Chaînes D’Assemblage Pour Électronique De Puissance Et Chargeurs De Batteries
Marposs fournit des solutions flexibles pour l’assemblage complet d’unités électroniques de puissance, comme les chargeurs de batteries et les convertisseurs. Différentes configurations, comprenant les opérations d’assemblage manuelles ou entièrement automatiques, peuvent être fournies selon les spécifications du client.
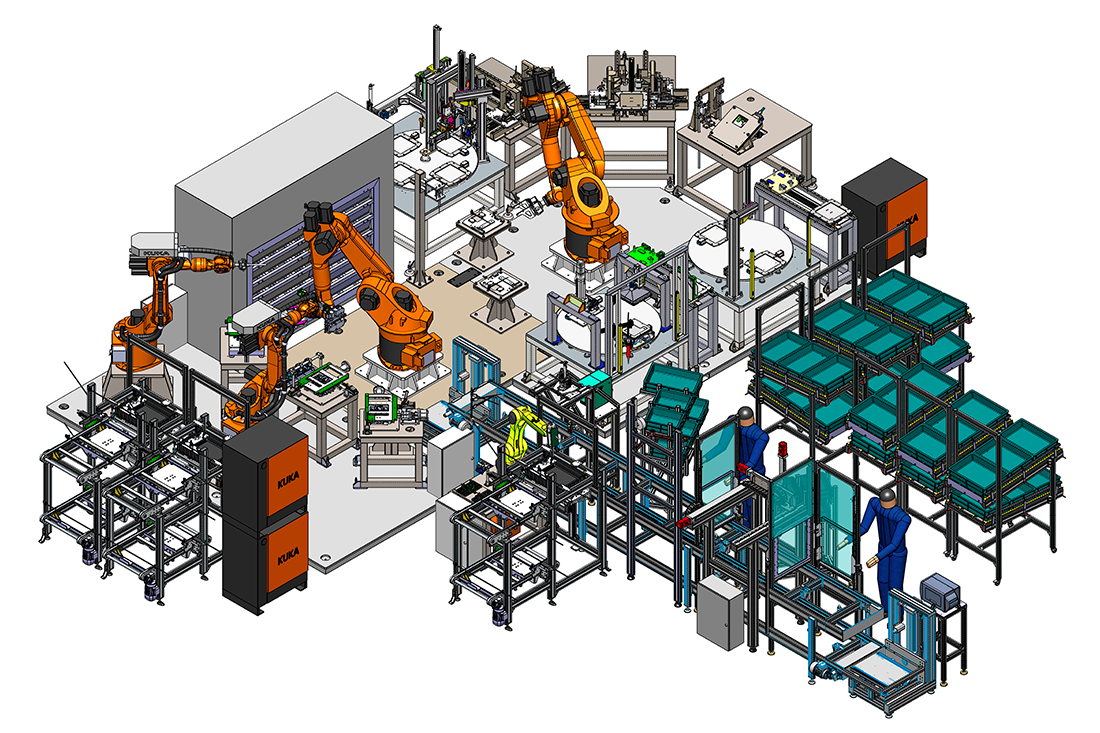
Chaîne automatique pour l’assemblage de tous les composants d’un chargeur de batterie pour véhicules électriques. Le procédé se divise en deux phases distinctes :
- Dans la première, le revêtement avec les cartes électroniques sont assemblés.
- La deuxième consiste à l’assemblage de la base. Les deux parties sont nettoyées à l’air ionisé avant de réaliser la détection de fuites et les tests électriques.
PHASE #1
Toutes les opérations sont réalisées par des opérateurs sur 3 stations manuelles.
- Le revêtement est collecté par l'opérateur et ionisé dans une zone isolée.
- Les connecteurs d’alimentation sont assemblés dans la station manuelle suivante.
- Les cartes électriques sont prélevées par l’opérateur et vissées.
Pendant toutes les opérations, les opérateurs sont guidés par un écran d’ordinateur et les composants sont suivis par lecture Datamatrix.
PHASE #2
Pendant la deuxième phase, les opérations sont aussi divisées en 2 principales zones :
- Dans la première, les composants de la base sont traités par les opérateurs et déplacés sur un convoyeur à chaîne.
- Dans la deuxième, les revêtements de la base sont manipulés par des robots anthropomorphes et assemblés par des stations automatiques et des tables tournantes.
Première zone - manutention par convoyeur à chaîne
Les caissons, complétés de joints sont prélevés par les opérateurs et disposés sur palettes, transportés par un convoyeur à chaîne.
- Dans la première station du convoyeur, le revêtement de la base est nettoyé à l’air ionisé dans une zone isolée.
- Dans la deuxième, un système de caméra géré par un manipulateur électrique, contrôle la position et l’état des joints.
- La troisième est dédiée aux connecteurs à eau qui sont vissés par les opérateurs ; les vis sont fournies une par une, en mode automatique.
- Sur la quatrième, les cartes électroniques sont insérées par les opérateurs et vissées. Les vis sont là aussi fournies en mode automatique, une par une.
Tous les composants, prélevés pour la procédure d’assemblage, sont tracés par lecture Datamatrix. Les opérateurs sont guidés par un écran d’ordinateur pendant toutes les opérations.
Deuxième zone - manutention par robots anthropomorphes
Le robot prélève le revêtement de base pour l’assemblage.
- Lors de la première opération, le circuit de refroidissement est contrôlé par détection de fuite d’air (pression 2,5 bars - 15’’).
- Lors de la deuxième, des bobines électromagnétiques sont prélevées par un second robot et positionnées dans le caisson : le revêtement a préalablement été posé sur la deuxième station de travail par le premier robot.
- La troisième est destinée au procédé de résinage : le caisson est préchauffé avant de fixer les composants intérieurs puis remplie par un distributeur de résine.
- Lors de la quatrième, le caisson est laissé par le premier robot dans le four pour séchage de la résine.
Au cours des dernières phases, le procédé passe aux tables tournantes.
La première reçoit le caisson par le robot et effectue les opérations suivantes :
- La partie basse du revêtement est nettoyée à l’air ionisé.
- Elle est assemblée à une deuxième carte électronique.
- Elle est vissée par l’opérateur et contrôlée par une caméra.
- La rotation de la table terminée, le caisson est rendu au robot.
En phase finale, le caisson supérieur et prélevé manuellement dans une zone de stockage, assemblé et vissé. Ensuite, le procédé se termine sur la deuxième et la troisième table tournante, où sont effectuées les opérations suivantes :
- Le caisson est laissé sur la deuxième table tournante pour la dernière détection de fuites (0,20 bar – 15”).
- Il est testé par un testeur électrique et, en cas d’issue positive, le caisson est marqué au laser.
- La dernière vanne est assemblée sur la troisième table tournante avant le déchargement par l’opérateur.
Stations manuelles
- Haute efficacité = 90%.
- Haute flexibilité des procédés d’assemblage : les stations manuelles permettent de modifier et/ou de mettre à jour le procédé d’assemblage avec des améliorations mécaniques.
- Possibilité de changer d'opérateurs : ils sont guidés par l’écran d'ordinateur pendant les opérations manuelles. Même les nouveaux opérateurs sont ainsi d’une extrême efficacité.
Stations Automatiques
- Haute efficacité = 90%.
- Procédé hautement automatisé : toutes les opérations délicates sont prises en charge par le dispositif automatique, en laissant les tâches d’assemblage simples aux opérateurs.
- Possibilité de changer d'opérateurs : ils sont guidés par l’écran d'ordinateur pendant les opérations manuelles. Ceci permet aussi aux nouveaux opérateurs d’être d’une extrême efficacité.
- Définies selon les exigences du client
Stations manuelles
Temps de cycle 100% | 239 s |
Temps de cycle 90% | 262,9 s |
Produits |
15,6 pièces / heure |
Rendement | 90% |
Stations Automatiques
Temps de cycle 100% | 210 s |
Temps de cycle 90% | 233 s |
Produits | 17 pièces / heure |
Rendement | 90% |