Líneas De Conjunto Para Electrónica De Potencia Y Cargadores De Batería
Marposs ofrece soluciones flexibles para el conjunto completo de unidades de electrónica de potencia, como cargadores de batería e inverters. Pueden ofrecerse diferentes configuraciones, incluyendo operaciones de conjunto manuales o completamente automáticas, según las especificaciones del cliente.
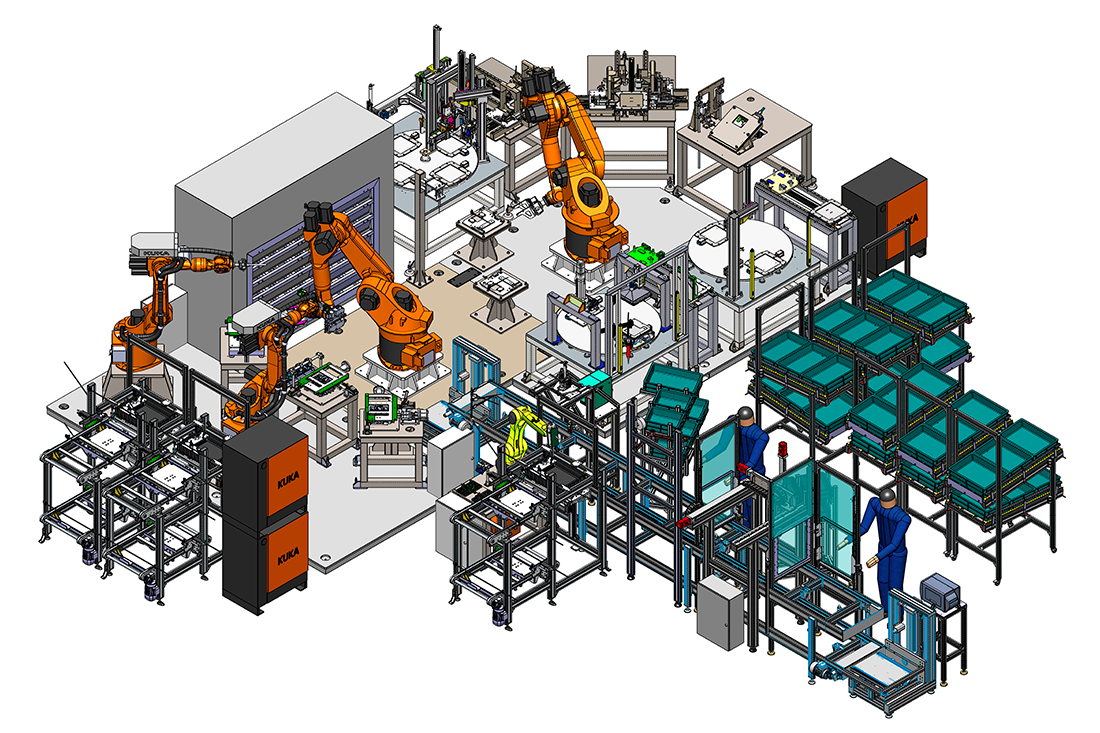
Línea automática para el conjunto de todos los componentes de un cargador de baterías para vehículos eléctricos. El proceso se divide en 2 fases diferentes:
- En la primera, se monta la tapa con los paneles eléctricos.
- En la segunda, se completa el conjunto del lado inferior. Ambos lados se limpian con aire ionizado antes de realizar la prueba de estanqueidad y la prueba eléctrica.
FASE #1
Todas las operaciones son realizadas por operadores en 3 estaciones manuales.
- La tapa es recogida por un operador e ionizada en un área separada.
- Los conectores de la potencia principal se montan en la siguiente estación manual.
- Un operador toma los paneles eléctricos y los enrosca.
Durante las actividades, los operadores son guiados por un ordenador de panel y se efectúa un seguimiento de los componentes mediante la lectura de una matriz de datos.
FASE #2
Durante la segunda fase, las operaciones también se dividen en 2 áreas principales:
- En la primera, los componentes inferiores son procesados por operadores y gestionados por un transportador de cadena.
- En la segunda, las tapas inferiores son gestionadas por robots antropomorfos y montados en estaciones automáticas y mesas giratorias.
Primer área - manejo mediante un transportador de cadena
La caja inferior, con las juntas, es tomada por los operador y ubicada en palets, que son gestionados por el transportador de cadena.
- En la primera estación del transportador, la tapa inferior se limpia con aire ionizado en un área separada.
- En la segunda, un sistema de cámara gestionado por un manipulador eléctrico comprueba que la posición es correcta y las juntas están íntegras.
- La tercera se dedica a los conectores de agua, que son enroscados por los operadores; los tornillos se suministran uno a uno, automáticamente.
- En la cuarta, los operadores sitúan los paneles electrónicos y se enroscan. Los tornillos son automáticamente suministrados uno a uno, también en esta estación.
Todos los componentes tomados para el proceso de montaje son trazados mediante la lectura de la matriz de datos. Los operadores son guiados por el ordenador del panel durante todas las operaciones.
Segunda área – manejo con robot antropomórficos
El robot toma la caja inferior para el proceso de montaje.
- En la primera operación, el circuito de enfriamiento es comprobado con una prueba de fuga de aire (presión 2,5 bar – 15”).
- En la segunda, las bobinas electromagnéticas son tomadas por un segundo robot y situadas dentro de la caja: el primer robot ha colocado antes la tapa inferior en la segunda estación de funcionamiento.
- La tercera está dedicada al proceso de resinado: la caja se precalienta antes de fijar los componentes internos y después se llena con un dispensador de resina
- En la cuarta, el primer robot deja la caja dentro del horno para la maduración de la resina.
En las últimas fases, el proceso está a cargo de las mesas giratorias.
La primera mesa giratoria recibe la caja del robot y después realiza las siguientes actividades:
- El lado inferior de la tapa se limpia con aire ionizado.
- Se monta con un segundo panel electrónico.
- Un operador la enrosca y comprueba con la cámara.
- Al final de toda la rotación de la mesa giratoria, la caja se devuelve al robot.
En la primera fase, la caja superior es recogida manualmente de un área de almacenamiento, montada y enroscada. Después, se completa el proceso con la segunda y tercera mesa giratoria con las operaciones que se describen a continuación:
- La caja se deja en la segunda mesa giratoria para la prueba de fuga de aire (0,20 bar – 15”).
- Es probada por un probador eléctrico, si la prueba es correcta, la caja se marcará con láser.
- Se monta la última válvula en la tercera mesa giratoria antes de ser descargada por el operador.
Estaciones Manuales
- Elevada eficiencia = 90%.
- Elevada flexibilidad de los procesos de conjunto: las estaciones manuales permiten una modificación o una actualización del proceso de montaje con mejoras mecánicas rápidas y fáciles.
- Fácil intercambio de operadores: el ordenador de panel guía a los operadores durante las operaciones manuales. Permite la máxima eficiencia también para los nuevos operadores.
Estaciones Automáticas
- Elevada eficiencia = 90%.
- Proceso de elevada automatización: todas las operaciones críticas son a cargo del dispositivo automático, dejando los procesos de conjunto fáciles a los operadores.
- Fácil intercambio de operadores: el ordenador de panel guía a los operadores durante las operaciones manuales. Permite la máxima eficiencia, también para los nuevos operadores.
- Definido según las especificaciones del cliente
Estaciones Manuales
Tiempo de ciclo al 100% | 239 seg |
Tiempo de ciclo al 90% | 262,9 seg |
Productividad |
15,6 piezas/hora |
Eficiencia | 90% |
Estaciones Automáticas
Tiempo de ciclo al 100% | 210 seg |
Tiempo de ciclo al 90% | 233 seg |
Productividad | 17 piezas/hora |
Eficiencia | 90% |