Technologien -- Digitales Scannen
Digitales Scannen bezeichnet eine Messtechnik, die angewendet werden kann, wenn eine oder mehrere statische Kontrollen nicht mehr ausreichen, um die Dimensionsmerkmale und die Form der vermessenen Komponente zu bestimmen. Das ist oft zum Vermessen mechanischer Komponenten erforderlich, die unter höchst präzisen Paarungsbedingungen arbeiten. Im Allgemeinen wird diese Messtechnik zur Erfassung bestimmter Formfehler des Werkstücks empfohlen.
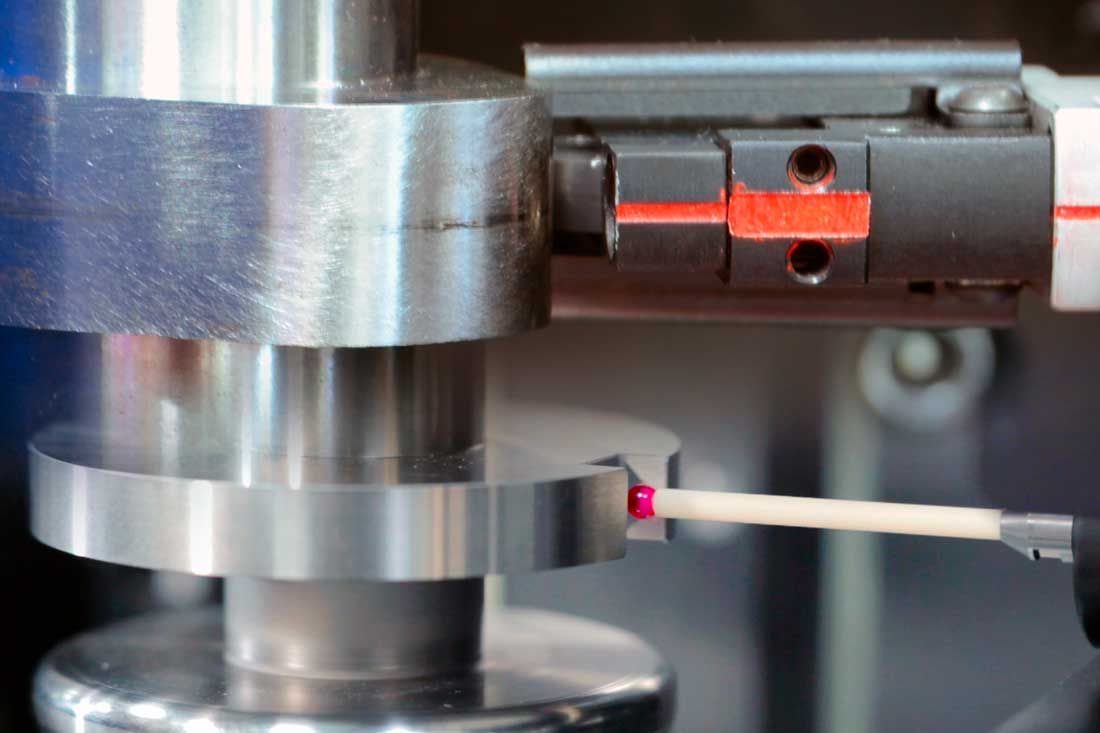
Im Vergleich zur statischen Kontrolle mechanischer Werkstücke bietet digitales Scannen verschiedene Vorteile:
-
Detaillierte Überprüfung und Datensammlung über die gesamte gescannte Fläche
-
Bewertung des Funktionsverhaltens der Komponente
-
Nützliche Informationen zum Einrichten und zur Steuerung des Fertigungsprozesses
Während der Ermittlung der Messdaten werden das Messgerät und die vermessene Komponente in ständiger Bewegung im Verhältnis zueinander gehalten. Daraus ergibt sich ein Vektor aus Messproben, der das Dimensionsprofil der Komponente in der Abtastrichtung darstellt. Dieser Vektor, der mit verschiedenen Methoden gefiltert und verarbeitet werden kann, wird dazu verwendet, Messwerte zu erzeugen, die den tatsächlichen Zustand des Werkstücks mit Bezug auf seine Größen- und Formtoleranzwerte darstellen.
Abtastgeschwindigkeit und -frequenz hängen von der Genauigkeit ab, die bei der jeweiligen Messanwendung gefordert ist.
Axiale Scan-Prüfung zylindrischer Komponenten
Ein Beispiel für häufig verwendetes digitales Scannen ist die axiale Abtastung zylindrischer Komponenten wie Löcher und Stifte.
Um das korrekte Funktionsverhalten von Komponenten sicherzustellen, die unter besonders präzisen Paarungsbedingungen arbeiten müssen - wie etwa Spritzkörper, Nadeln, Ventile oder Pumpen - kann es nötig sein, die Paarungsdurchmesser, die Formfehler und die axiale Ausdehnung der jeweiligen Paarungsfläche zu vermessen. Das geschieht durch einen kompletten Scan.
Es gibt verschiedene Messgeräte, die zu diesem Zweck verwendet werden können:
- Pneumoelektronische Messdorne und -ringe
- Kontaktelektronische Messgeräte
- Optische Messköpfe
- Scan-Messsysteme
Beim digitalen Scannen eines Lochs wird der Dorn während der Erfassung der Durchmesserwerte in ständiger Bewegung auf der Bohrungsachse gehalten. Daraus ergibt sich ein Vektor aus den Messproben, der das Durchmesserprofil, seine Variationen und die Abtastachse darstellt.
Auf der Grundlage dieses Probenvektors können die Messwerte nach verschiedenen Formeln für den durchschnittlichen Durchmesser, die absolute Maximalgröße und die absolute Minimalgröße der gesamten vermessenen Fläche verarbeitet werden. Andere gemessene Formfehler wie Konizität, Balligkeit und Geradheit können ebenfalls verarbeitet werden.
Scannen des Umfangs zylindrischer Komponenten
Dasselbe Konzept des digitalen Scannens kann angewandt werden, um dynamische Durchmesser und die Rundheit von Rotationskörpern zu vermessen. In diesem Fall wird das vermessene Werkstück bei der Erfassung der Durchmesserwerte in einer Rotation mit konstanter Drehzahl gehalten.
Abhängig von der Anzahl und Anordnung der nötigen Messstellen werden mehrere Werkstück-Vermessungen verarbeitet. Das geschieht zum Beispiel beim durchschnittlichen Mindest- oder Maximaldurchmesser sowie bei Formfehlern wie Ovalität und Rundheit.
Bei komplexeren Werkstücken, wie etwa einer Nockenwelle, muss das Nockenprofil digital gescannt werden, um die tatsächliche Form zu kontrollieren und um zu bewerten, ob das Funktionsverhalten der Komponente korrekt ist.
Scan-Kontrollen werden immer bei Messvorrichtungen mit dynamischen Messungen verwendet. Typische Anwendungen:
- M39S Scan-System zum axialen Scannen von Einspritzkomponenten
- M57 Profile und M110 Profile zum Scannen von Nockenprofilen
- OPTOQUICK zum Scannen von Nocken- und Kurbelwellen
- G25-Messsystem zum Scannen an Schleifmaschinen, Zahnradmaschinen und Verarbeitungszentren