Linee di assemblaggio per elettronica di potenza e caricabatterie
Marposs fornisce soluzioni flessibili per l'assemblaggio completo di unità elettroniche di potenza, come caricabatterie e inverter. Sono disponibili configurazioni diverse, comprese operazioni di assemblaggio manuali o completamente automatiche, a seconda delle specifiche del cliente.
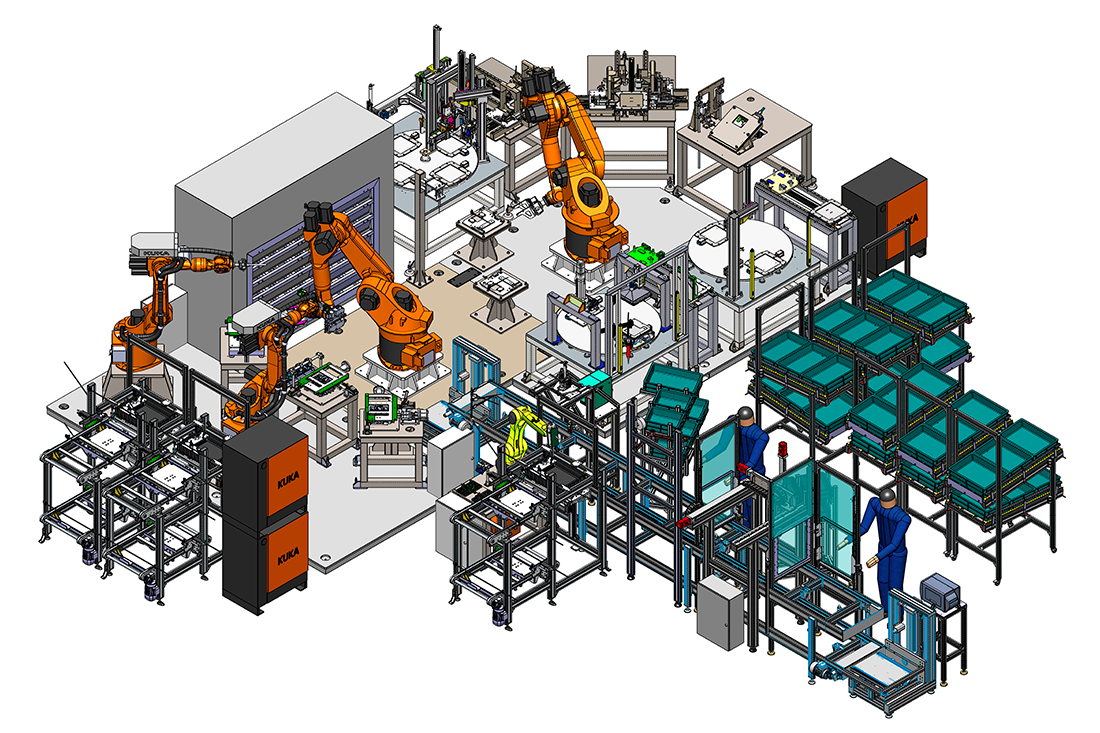
Linea automatica per l'assemblaggio di tutti i componenti di un caricabatterie per veicoli elettrici. Il processo si divide in due fasi diverse:
- Nella prima viene assemblata la copertura con le schede elettroniche.
- Nella seconda viene eseguito l’assemblaggio del lato inferiore. Entrambi i lati vengono puliti con aria ionizzata prima di eseguire i test di tenuta e il test elettrici.
FASE #1
Tutte le operazioni sono eseguite dagli operatori in 3 stazioni manuali.
- Il coperchio viene raccolto dall'operatore e ionizzato in un'area separata.
- I connettori elettrici principali vengono assemblati nella stazione manuale successiva.
- Le schede elettriche vengono prelevate e avvitate dall’operatore.
Durante tutte le attività, gli operatori vengono guidati da un panel PC e i componenti vengono tracciati tramite lettura di data matrix.
FASE 2
Anche durante la seconda fase le operazioni sono divise in due aree principali:
- Nella prima, i componenti inferiori vengono lavorati dall’operatore e movimentati da un convogliatore a catena.
- Nella seconda, le coperture inferiori vengono movimentate da robot antropomorfi e assemblate da stazioni automatiche e tavole rotanti.
Prima area - movimentazione con convogliatore a catena
L’intelaiatura inferiore, completa di guarnizioni, viene prelevata dagli operatori e messa su un pallet, movimentato dal convogliatore a catena.
- Nella prima stazione del convogliatore, la copertura inferiore viene pulita con aria ionizzata in un’area separata.
- Nella seconda, un sistema di telecamere gestito da un manipolatore elettrico controlla il corretto posizionamento e l’integrità delle guarnizioni.
- La terza operazione è dedicata ai raccordi idraulici, che vengono avvitati dagli operatori. Le viti vengono fornite una a una, automaticamente.
- Durante la quarta, le schede elettroniche vengono posizionate dagli operatori e avvitate. Le viti vengono fornite automaticamente una a una, anch'esse in questa stazione.
Tutti i componenti prelevati per il processo di assemblaggio vengono tracciati mediante lettura di data matrix. Gli operatori vengono guidati da un panel PC durante l’intera operazione.
Seconda area: movimentazione mediante robot antropomorfi
Il robot raccoglie l’intelaiatura inferiore per il processo di assemblaggio.
- Nella prima operazione, il circuito di raffreddamento viene controllato mediante test di tenuta aria (pressione 2,5 bar - 15”).
- Nella seconda, le bobine elettromagnetiche vengono prelevate da un secondo robot e posizionate nell’intelaiatura: la copertura inferiore è stata precedentemente posizionata sulla seconda stazione di lavoro dal primo robot.
- La terza è dedicata al processo di applicazione della resina: l’intelaiatura viene preriscaldata prima del fissaggio dei componenti interni e quindi riempita per mezzo di un dispenser di resina.
- Nella quarta, l’intelaiatura viene lasciata dal primo robot all’interno del forno per l'essiccazione della resina.
Nelle ultime fasi, il processo è affidato a tavole rotanti.
La prima tavola rotante riceve l’intelaiatura dal robot ed esegue le seguenti operazioni:
- Il lato inferiore della copertura viene pulito con aria ionizzata.
- Viene assemblato con una seconda scheda elettronica.
- Viene avvitato dall'operatore e controllato dalla telecamera.
- Al termine della rotazione completa della tavola, l’intelaiatura viene restituita al robot.
Nella fase finale, l’intelaiatura superiore viene raccolta manualmente da un'area di stoccaggio, montata e avvitata. Dopodiché, il processo viene completato dalla seconda e dalla terza tavola rotante con le operazioni descritte di seguito:
- L’intelaiatura viene lasciata sulla seconda tavola rotante per l’ultimo test di tenuta aria (0,20 bar - 15”).
- Viene testata dal tester elettrico e, se il risultato è positivo, viene marcata dal laser.
- L’ultima valvola viene assemblata sulla terza tavola rotante prima dello scarico da parte dell’operatore.
Stazioni manuali
- Efficienza elevata = 90%
- Elevata flessibilità del processo di assemblaggio: le stazioni manuali consentono una modifica e/o un upgrade del processo di assemblaggio con miglioramenti meccanici facili e veloci.
- Facile cambio dell’operatore: il panel PC guida gli operatori durante le operazioni manuali. Consente la massima efficienza anche per i nuovi operatori.
Stazioni automatiche
- Efficienza elevata = 90%
- Processo altamente automatizzato: tutte le operazioni critiche sono affidate a dispositivi automatici, lasciando agli operatori i semplici processi di assemblaggio.
- Facile cambio dell’operatore: il panel PC guida gli operatori durante le operazioni manuali. Consente la massima efficienza, anche per i nuovi operatori.
- Definite a seconda delle specifiche del cliente
Stazioni manuali
Tempo di ciclo al 100% | 239 sec |
Tempo di ciclo al 90% | 262,9 sec |
Produzione |
15,6 pezzi / ora |
Efficienza | 90% |
Stazioni automatiche
Tempo di ciclo al 100% | 210 sec |
Tempo di ciclo al 90% | 233 sec |
Produzione | 17 pezzi / ora |
Efficienza | 90% |