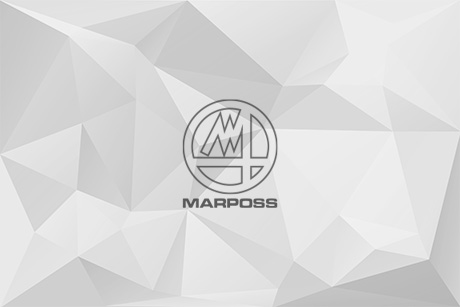
In line with current trends, Marposs UK has aligned its sales response to match one of its major customers' requirements.
The customer, Ford Motor Company, has provided full office services for a resident Marposs engineer at its Dunton Technical Centre, Essex, England within the process engineering section, allowing daily contact at all levels. One of the main aims of this co-operation is to save time in many areas. Marposs makes its expertise readily available to Ford for both general and specific queries, and Marposs can obtain technical information and decisions regarding ongoing projects more simply and quickly. The end result is to reduce the overall time from the start of a new project to full-scale production.
At a local level, Ford's two engine plants in the UK, Dagenham (diesel) and Bridgend (petrol) are to be supported by two "point of contact" engineers, both Coventry based. These engineers will ensure a closer liason between the Marposs sales & service organisation and all parts of the plants using Marposs equipment. These two plants are the recipients of equipment sourced by the Dunton Technical Centre and one target is to maintain continuity throughout the project life.