Monitoring Solutions for Single, Double and Multi Blow Header
Brankamp monitoring systems detect process failures, protect the machine and tool from overloads, improve the quality of the produced parts and support the operator in quicker machine set-up. In case of production problems (e.g. punch breakage or double parts), they stop the machine early in order to prevent or minimize costly damage to the machine and tool. Quality defects on produced parts (e.g. head cracks), that often occur individually and randomly on work pieces trigger a sorting device without interrupting the production. The failure detection is carried out by a 100% in-process monitoring of all produced parts that are produced on single, double or multi blow header.
All Brankamp monitoring systems offer the operator a well-founded insight into the stability of the forming process through a powerful graphic display. The associated process signals can be evaluated and the current values of the various counter settings (order, tool and maintenance counters etc.) can be checked. All set and learned limits can be stored under an article or product number. These reference curves are available to the operator for fast, reproducible resetting. Runtime analyses (Stop & Go diagram) as well as frequency distributions of shutdown reasons enable a well-founded failure analysis which can be used to increase productivity.
Our goal is to support our customers in achieving the highest productivity and manufacturing quality. Brankamp monitoring systems are the key to efficient machine, tool and quality monitoring whenever millions of parts are produced monthly.
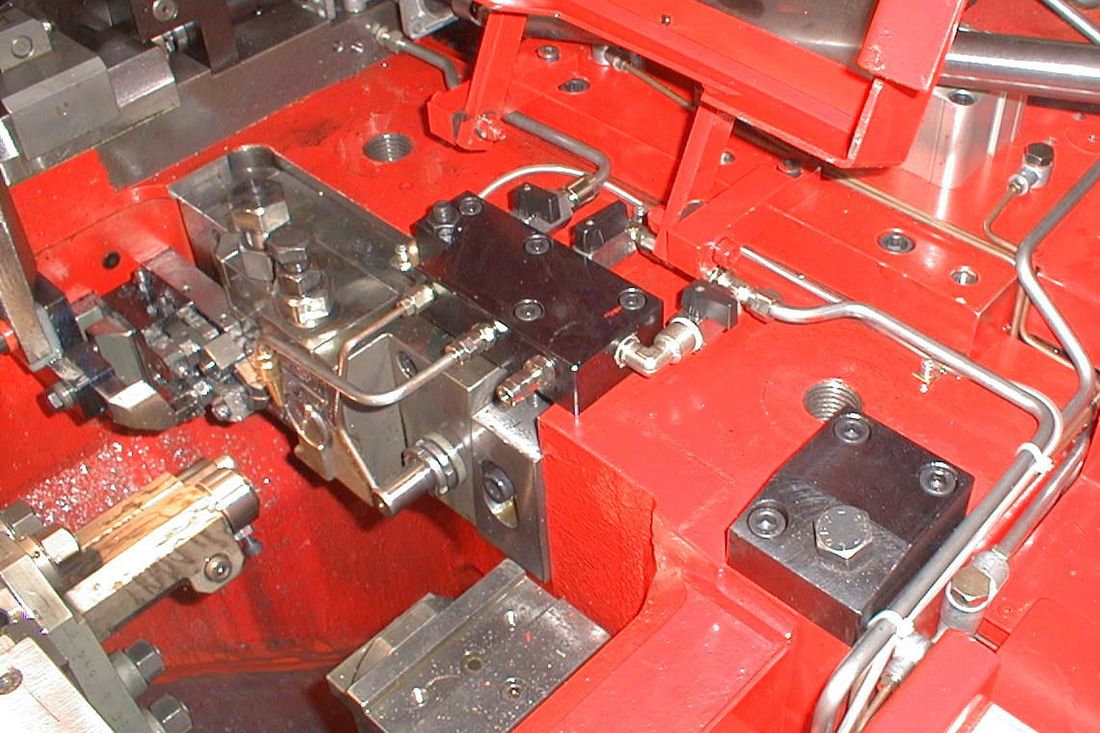
- Precise machine and tool protection to avoid consequential damage and downtimes, reduction of repair costs
- Detailed monitoring of the produced part quality to improve the quality level (0 ppm)
- Increased productivity through extended runtimes, reduced downtimes and optimized production speed
- Reduction of tool and scrap costs through early failure detection
- Insight into the process to reduce set-up times and optimize production
- Operator support through various counters for piece counting (good and bad parts), recording of shift performance and tool life, counters for quality inspection and maintenance intervals, parts/crate and dosing counter.
- Recording of article-related productivity distributions (production, set-up, stop, rejects) enable precise calculation of part costs
- Network interface for communication with external programs (MDE/BDE/MES, Teleservice, IoT)
- Comprehensive documentation of production allows precise runtime analysis and failure tracking
How it works
Force sensors are installed as standard in the hard plate, the base plate or in special cases on the punch side, in the ejector (rivet production) or if calibrated in the machine frame. In addition, the wire stop force can be included in the monitoring by a special evaluation channel (ball and roller production). Further sensor signals such as temperature (semi hot forming), pressure or power can be acquired and evaluated by the Brankamp monitoring system for condition monitoring on the machine.
Special features
- SYSTOMATIC for the identification of systematic (permanent) process faults
- WIRE FEED AID for an optimum setting on the feeding system
- HD ZOOM for a more detailed monitoring of specific process areas