Test di tenuta a tracciatura elettrolita
Leak B-TRACER
Gli elettroliti tipicamente utilizzati nella produzione di batterie agli ioni di litio sono caratterizzati dalla presenza di VOC (Composti Organici Volatili). Il processo di Leak Test (in attesa di brevetto) sviluppato da Marposs si basa sulla vaporizzazione e sull'estrazione dei VOC dalle celle in caso di perdita, per poi tracciarne e quantificarne la presenza in camera da vuoto.
Il Leak B-Tracer è una stazione semiautomatica facilmente riattrezzabile, progettata per il test di tenuta di diversi tipi di celle di batterie sigillate in diverse operazioni del processo di assemblaggio, prima o dopo la fase di formation e di degasaggio.
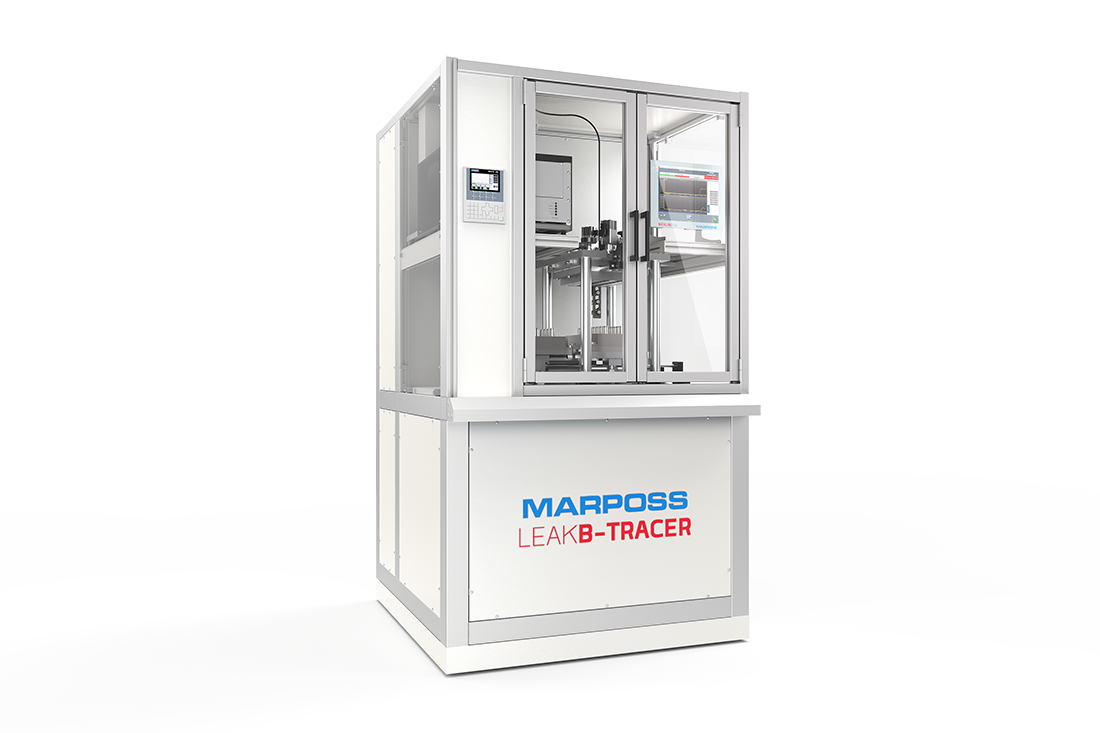
Con le celle batteria caricate nella camera a vuoto e in caso di perdita, il sistema vaporizza i solventi e li estrae dalla cella, di conseguenza il sistema è in grado di quantificare l'entità della perdita utilizzando una versione adeguata di spettrometro di massa.
Il Leak B-Tracer è caratterizzato da una robusta struttura principale in profili di alluminio e da una piastra di base in alluminio. La stazione è circondata da recinzioni di sicurezza in Lexan con una porta sul lato di carico/scarico, dotata di un interruttore di sicurezza interbloccato. Il quadro elettrico, la strumentazione di misura e il dispositivo di prova di tenuta sono assemblati sulla struttura principale.
Il dispositivo automatico è dotato di quanto segue:
- Due vassoi inferiori rimovibili (per il riattrezzamento manuale di diversi formati di celle), in grado di ricevere un lotto di celle batteria. Entrambi sono dotati di una guarnizione per sigillare la camera da vuoto, riferimenti per il posizionamento preciso dei pezzi e di componenti per la riduzione del volume.
- Una slitta orizzontale ad azionamento pneumatico per trasferire i vassoi di fondo da sinistra a destra e viceversa (un vassoio di fondo sarà sempre in posizione di prova mentre l'altro sarà in posizione di carico/scarico, uno a sinistra e uno a destra dell'attrezzatura).
- Una struttura a ponte posizionata centralmente e dotata di un coperchio superiore rimovibile (per il riattrezzamento manuale di diversi formati di cella) per chiudere la camera a vuoto quando si solleva un vassoio inferiore.
- Un sollevatore pneumatico per sollevare e abbassare il vassoio inferiore nella posizione di prova, nonché per chiudere e aprire la camera da vuoto contro il coperchio superiore.
La quantità e il tipo di celle da testare possono essere facilmente modificati in caso di nuove esigenze, mediante il riattrezzamento manuale dei due vassoi inferiori, rendendo così il Leak B-Tracer in grado di testare qualsiasi tipo di cella (prismatica, cilindrica, bottone, pouch).
Il sistema può lavorare facilmente con qualsiasi tipo di elettrolita (DMC, EMC, PP, ...).
Inoltre, utilizzando la procedura di scansione AMU (Atomic Mass Unit), questo sistema può facilmente identificare il valore AMU corretto da tracciare, senza conoscere la ricetta del solvente.
Il Leak B-Tracer è dotato della soluzione Marposs “Fast Response System”, che consiste in uno spettrometro di massa collegato a un Marposs Merlin Plus industriale e al software Marposs “SOLT” per la gestione dei cicli di misura e per la memorizzazione locale dei dati di prova.
L'IPC può essere utilizzato anche per la memorizzazione locale dei dati e delle statistiche.
Per ogni pezzo testato, i seguenti dati possono essere memorizzati sulla memoria locale dell'IPC:
- Data e ora del test
- Risultato (buono o scarto)
- Valore effettivo della pressione di prova
- Valore di perdita
- Parametri di prova (pressione di prova e limite di scarto)
Un test periodico dell'integrità delle guarnizioni e della strumentazione sarà eseguito utilizzando una parte certificata “Master Leak”.
Il Master Leak, progettato con un valore di perdita vicino al limite di scarto richiesto, sarà riempito con lo stesso solvente utilizzato per il tracciamento dell'elettrolita delle celle batteria. Verrà inserito manualmente dall'operatore quando sarà necessario un ciclo master per verificare la funzionalità del sistema senza dover calibrare il sistema di misura.
L'integrazione di un sistema di rilevamento delle grosse perdite, per ridurre il tempo di ciclo sulle celle con grandi perdite, protegge anche lo spettrometro di massa dalla contaminazione dovuta all'alta concentrazione di solvente durante la fase di test.
Uso previsto:
- Test di tenuta su prototipi e linee pilota
- Test off-line e analisi SPC
- Ricontrollo di un lotto di scarto da un test nella produzione di massa
Le competenze di Marposs sul metodo di tracciamento dell'elettrolita, combinate con l'esperienza nel campo dell'automazione, consentono di offrire soluzioni per l'integrazione di questa tecnologia nelle linee di produzione di celle batteria, in grado di soddisfare i più severi requisiti di tempo di ciclo.
- Il test si applica a qualsiasi tipo di cella (bottone, cilindrica, prismatica o pouch), attraverso un facile sistema di riattrezzamento della camera da vuoto
- Il test è applicabile a qualsiasi fase del processo, anche dopo il riempimento dell'elettrolita e la sigillatura
- Test appropriato per diversi tipi di elettrolita
- Procedura di test rapida
- Test di grossa perdita per prevenire la contaminazione
- Dimensioni massime della camera: Larghezza 280 mm x Profondità 160 mm x Altezza 250 mm
- Tempo di ciclo tipico: da 15 a 60 (*) secondi
- Tipo di elettrolita: DMC - EMC - DEC - MB - EA - EC - PP - PC - ecc.
*A seconda del tipo, delle dimensioni e del numero di celle
- Test di celle cilindriche e bottone
Possono essere forniti diversi utensili, progettati in base alle dimensioni della cella.
- Test delle celle prismatiche
Possono essere forniti diversi utensili, progettati in base alle dimensioni della cella.
- Test delle celle pouch
Per il test delle celle pouch, l'implementazione del metodo prevede l'uso di strumenti speciali. La cella deve essere contenuta rigidamente durante il test per evitare il rigonfiamento della stessa nella camera da vuoto. Questo test consente di rilevare la presenza di perdite nei punti particolarmente critici delle saldature lungo tutto il bordo della cella.