LT-H Leak Test-Helium
HELIUM TEST BENCH FOR BATTERY CHILLER
Leak testing is used to detect leaks of the Battery Chiller; the analysis is carried out on the Coolant and Refrigerant Flow Paths. In order to improve productivity, the machine is equipped with three Vacuum Chambers and it verifies that no leakage is associated to the circuits system, simulating real operating condition.
Before the assembly on the propulsion system, a crucial step is to verify the tightness of the battery chiller to ensure the efficiency and the long-term reliability of the global system.
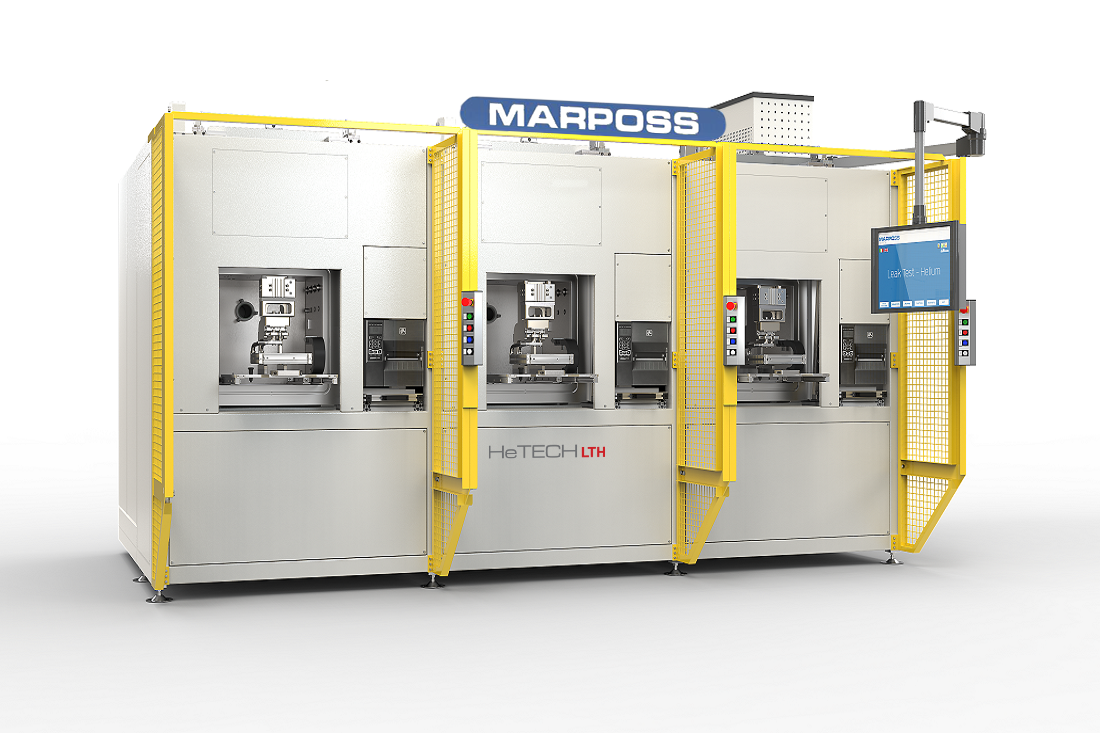
The test fixture is of great importance and it is designed in strict cooperation with the customer in order to grant maximum performance and satisfy the customer needs and specifications.
HMI is made by a touch-screen color monitor and two remote control boxes (one for each chamber) with the push-buttons and the light signals for the operator.
The machine is suitable to be connected to a helium recovery system.
The test tooling is made by a nest where the part under test has to be placed and one coupler for connection to the process circuit of the machine.
The test tooling is equipped with 4 connections, 2 for the coolant circuit and other 2 for the refrigerant circuit.
Each tooling is equipped with a marking system to mark the part with a dot.
With this tooling, it is possible to test both circuits with helium, for external and also internal (between the two circuits) leakage.
The control system is made by an industrial PC with 15” touch-screen colour monitor joined to a PLC.
The PC is used for HMI functions and communication with the server (data transfer in both directions), while the PLC is used to manage the whole cycle (driving of all the electrical, mechanical and pneumatic devices) and to exchange signals with the external handling system.
Test pressures, rejection thresholds and productivity that our machines can reach may vary according to the technical specifications of the component and the production needs of the User.
- Dedicated pumping system for the analysis - Total flow
- Pumping system placed on a cart for easy maintenance
- Dedicated Electric and Pneumatic cabinet
- Ventilation and Sound proofing of the pumping system
- Totally customizable HMI interface
- Full traceability of the tested component
- Ready for MES communication