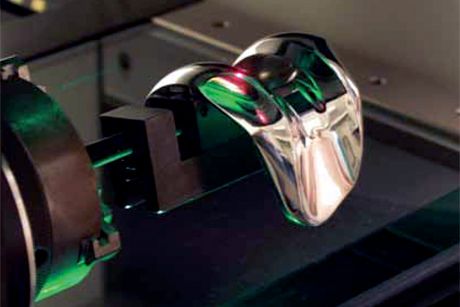
Compared to many other industries, medical device manufacturing
has unique concerns about patient welfare, with
lingering thoughts of liability. "These concerns drive extreme
process control" explains Frank Powell, product manager for
Marposs (Auburn Hills, MI), a provider of in-process gaging and measurement equipment. “We have installed systems that
use a 2-D bar code on each part to relate gaging data, what operation
it was measured on, what the measurements were, and
even which machine it was made on and who was the operator
at the time,” he says.
Another example of the extreme care sometimes needed
in medical device manufacturing was the company’s experience
in developing a mark-free measuring system for titanium
hip joints. The ball and socket have to mate perfectly, requiring
a superfinish for a nearly friction-free range of motion.
Specialized machine tools create the superfinish. In-process
gages monitor and control these machines.
The problem is
that titanium is a highly reactive metal that attaches readily
to carbon-based materials, such as the diamond commonly
used for precision gage contacts. The buildup on the carbonbased
contacts led to inaccuracies. Modern ceramics provide
the best wear characteristics.
Machining processes using
contact gages can leave a mark on the workpiece. In most
cases, it would not affect the functional performance of the
artificial joint. As Powell points out, however: “Surgeons are
not metrologists.” If they see a mark, concerns over patient
welfare will lead them to reject and scrap the part. In response,
Marposs works with process engineers and machine builders
to fine-tune the grinding process to prevent visible marks.
Powell concludes that more inspection systems will be needed
to control quality in the future.
Read the Medical Metrology article, that first appeared in the March 2012 issue of Manufacturing Engineering® MEDICAL Manufacturing 2012 Yearbook.
Copyright Notice: 2012 Copyright by Society of Manufacturing Engineers. All rights retained. This article may only be viewed or printed one (1) time for personal use. User may not save any text or graphical items to hard drives or duplicate this article in whole or in part in any medium. This article appears with permission from Manufacturing Engineering®, the official publication of the Society of Manufacturing Engineers (SME). www.sme.org