Neue Trends und Qualitätsstandards in der Glasherstellung: Qualitätskontrolle verbessern!
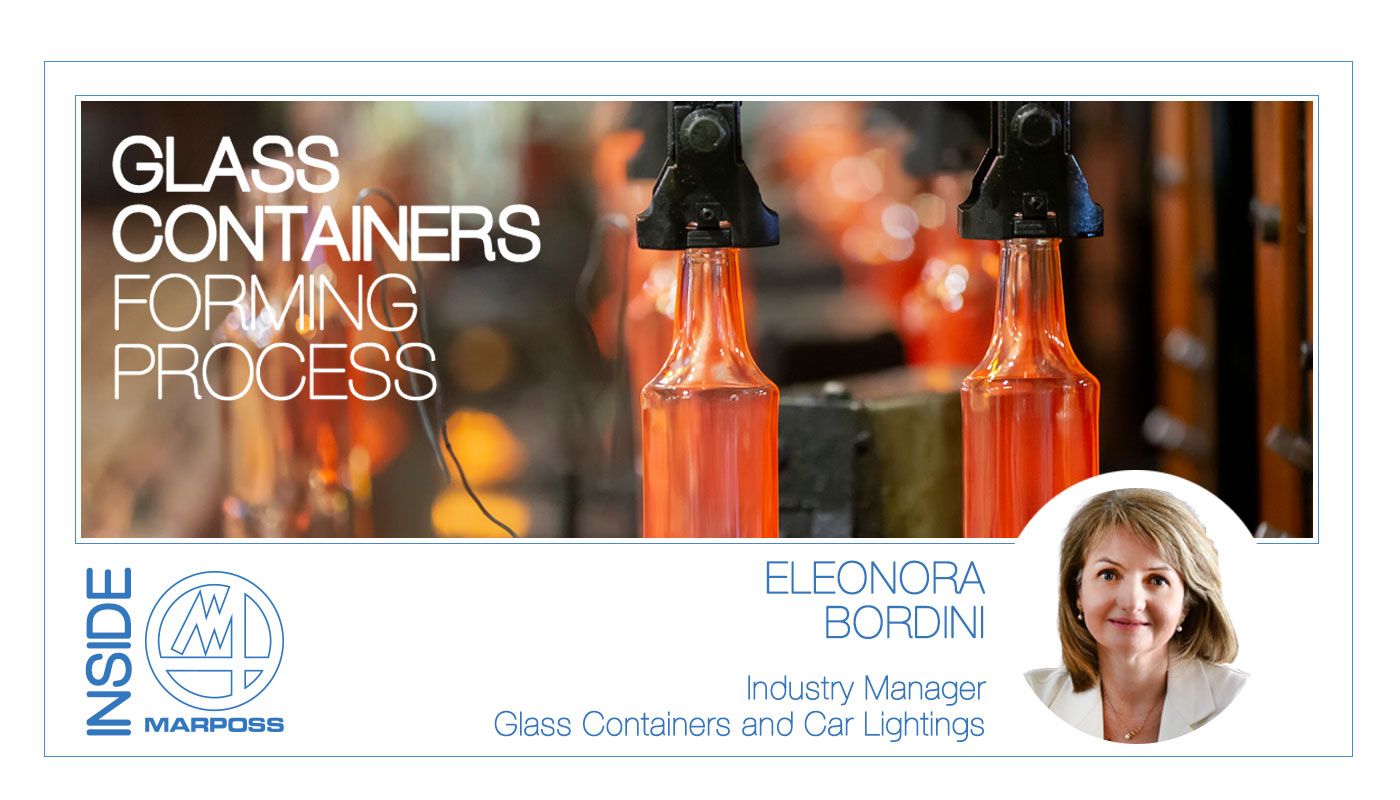
Die Evolution in der Glasherstellung
Glas ist einer der ältesten Werkstoffe. Die Geschichte von Glas reicht zurück bis 3500 Jahre vor Christus. Der erste Hohlglasbehälter wurde etwa 1500 Jahre v. Chr. in Ägypten hergestellt.
Die Erfindung der Glasmacherpfeife im ersten Jahrhundert v. Chr. kam einer Technikrevolution gleich. Die echte Revolution kam jedoch mit dem ersten Flaschenblasautomat, den Michael Owens zu Beginn des 20. Jahrhunderts in den USA erfunden hatte. Der Automat konnte bis zu 2.500 Behälter/Stunde herstellen und ermöglichte somit eine Glasbehälterfertigung im industriellen Maßstab.
Die noch heutzutage aktuelle Blas-Blas- bzw. Press-Blas-Technologie fand 1925 mit der ersten IS-Maschine (IS = Individual Sections) mit ihren einzelnen Produktionsstationen eine weitere Verbesserung. In jeder dieser Stationen werden ein oder mehrere Behälter unabhängig voneinander gefertigt. Ein Tropfen flüssiges Glas fällt in eine leere Form, wo er mit dieser Technologie vorgeblasen oder mit einem Kolben vorgepresst wird. Der vorgeformte Posten Tropfen (Glasrohling) wird dann in eine Fertigform geleitet, wo er fertig geblasen wird.
Moderne Formmaschinen können heute bis zu 20 einzelne Produktionsstationen aufweisen, in denen jeweils gleichzeitig 1 bis 4 Behälter produziert werden können. Somit fallen immer 1-4 Tropfen (SG = Einzeltropfen, DG = Doppeltropfen, TG = Dreifachtropfen, GD = Vierfachtropfen) geschmolzenes Glas in die pro Produktionsstation vorhandenen 1 bis 4 Formen. Und dies geschieht parallel in jeder Station. Je nach Behältergröße und -form beträgt die Fertigungsgeschwindigkeit somit bis zu 700 Behälter/min.
Glasbehälter: Eigenschaften und Vorzüge
Behälter aus Glas finden Anwendung als Verpackung in verschiedenen Industriezweigen:
- Lebensmittel und Getränke
- Parfüm und Kosmetik
- Pharmazeutische Produkte
Glas ist inert: Vom Glas geht nichts in das Produkt über und nichts kommt von außen durch das Glas in das Produkt.
Glas ist nachhaltig (zu 100 % recycelbar).
Glas ist schön und erhöht den wahrgenommenen Produktwert und die Produktqualität im Vergleich zu anderen Verpackungsmaterialien wie Plastik und Aluminium.
Glas ist jedoch im Vergleich zu anderen Werkstoffen viel schwerer. In den vergangenen Jahren wurde der Fertigungsprozess dahingehend verbessert, dass Leichtglasbehälter hergestellt werden können. Somit sind Glasbehälter heute bis zu 40% leichter als vor 20 Jahren. Weniger Gewicht ist eine Notwendigkeit, nicht nur für weniger Transportkosten, sondern vor allem auch, um Rohstoffe und Energie einzusparen.
Auch an den Schmelzöfen wurden bedeutende Technologieverbesserungen vorgenommen, um den Energieverbrauch und CO2-Emissionen zu reduzieren.
Außerdem wurden Glasbehälter in der Form immer komplexer. Einzigartige Formen erhöhen den Produktwert (Premiumisierung) und die Markenwahrnehmung. Denken wir nur daran, wie leicht eine Coca-Cola-Flasche oder ein Nutellaglas erkannt werden können, auch wenn sie leer und ohne Etikett sind.
Trends in der Glasherstellung: Qualitätskontrolle verbessern
Glashersteller legen auch immer mehr Wert auf die Qualität ihrer Produktion, mit dem Ziel, weniger Ausschussteile zu produzieren und jeden Anlass für Kundenbeschwerden zu vermeiden.
Die Qualitätskontrolle sollte dem frühestmöglichen Stadium des Glasherstellungsprozesses beigeordnet sein, um im Fehlerfall sofort die nötigen Abhilfemaßnahmen einzuleiten.
Die Kontrolle auf Unvollkommenheiten an Behälterboden, -körper, -hals und der Oberflächenbeschaffenheit wird während der gesamten Fertigung mit In-line Kontrollstationen überwiegend berührungslos (Kameras und andere optische Sensoren) ausgeführt.
Die Maßkontrolle erfolgt auf Musterbasis in der Nähe der Fertigungslinie, mit Gut-/Schlechtlehren oder, alternativ, mit manuellen bzw. halbautomatischen/automatischen Messsystemen im Messraum.
Bei Glasbehältern sind folgende Maßkontrollen durchzuführen:
- Gesamthöhe
- Achsabweichung
- Mündungsparallelität
- Außendurchmesser, oder lange/kurze Seiten und Diagonalen am Körper
- Außendurchmesser am Behälterhals
- Viele andere Parameter am Oberflächenfinish (z.B. Durchmesser, Höhen, Radien, Winkel...) bei allen Finish-Arten
Die Kontrolle mit Gut-/Schlechtlehren bringt ein großes Fehlerpotential mit sich: sie gibt keine Aussage zur Quantität und verlässt sich voll auf die Fähigkeiten des Bedieners. Zudem entstehen dadurch hohe Kosten, weil für jeden hergestellten Artikel ein Satz spezifischer Gut-/Schlechtlehren vorzuhalten ist, der auch verwaltet und periodisch nachkalibriert werden muss. Mit dieser Technologie können außerdem keine Daten gesammelt und keine statistische Analyse zur Prozessverbesserung durchgeführt werden.
Halbautomatische Messsysteme basieren auf einer taktilen oder optischen Technologie. Der zu messende Behälter wird manuell be-/entladen und der Messzyklus läuft dann automatisch ab. Optische Messsysteme sind flexibel und können unterschiedliche Behälter unabhängig von deren Größe, Form und Farbe und ohne Jobwechsel messen.
In automatischen Messsystemen werden sowohl das Be-/Entladen der Behälter als auch die Messungen vollautomatisch ohne Eingriff des Menschen ausgeführt. Die Messtechnologie ist hier überwiegend berührungslos und zusätzlich zu den Außenabmessungen können auch andere Merkmale, wie Mündungsinnendurchmesser und -profil, Wanddicke, Gewicht, Einstichboden und Profil des Etikettierbereichs gemessen werden.
Automatische Messsysteme haben gegenüber halbautomatischen Systemen den Vorteil, dass erheblich weniger Personalkosten entstehen.
Die Messergebnisse aus den halbautomatischen und automatischen Messsystemen werden zu einer speziellen MES (Manufacturing Execution Software) gesendet und die Entscheider können dann den Fertigungsprozess in Echtzeit abstimmen und überwachen.
Andere Kontrollen an Glasbehältern, die auf Musterbasis im Messraum ausgeführt werden, sind:
- Stoßprüfung
- Vertikallast
- Abdrücktest
- Messung Innenvolumen
- Eigenspannung
Marposs bietet die komplette Lösungspalette für Glasbehältermessungen