Monitoring Solutions for Lathes and Turning Centers
Various factors significantly influence the quality of a workpiece. This includes the condition of the machine and the tool, the coolant used as well as the specific machining process and the raw part.
Based on set limits, the MARPOSS monitoring solutions monitor the relevant influencing factors or a defined part of them.
Machine protection is another important requirement that is met by MARPOSS monitoring systems, thus helping to minimize consequential damage and costs caused by collisions. This also avoids unplanned downtimes.
Machine protection can be permanently active – in manual operation and throughout the cutting process – even while the status of machines and their components is recorded during special spindle and axis movements.
The tools used are often a significant cost factor of the cost per unit. Therefore, the avoidance of tool breakage and the optimization of tool life represent another benefit of MARPOSS tool and process monitoring.
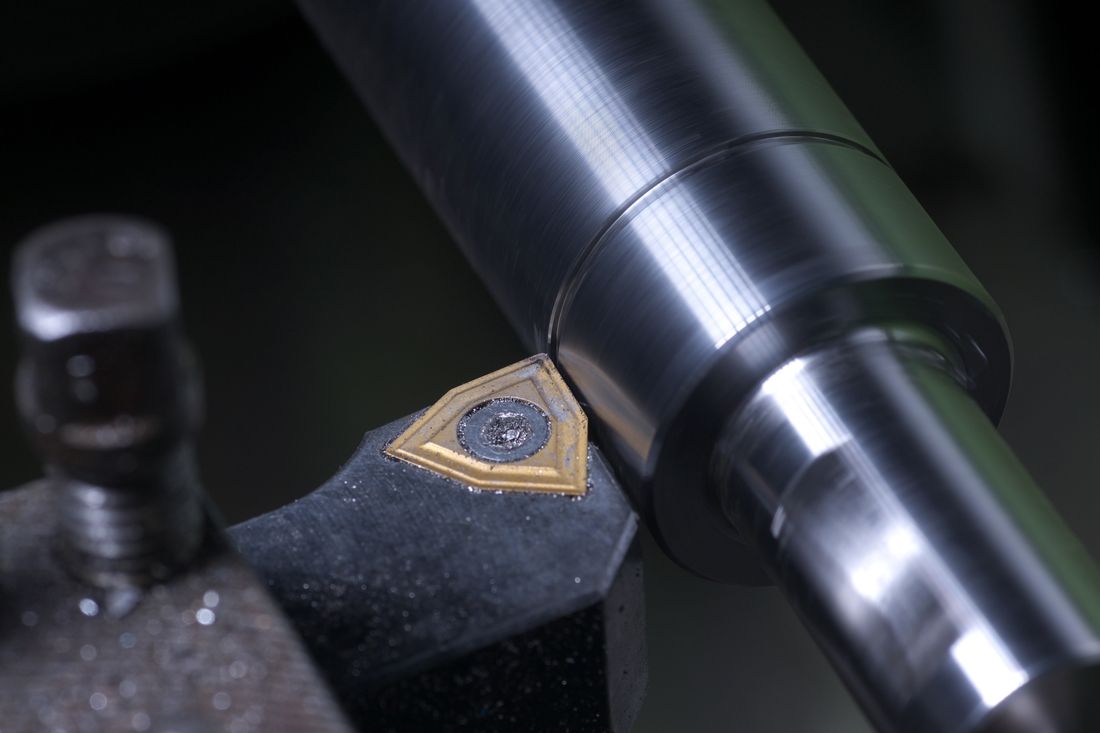
The main areas of application for ARTIS monitoring systems are:
- Machine protection
- Machine monitoring
- Tool and process monitoring
The systems are scalable and can therefore be individually adapted to machine designs, machine controls and user requirements. In this way, stand-alone and complex systems can be mapped equally (modularity).
The monitoring systems record relevant digital or analog sensor signals in real time (parallel) and evaluate them accordingly. In most cases, spindle or axis power signals are sufficient to reliably detect e.g. tool wear based on defined limits.
Multi signal monitoring (“multi-criteria”) is also possible and uses power, vibration and coolant flow signals to also detect small anomalies by means of special monitoring strategies.
To activate warnings or alarms signal limits can be set automatically or be defined individually by the user.
Permanent storage of the recorded data allows further evaluations.
- Machine protection: detection of collisions and limitation of their effects
- Machine condition: prevention of unplanned machine down times / use of collected data to control predictive maintenance / "chip in spindle" detection
- Tool and process monitoring: avoidance of tool breakage, scrap or further damage by setting individual limit values / optimization of tool life / Optimized feed control by using the Adaptive Control option
- Enables 24/7 or lights-out processing
- Provision of process visualization, analysis and optimization tools
- Helps to reduce costs per piece
Machine protection:
VM-02, CMS-02 / stand-alone or integrated in GENIOR MODULAR (GEM)
Machine monitoring:
VM-03, TMU-RO / stand-alone / VM-03 can be integrated into GENIOR MODULAR
VM-03 VisuScope for on-line and off-line evaluation of monitoring signals
Tool and process monitoring:
TMU-TP, GENIOR MODULAR, CTM / TMU-TP stand-alone or can be integrated in GENIOR MODULAR
Sensors, amplifiers and converters, displays and operating elements, as well as software modules