tests carried out on 4 windings with different levels of impregnation quality: no impregnation, standard process impregnation, reduced resin quantity impregnation, reduced solidification time impregnation.
-
To quantify how the inclusion of a phase separator, the impregnation process or both affect the quality of the winding insulation. This study, in addition to improving product knowledge, is essential to definethe motor Class for the use with inverters, as required by EN60034-18-41. For more information on this subject, see Technical Note TN147.
- During the end of life tests (stator/motor), check the number of hours after which the insulation material begins to show permanent degradation of its insulating properties. The PDIV test makes it possible to anticipate the assessment of material degradation before product failure occurs, making it possible to identify which materials and processes have the worst quality and start degrading earlier. This approach, used by major companies in high-reliability industries, enables more accurate selection of materials, processes and suppliers.
- The LT400 is particularly suitable for laboratory activities and production testing in small batches. It is particularly useful in the development phase to identify and correct non-obvious criticalities that could compromise stator reliability, and in the industrialisation phase to define acceptance thresholds to be applied in production testing.
In addition to ensuring complete stator qualification, the LT400 is equipped with several functions to identify latent defect trigger conditions that could compromise reliability, such as PDIV (Partial Discharge Inception Voltage) measurement.
- The AST family of systems is designed to perform complete testing in the production of windings and stators for electric motors.
Their great flexibility and high level of customisation allow the stator to be qualified according to specific customer requirements. The desired tests and their acceptance thresholds can be configured based on the data collected with the LT400 during the development and industrialisation phases, ensuring consistency in stator qualification from the early stages of development through to series production testing.
Like the LT400, the AST is capable of partial discharge testing.